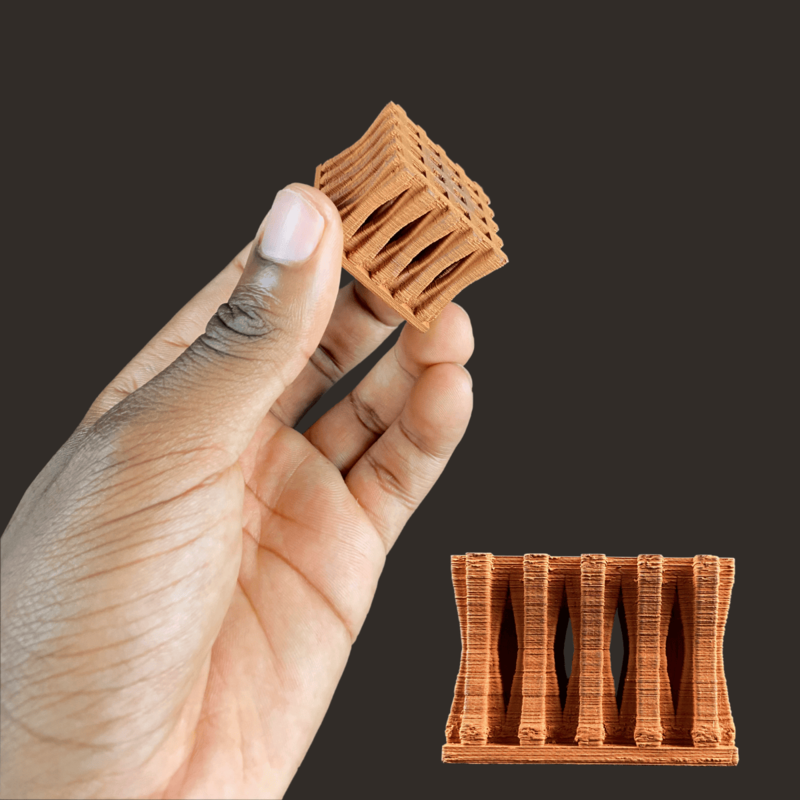
Metal Alloys - 3D printing Copper 999
Don't compromise on material quality - use industrial-grade materials at unbeatable prices.
Copper is a metallic material much appreciated for its high thermal and electrical conductivity, as well as for its ductility. Paradoxically, these same characteristics have made 3D printing very difficult for years.
The use of MIM raw materials makes copper alloy parts easy to produce (compared to alternative technologies such as laser fusion or even filament extrusion).
Originally intended for injection molding, these compounds are compatible with Pollen AM 3D printers. Pollen AM recommends Polymim GmbH's MIM raw materials.
