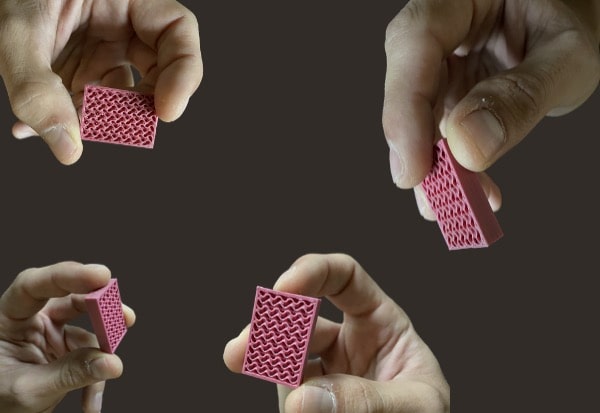
PIM process
A proven industrial process
suitable for 3D printing
PiM is a manufacturing process based on thermoplastic injection moulding and powder metallurgy and ceramic processing.
It allows the conception and the production of metallic & ceramic parts following the same mode as injection moulding. Used raw material, or feedstock PiM, is a mix of fine powder and thermoplastic binder, pelletized.
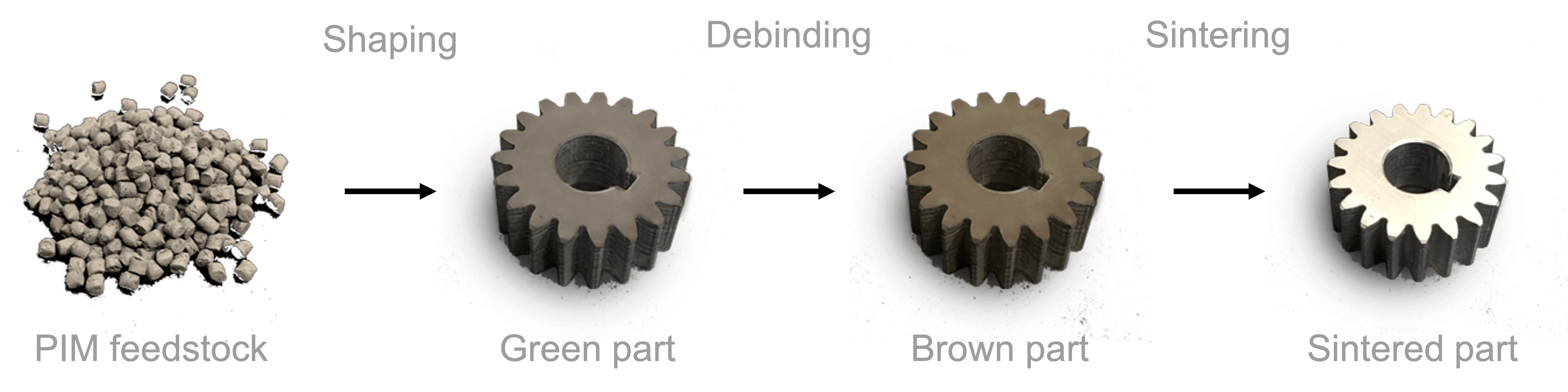
Since then, the MIM market has grown enormously and covers a wide range of industrial applications, such as the automobile, watchmaking, defence, aerospace, medical (prostheses, implants, probes, etc.), connectors, etc. In short, we all cross paths in our daily lives and without being aware of the parts resulting from the MIM processes.
PiM process is an indirect part manufacturing process, that is to say; you obtain a 100% metal or ceramic part it is necessary to post-treat the formed parts. Overall, the PIM process is broken down into three main stages.
Discover Metal and Ceramic 3D printed parts
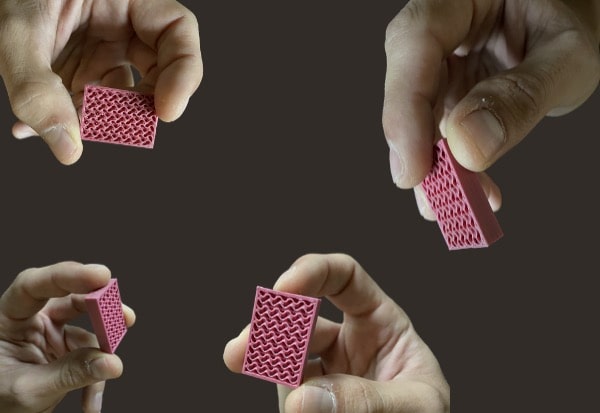
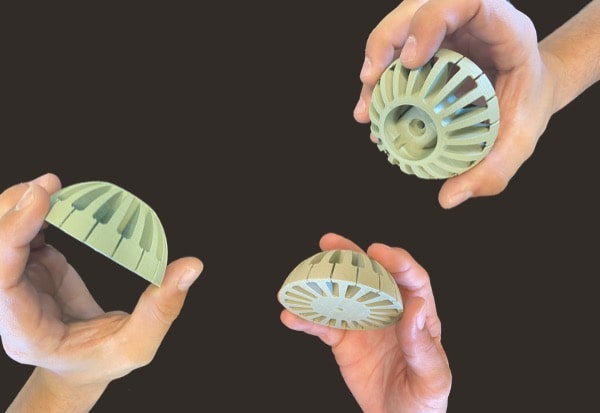
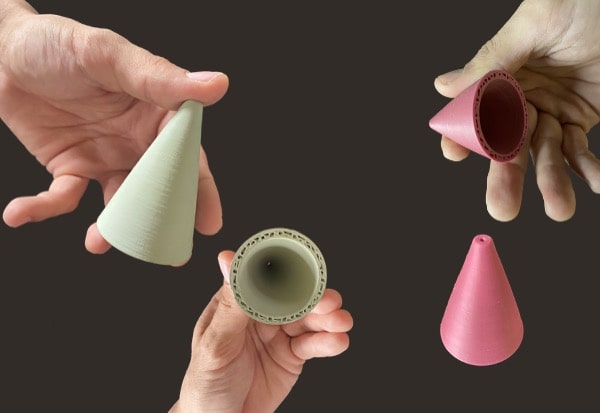