Decathlon is investing in 3D pellet printing for the prototyping of compostable sports equipment – Primante3D DECATHLON Pulse, Pollen AM and KUORI: a winning alliance for the prototyping of compostable sports equipment – CAO DECATHLON Pulse, Pollen AM and KUORI: a winning alliance for the prototyping of compostable sports equipment. – Fluids and Lubricants
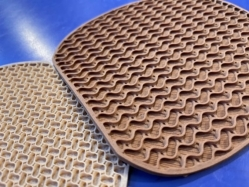
DECATHLON Pulse, Pollen AM et KUORI : une alliance gagnante pour le prototypage d’équipements de sport compostables
February 28, 2025 | Press
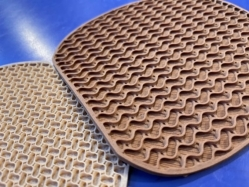
Decathlon is investing in 3D pellet printing for the prototyping of compostable sports equipment – Primante3D DECATHLON Pulse, Pollen AM and KUORI: a winning alliance for the prototyping of compostable sports equipment – CAO DECATHLON Pulse, Pollen AM and KUORI: a winning alliance for the prototyping of compostable sports equipment. – Fluids and Lubricants
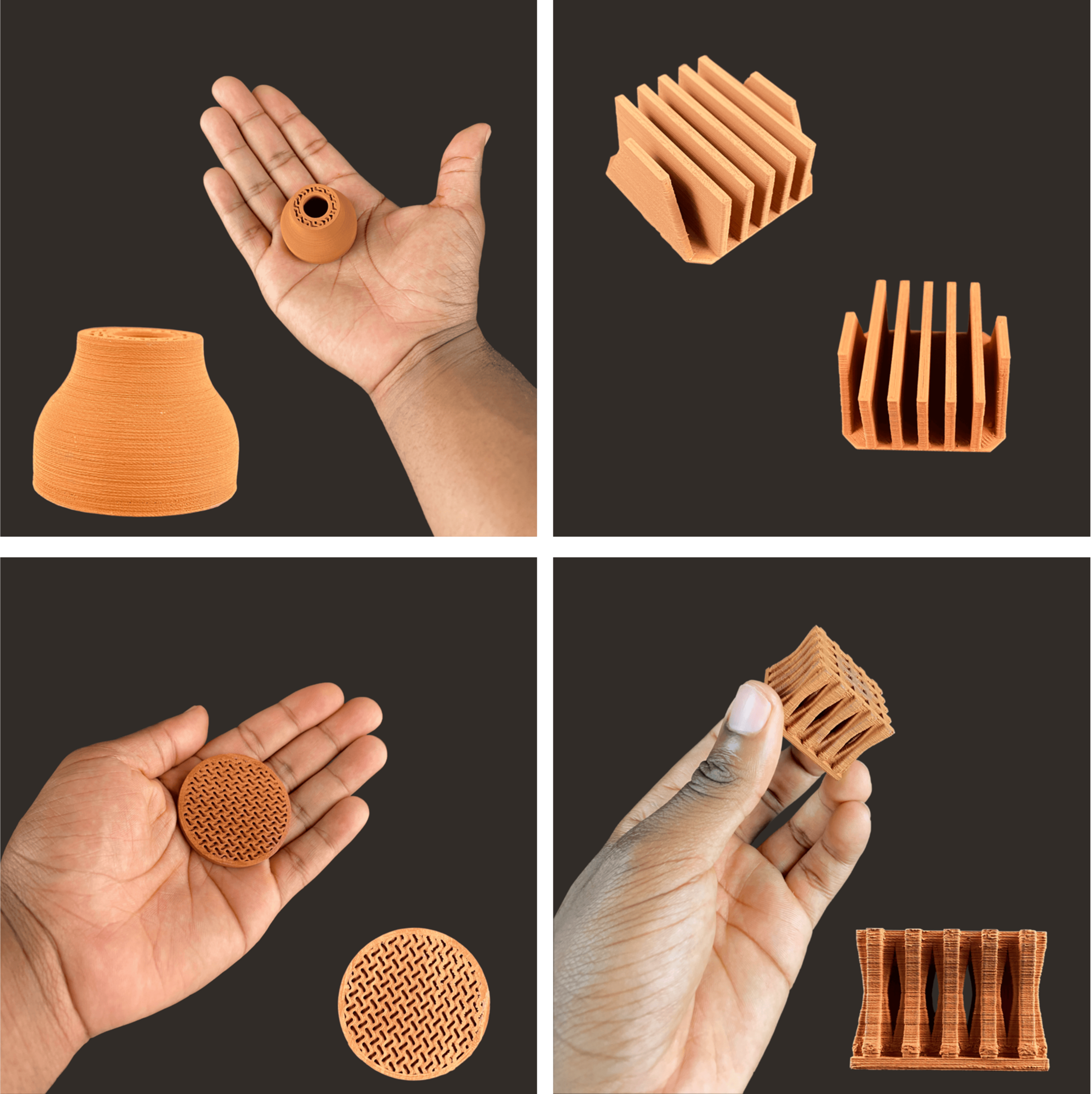
Copper MiM Feedstock
October 16, 2024 | Material
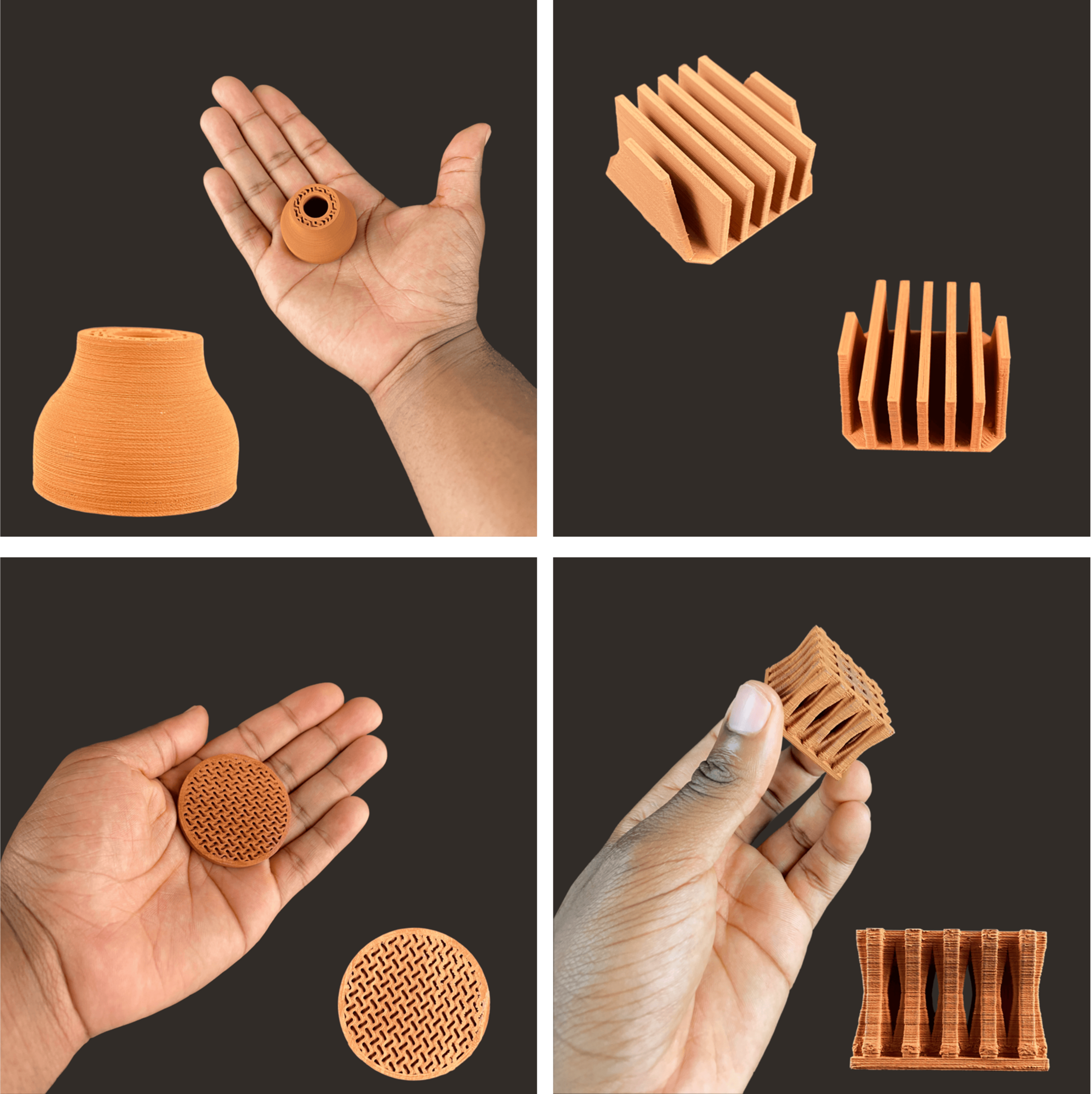
Printed copper parts can be used for a wide range of applications, including electronics, energy and construction. We are convinced that this technology will revolutionize the way we produce metal parts, offering unprecedented possibilities for customization and cost reduction.