The use of MIM feedstock allows the process of future metal alloy parts at low temperatures. Initially aimed at injection molding, these compounds are compatible with the Pollen AM Pam 3D printers.
Once formed, the parts will undergo a set of chemical and thermal post-treatments to give the parts the correct material properties. (Debinding / Sintering).
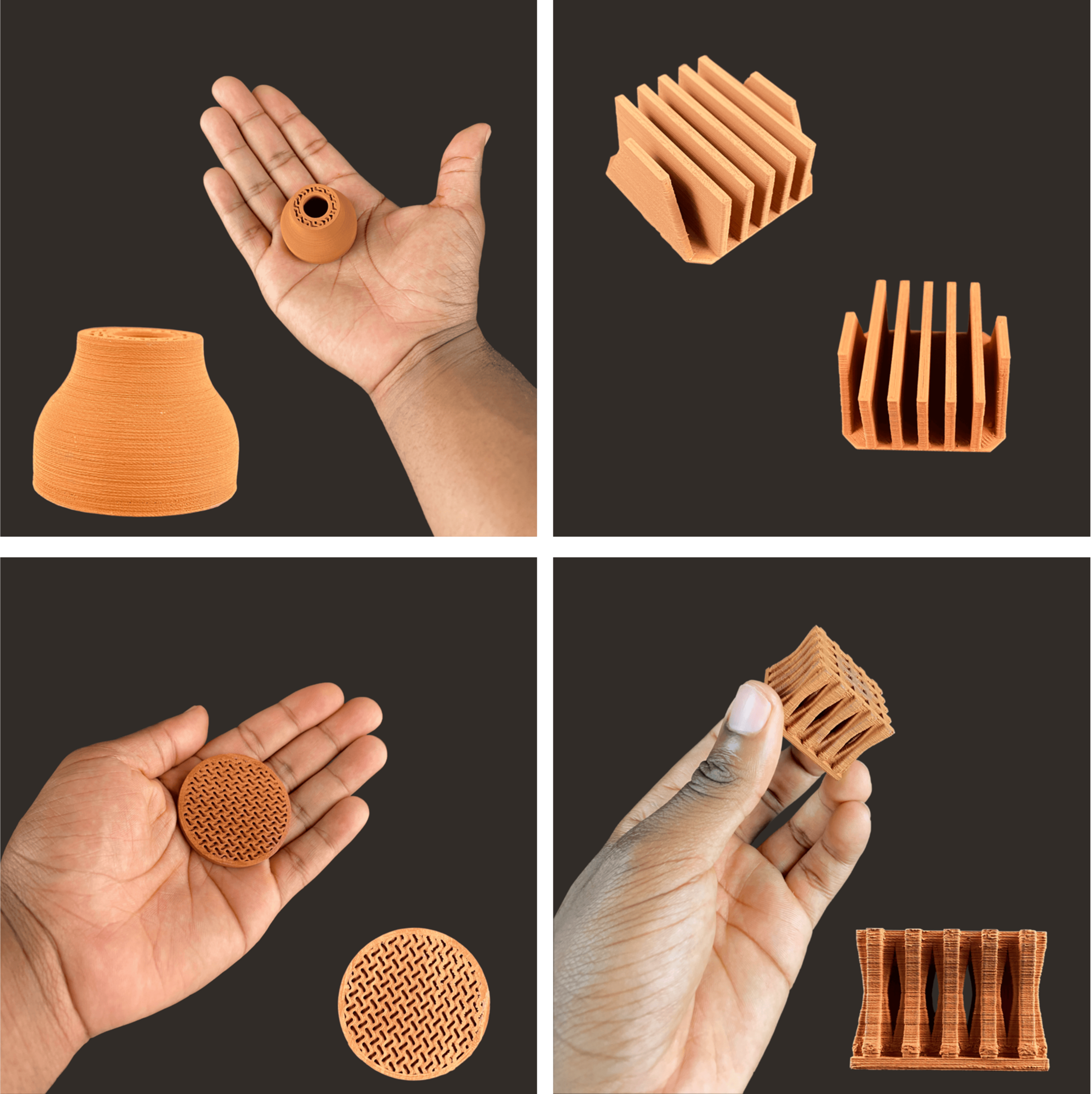
These parts above are captured in their green states, you will discover the parts after the sintering process in the parts gallery.
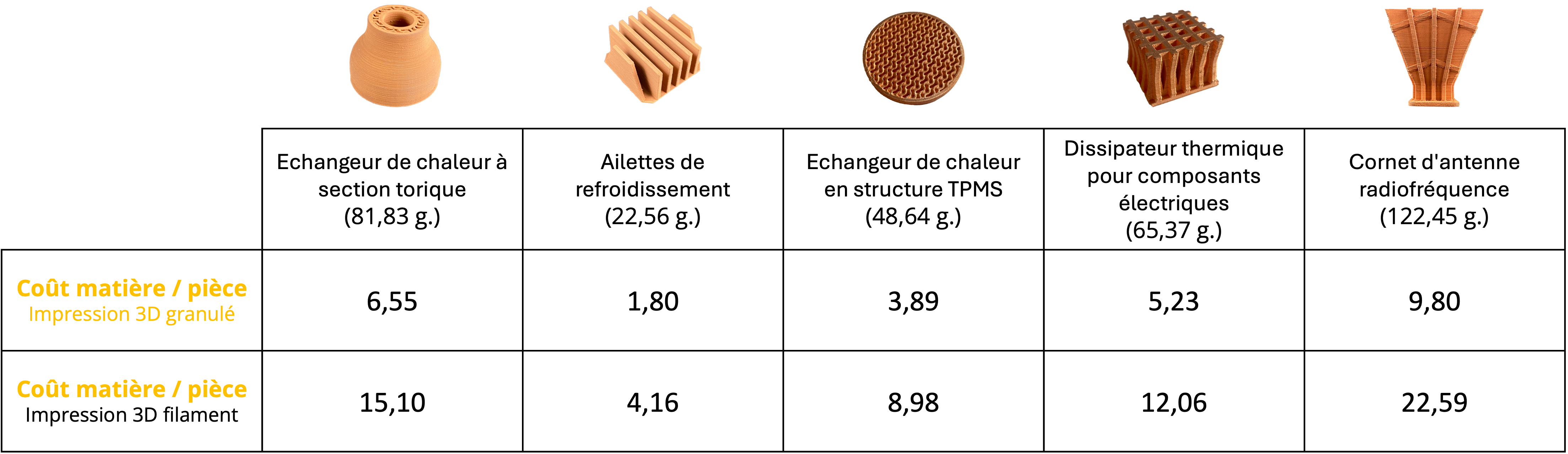
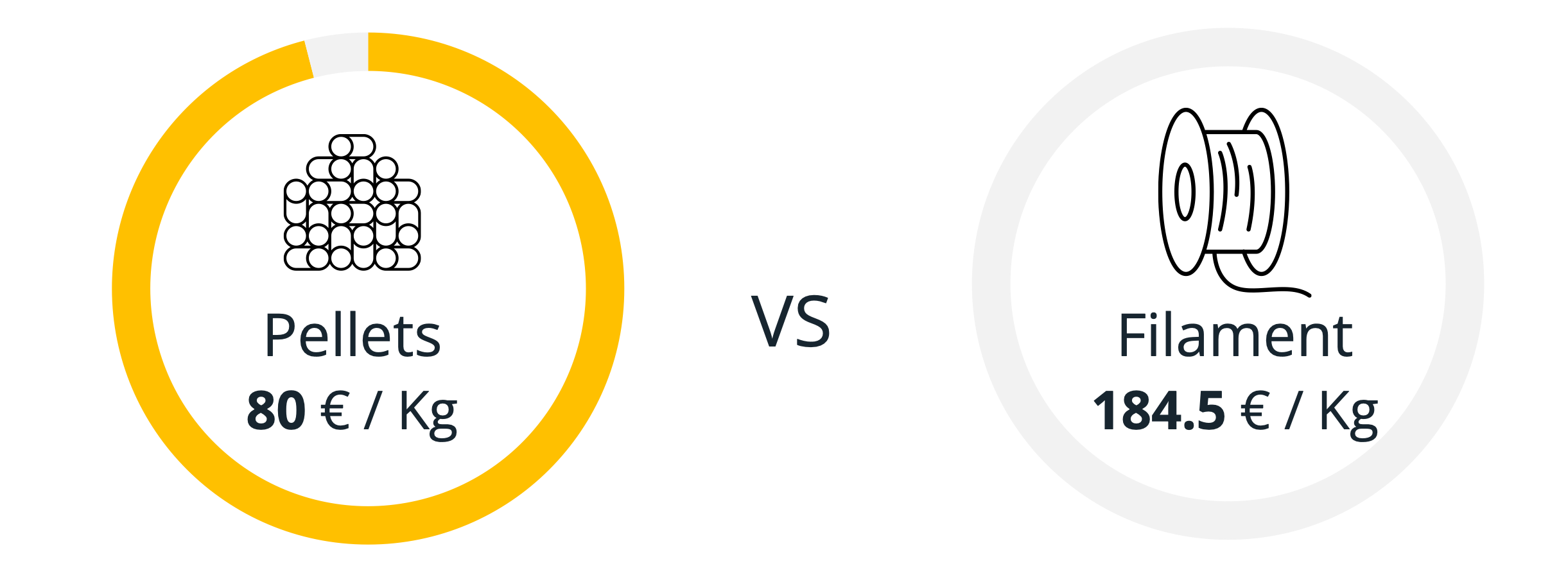
The use of industrial compounds in pellet form makes it possible to produce parts at a lower cost, comparable to manufacturing by injection molding, within shorter delays and with no tooling cost.
Considering 3D printing manufacturing, the use of compound in pellets form is the cheapest solution on the market to produce metal parts. (Pam vs. FDM, Binder Jetting, SML)
Process presentation
These parts were 3D printed using a Copper 999 feedstock for metal injection moulding.
Feedstock presentation
The feedstock is based on an copper powder (Cu999), and a thermoplastic binder system for the powder injection moulding process.
Green parts need a binder removal in a two-step debinding process before being sintered. ( Discover the process)
First debinding step is dissolving the binder in a water bath.
In the second debinding step the remaining binder is thermally removed.
These general guidelines are based on the processing of test parts with a wall thickness of 5 mm.
Cu | Fe | O | |
< | balance | 0,10 | 0,05 |
Specifications | General Tolerances | Normal density |
1,1570 | ± 0,0042 | 8,69 g/cm3 |
as Sintered | |
Density | ≥ 8,60 g/cm3 |
Yield strength - Rp02 | ≥ 50 MPa |
Tensile strength - Rm | ≥ ±210 MPa |
Elongation A10 | ≥ 40 % |
Hardness | ≥ 40HB |
Microsructure
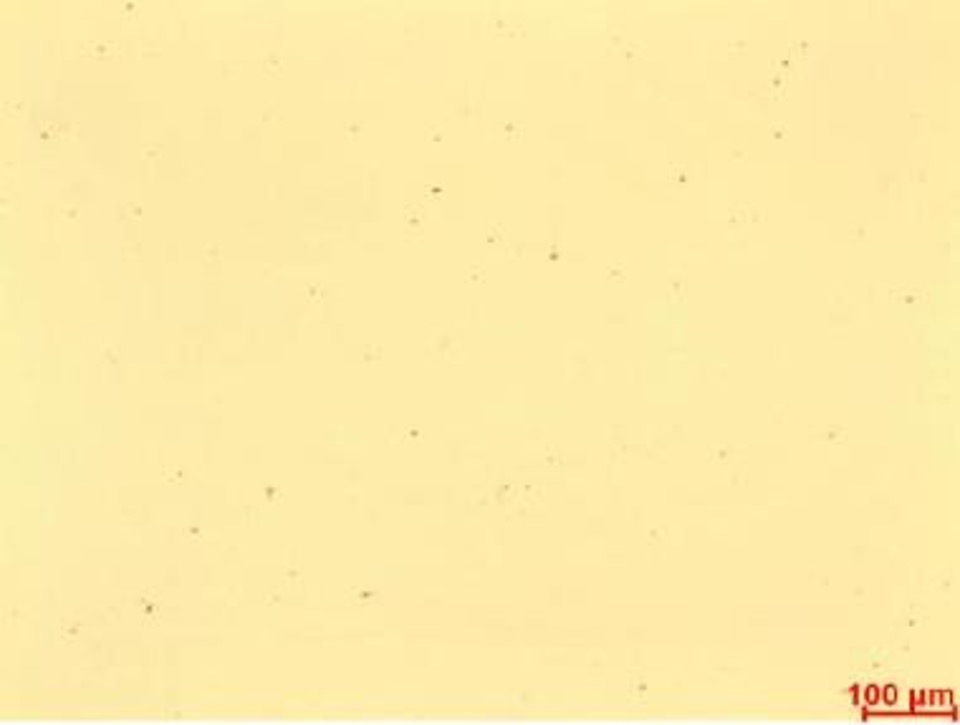
3D printing parameters

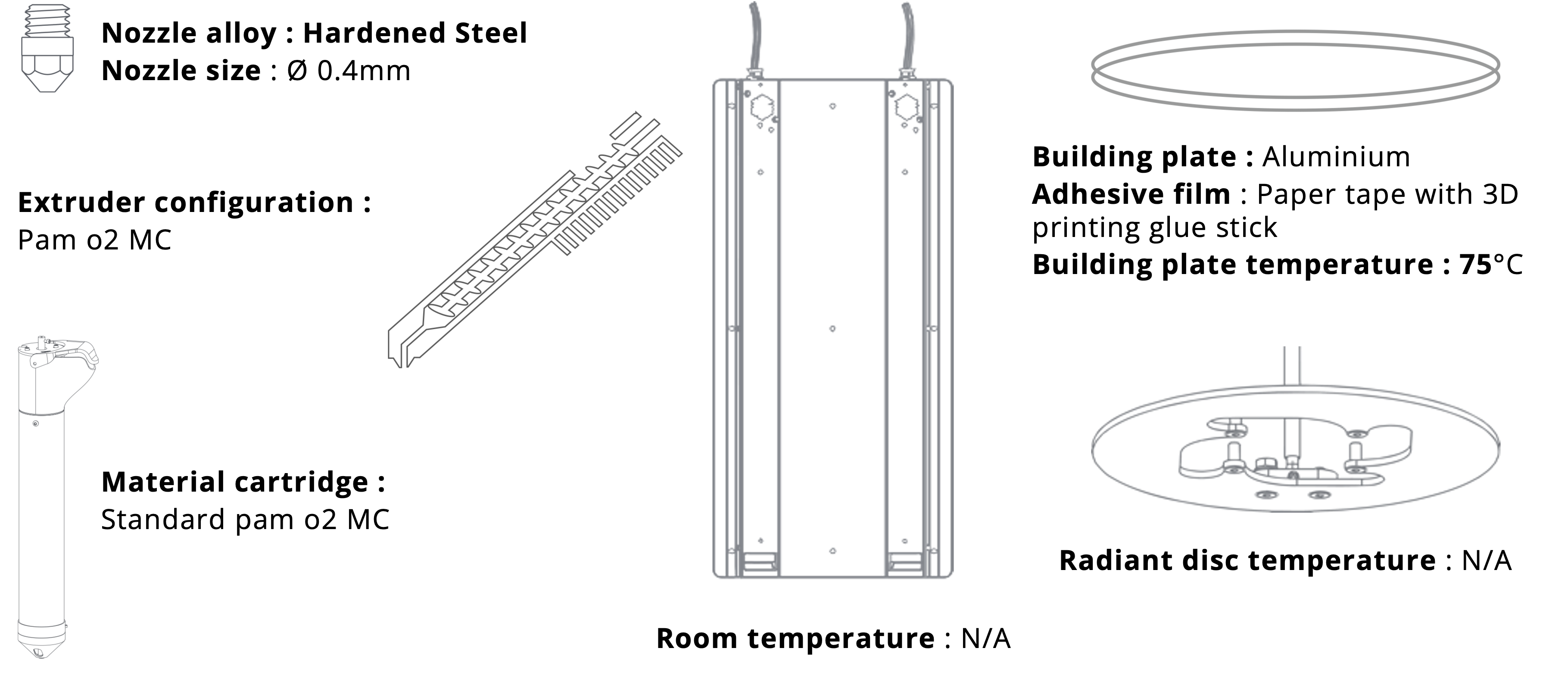
Debinding process
Debinding solvent | Destilled water (for Master- Alloy: with corrosion inhibitor, i.e. 2, Vol% added "DST-PAS/1" from company "DST-Chemicals A/S") |