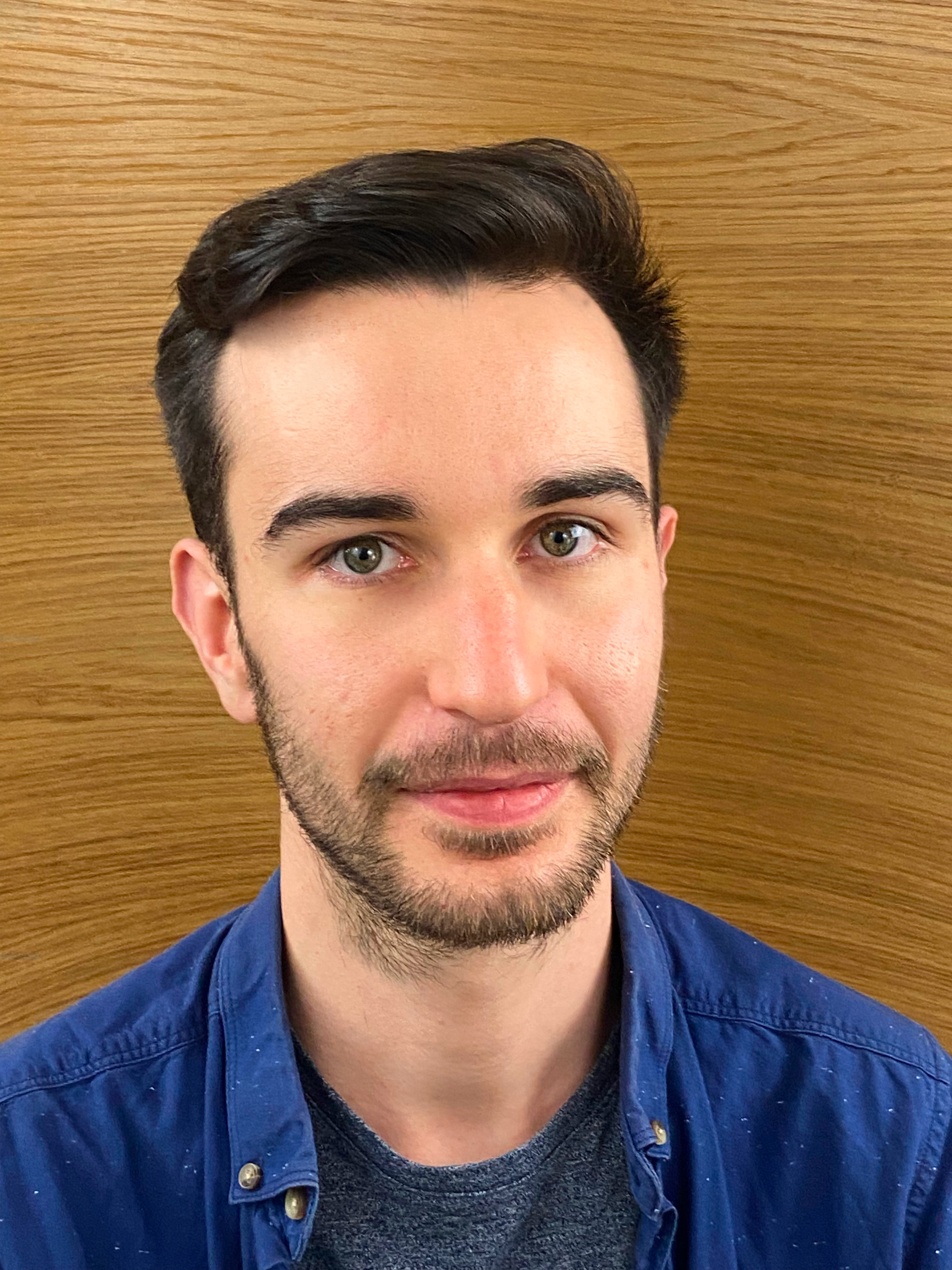
Interview with our collaborator: Fabien Lanoue
May 03, 2024 | Team
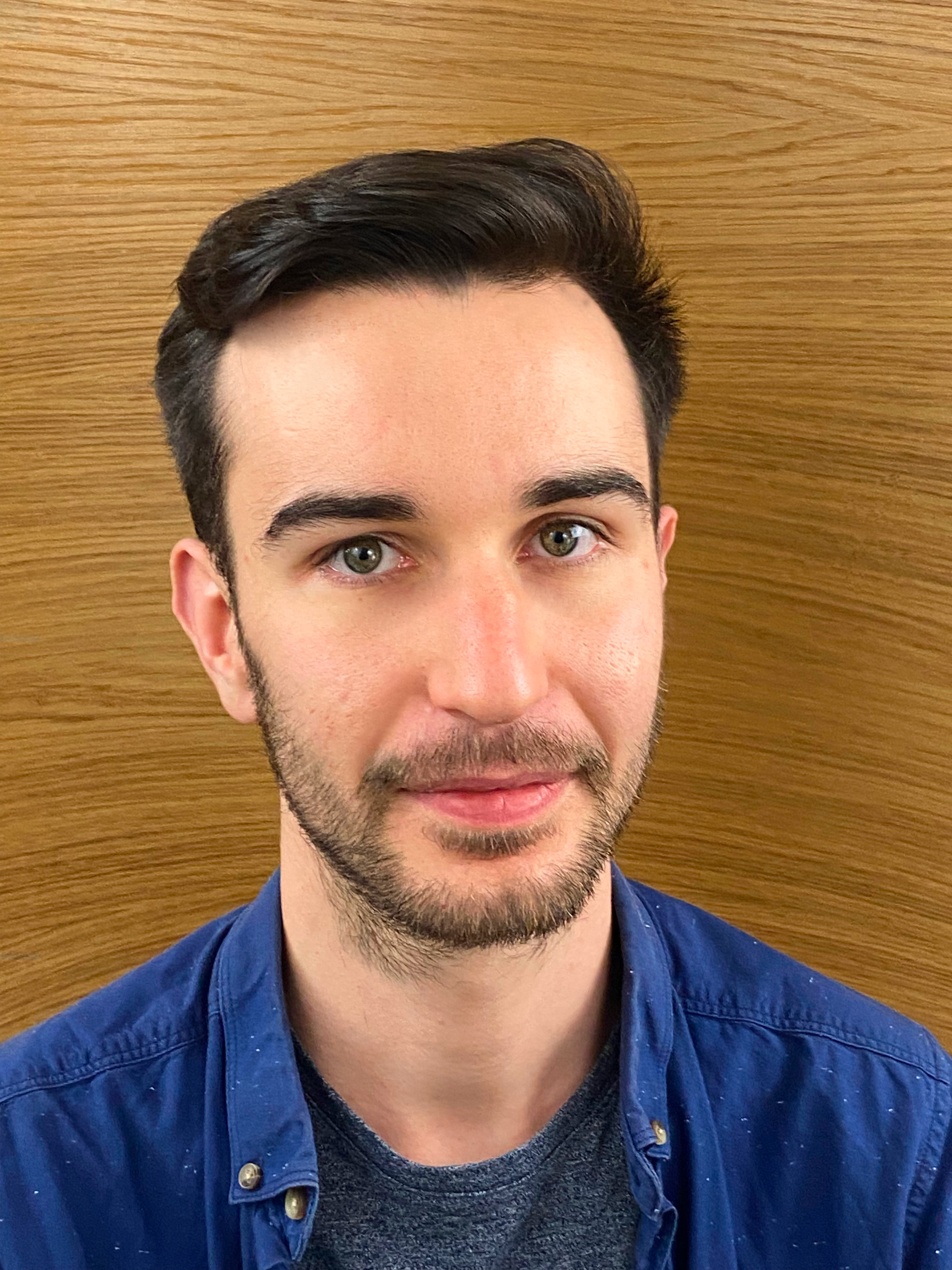
This is an opportunity for Pollen AM to introduce you to Fabien, who works closely with the PAM process and plays an essential role within Pollen AM.