Debinding temperature | 40 - 60 °C |
Debinding time | depending on part thickness, (i.e. 4mm part: approx. 10h at 60°C) |
Drying process | to constant weight - approx. 3h at 85°C |
Oversize factor | Weight loss |
1,1570 | ≥ 3,2 w% |
Sintering process
Sintering atmosphere | 100% dry hydrogen |
Sintering substrata | Non-metallic base (e.g. Al2O3) |
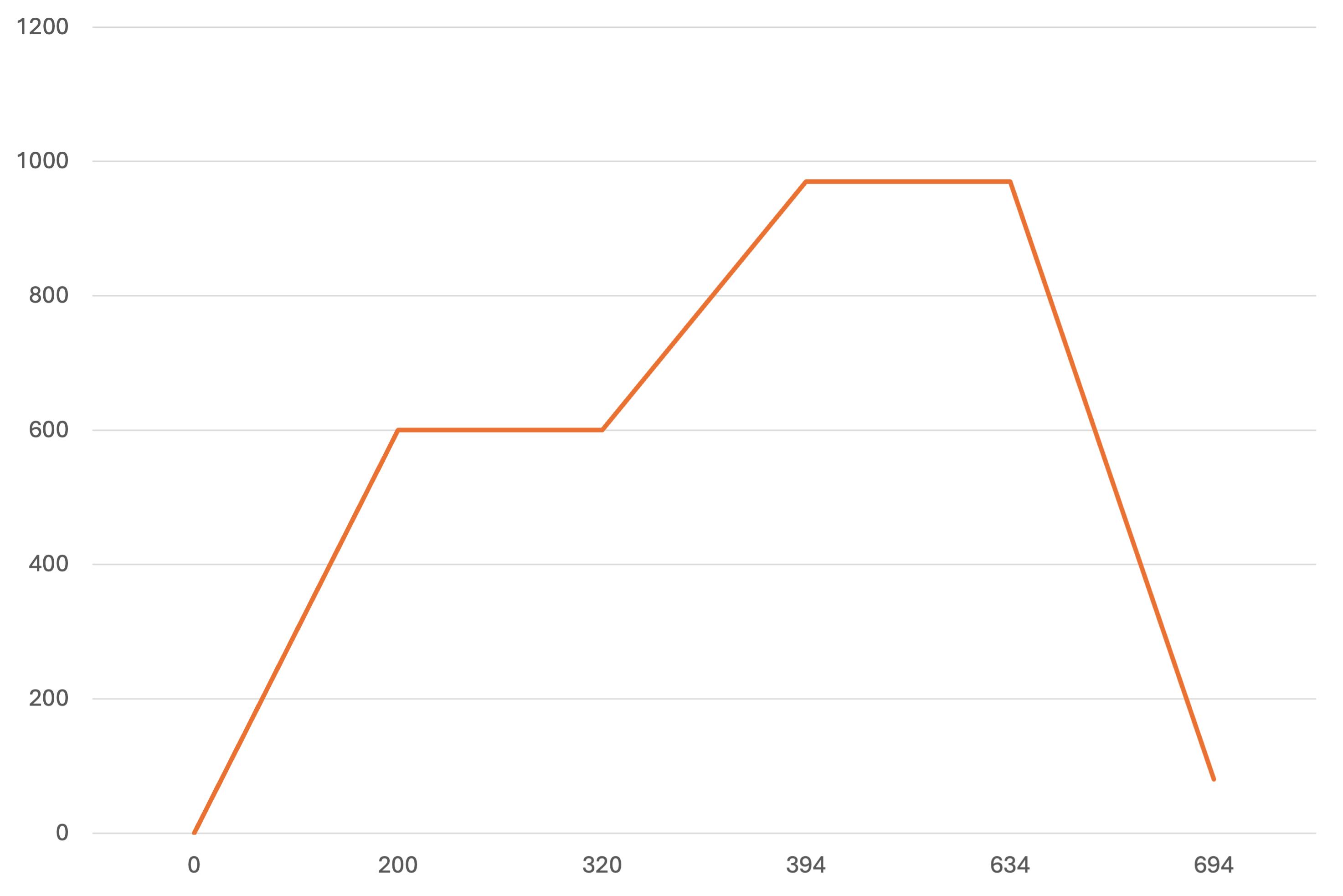
Description | Temperature | Rate |
Heating up to | 600°C | 3 K/min. |
Debinding at | 600°C | hold 2 h |
Heating up to | 970°C | 5 K/min. |
Sintering at | 970°C | hold 4 h |
Cooling down to | 80°C | 15 K/min. |
To know more about the 3D printing process, contact our expert team !