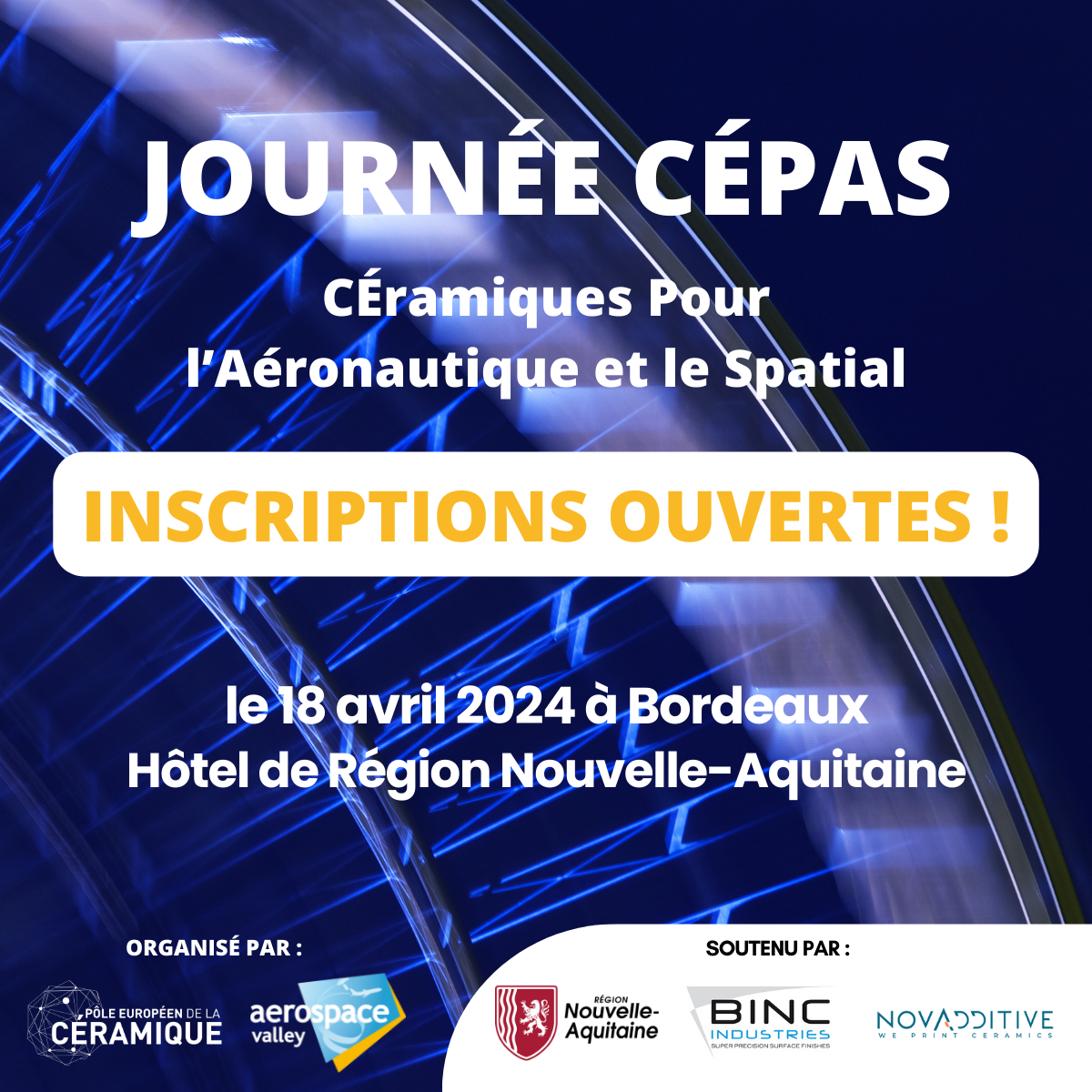
Pollen AM at CEPAS Day: Decarbonization of the Aerospace Industry
April 15, 2024 | Commitment
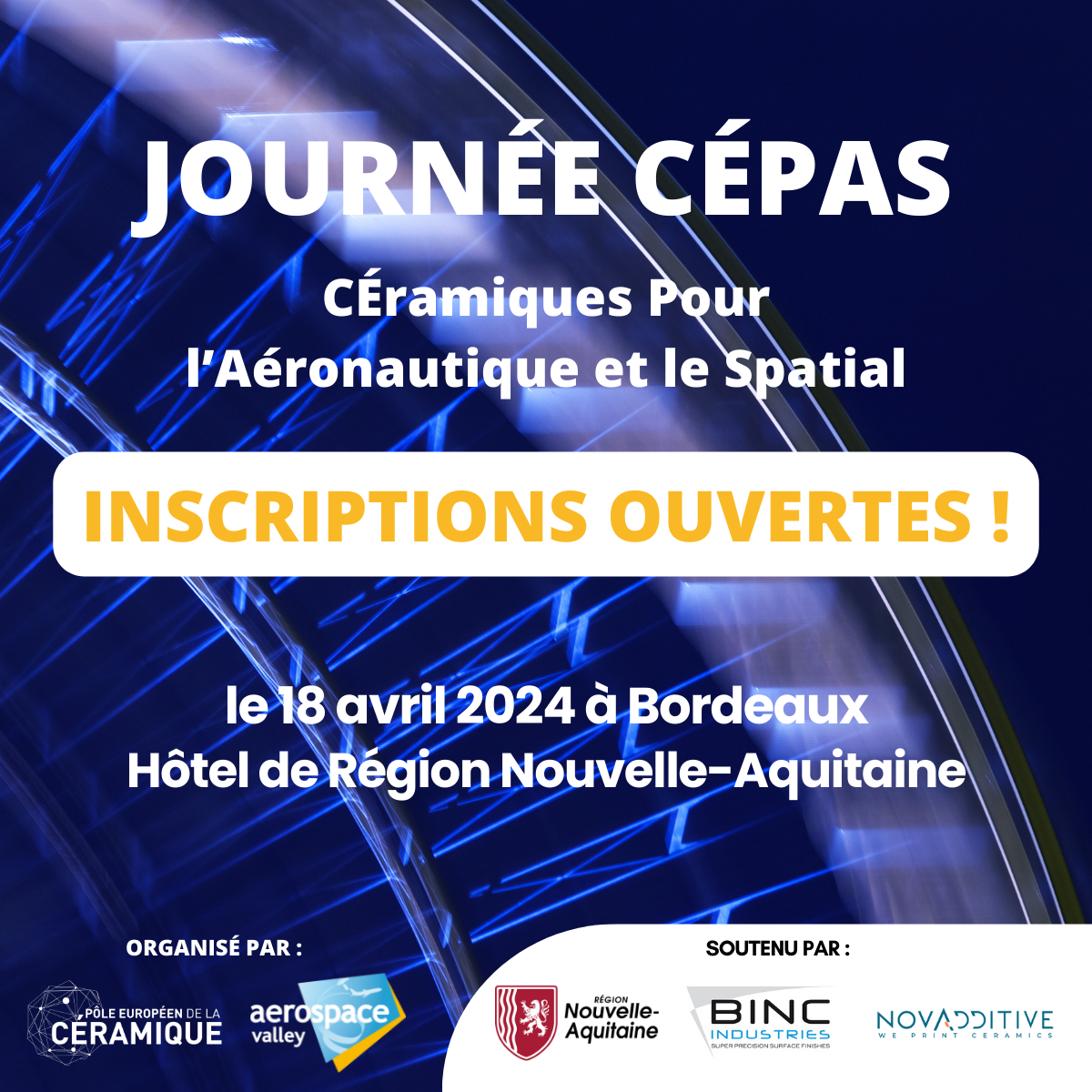
This day will be a unique opportunity to exchange knowledge, share experiences and explore the latest technological advances that are redefining the landscape of aerospace and space. We look forward to meeting key industry players and discussing future prospects for ceramics in the field of decarbonization.