Discover 3D printed parts in Copper
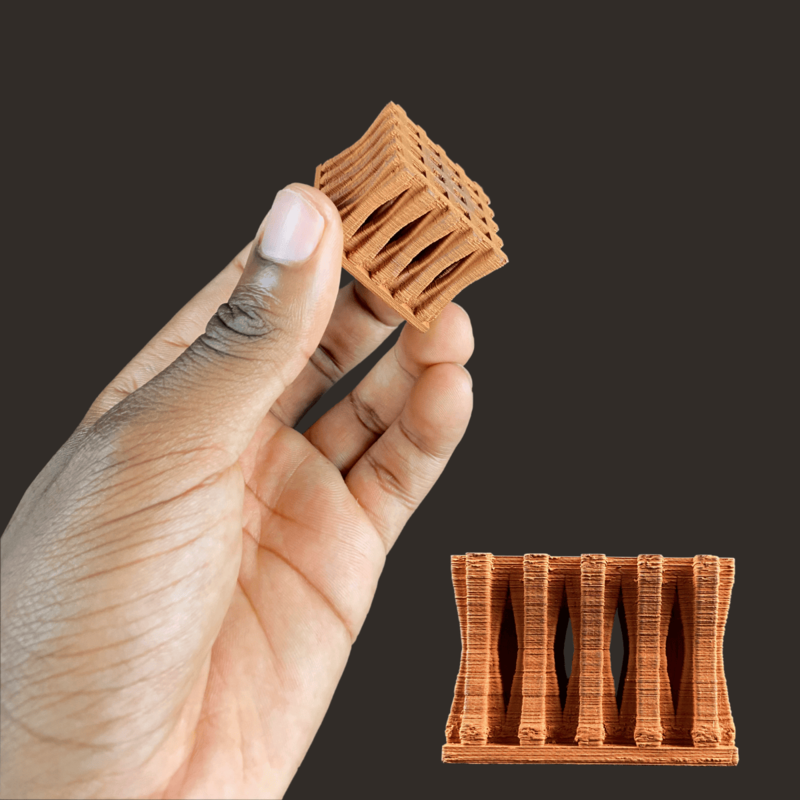
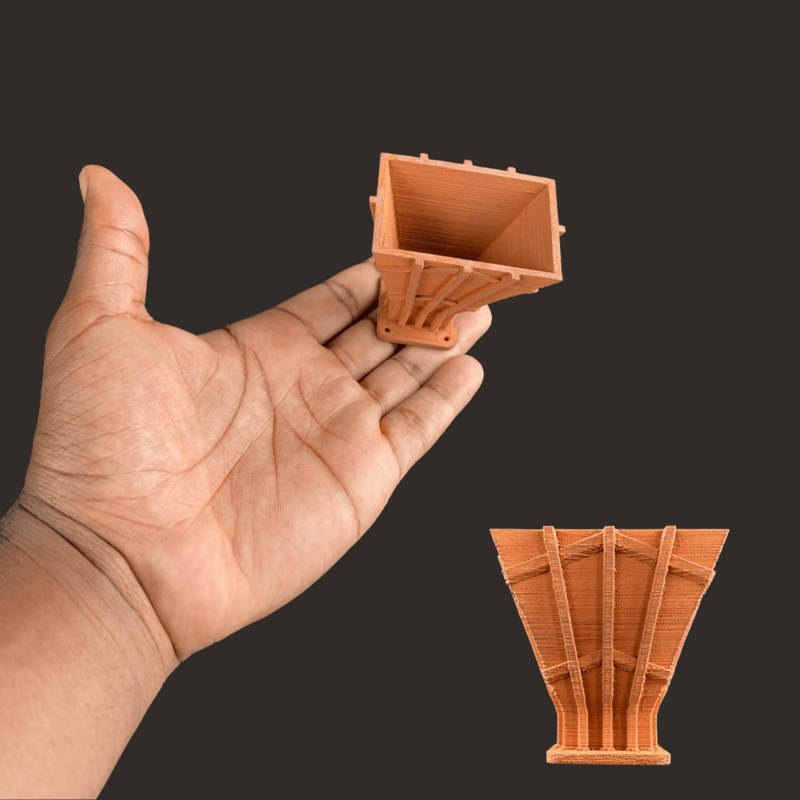
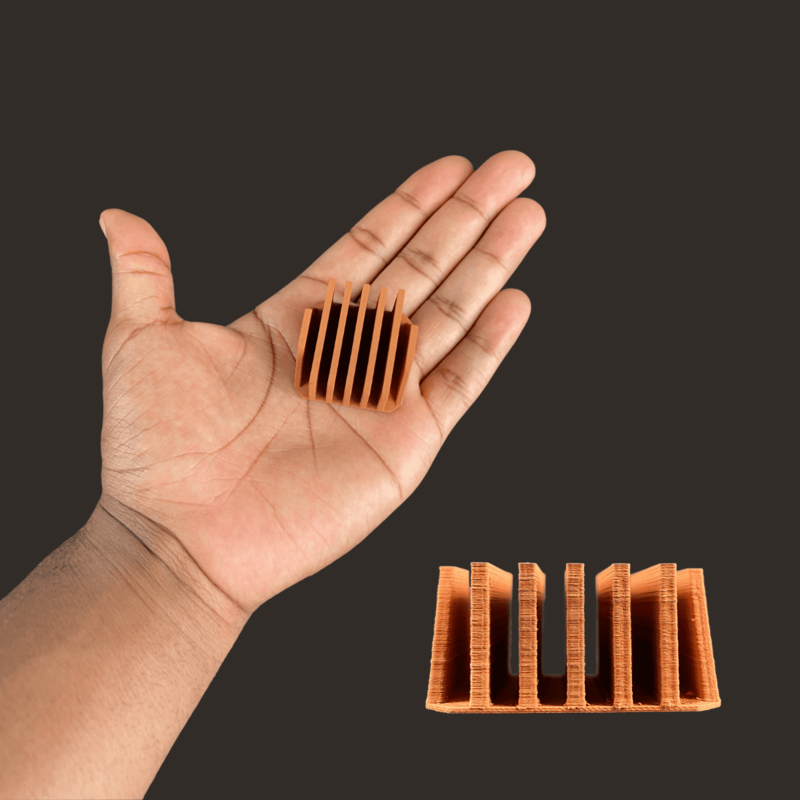
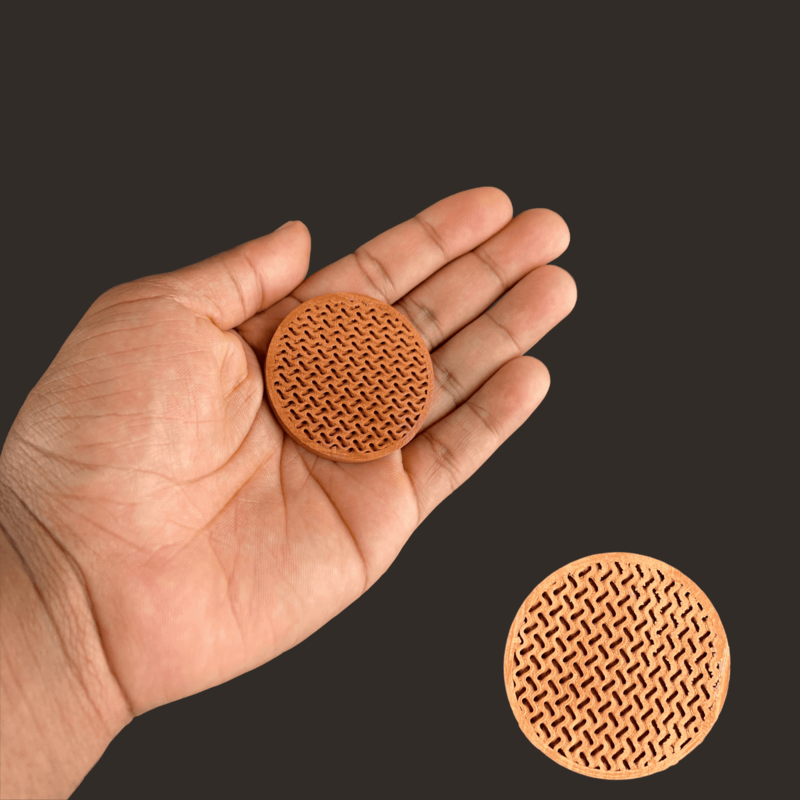