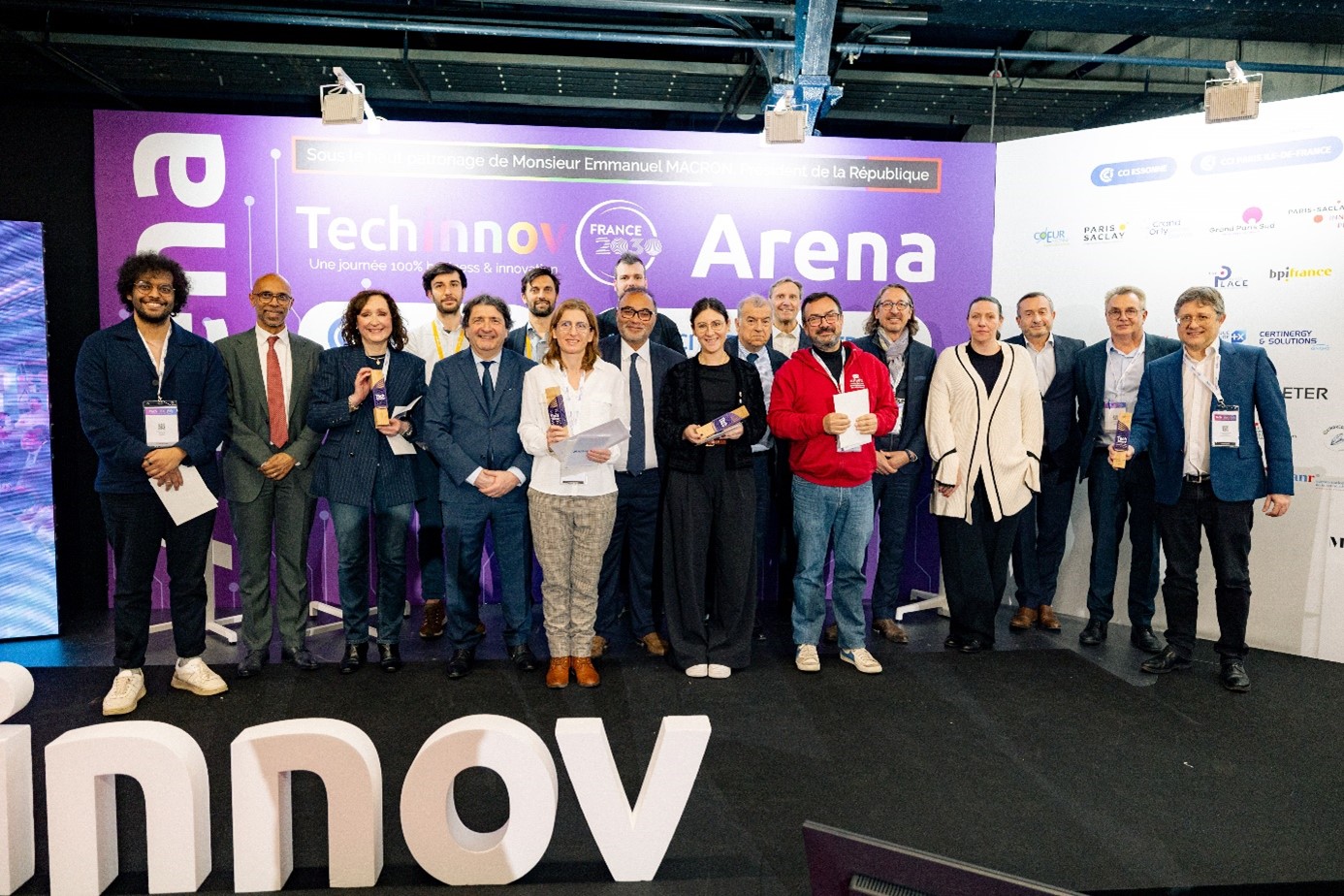
Pollen AM wins the Techninnov Contest in the Tech2030 category
March 26, 2024 | Event
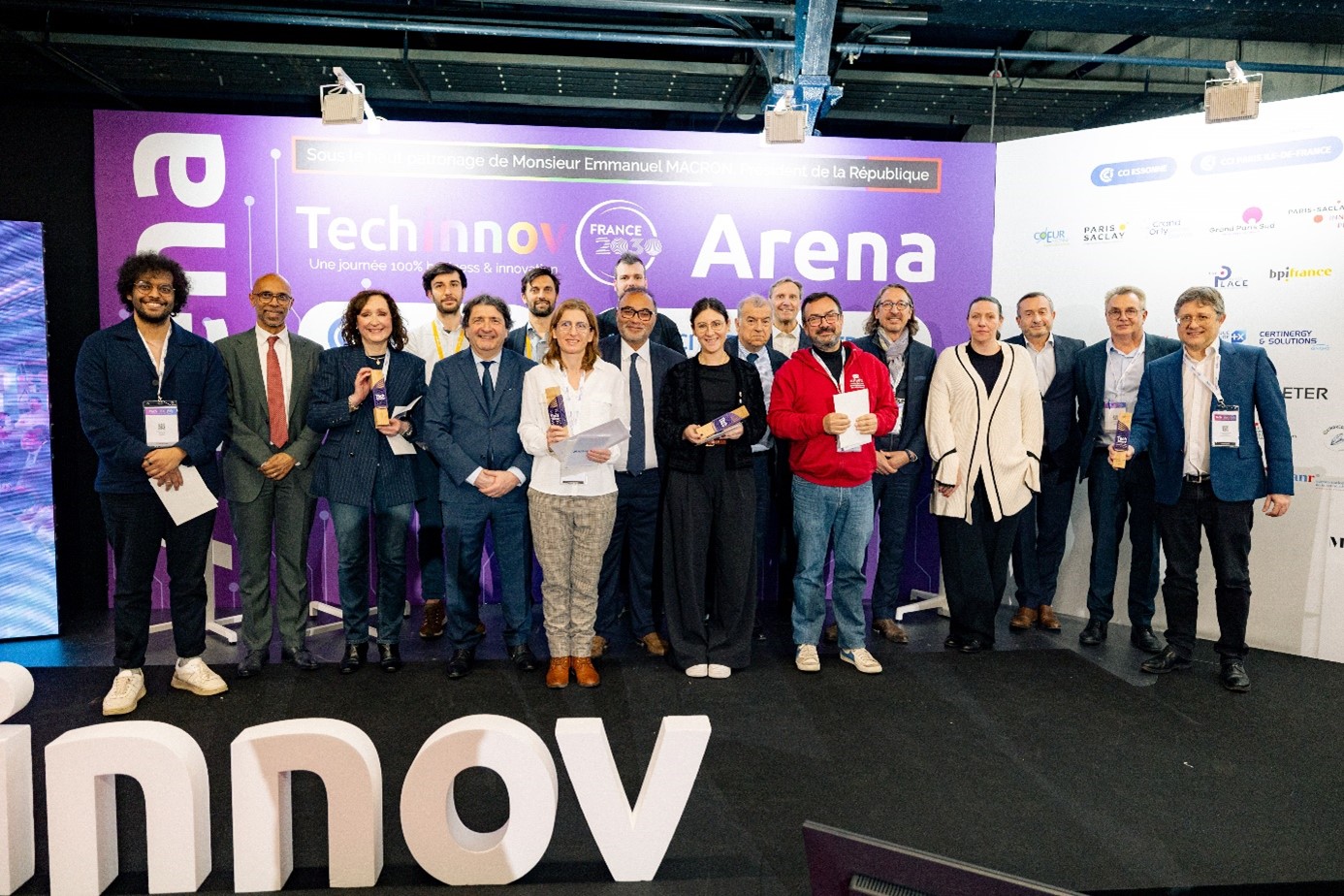
We would like to warmly thank all our partners, customers and employees for their trust and support. It is thanks to them that we were able to take up this challenge and win this great reward.
Newsletter
sign up for updates
We’ll never share your email address with anyone.
And you can opt out at any time. We promise.
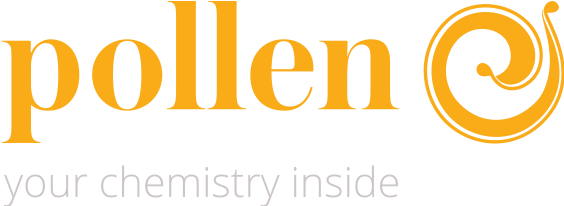
© 2025 Pollen AM inc. All rights Reserved.