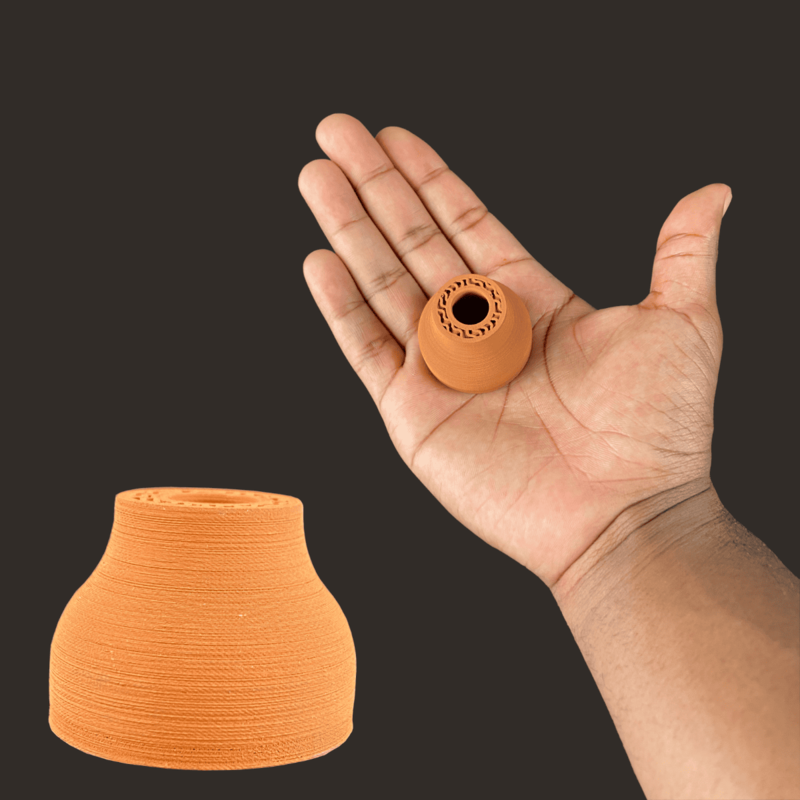
Let’s dive into the possibilities offered by PAM
From pellets to object, PAM technology offers the most direct process to high performances end-parts.
Metals Ceramics Commodity Elastomers Performance High Performance.
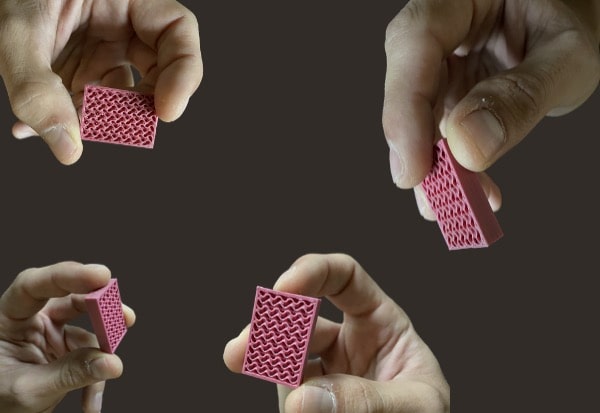
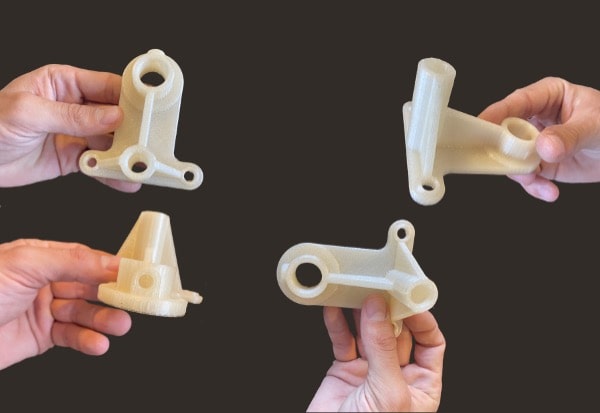
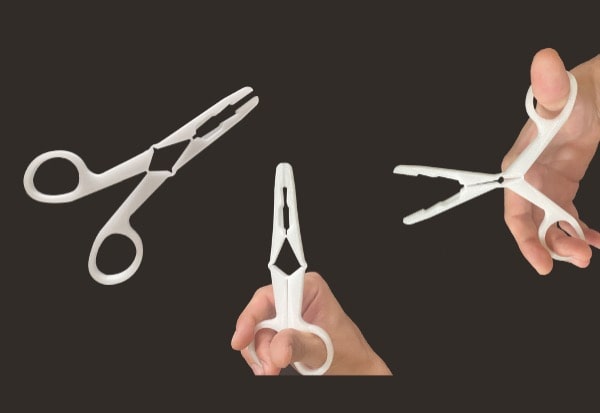
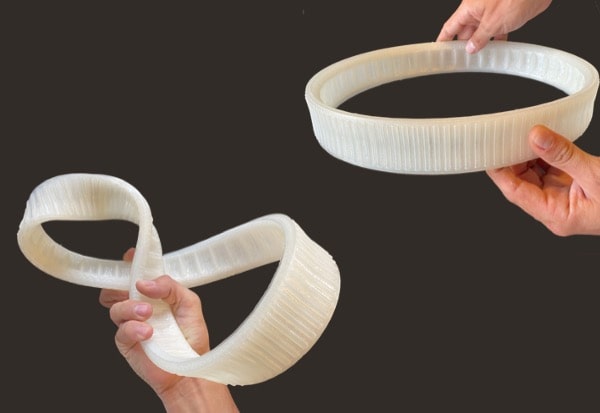
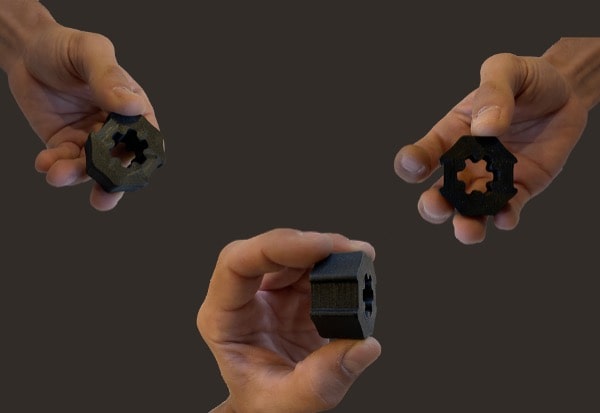