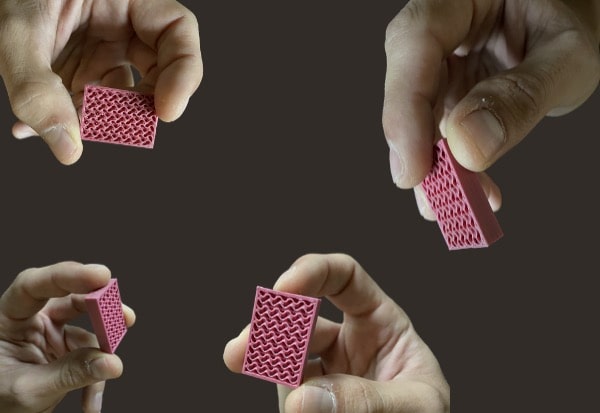
a turnkey solution!
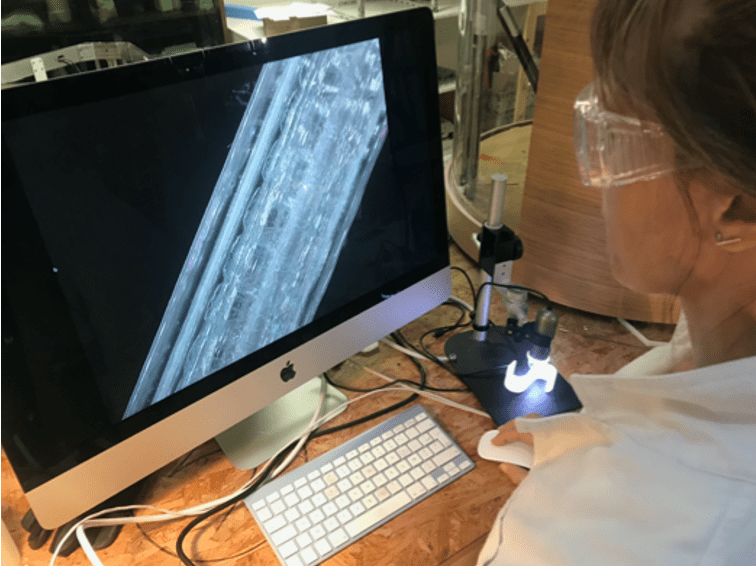
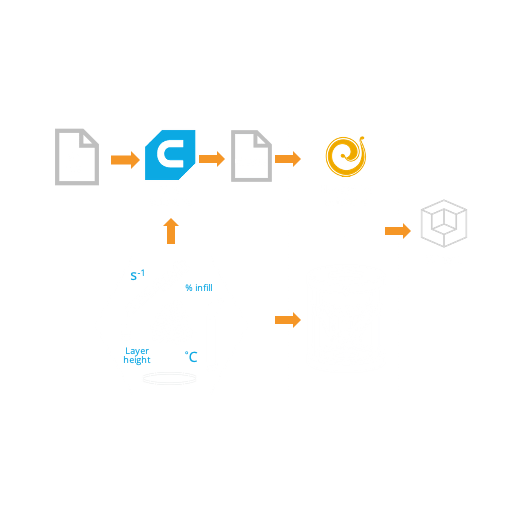
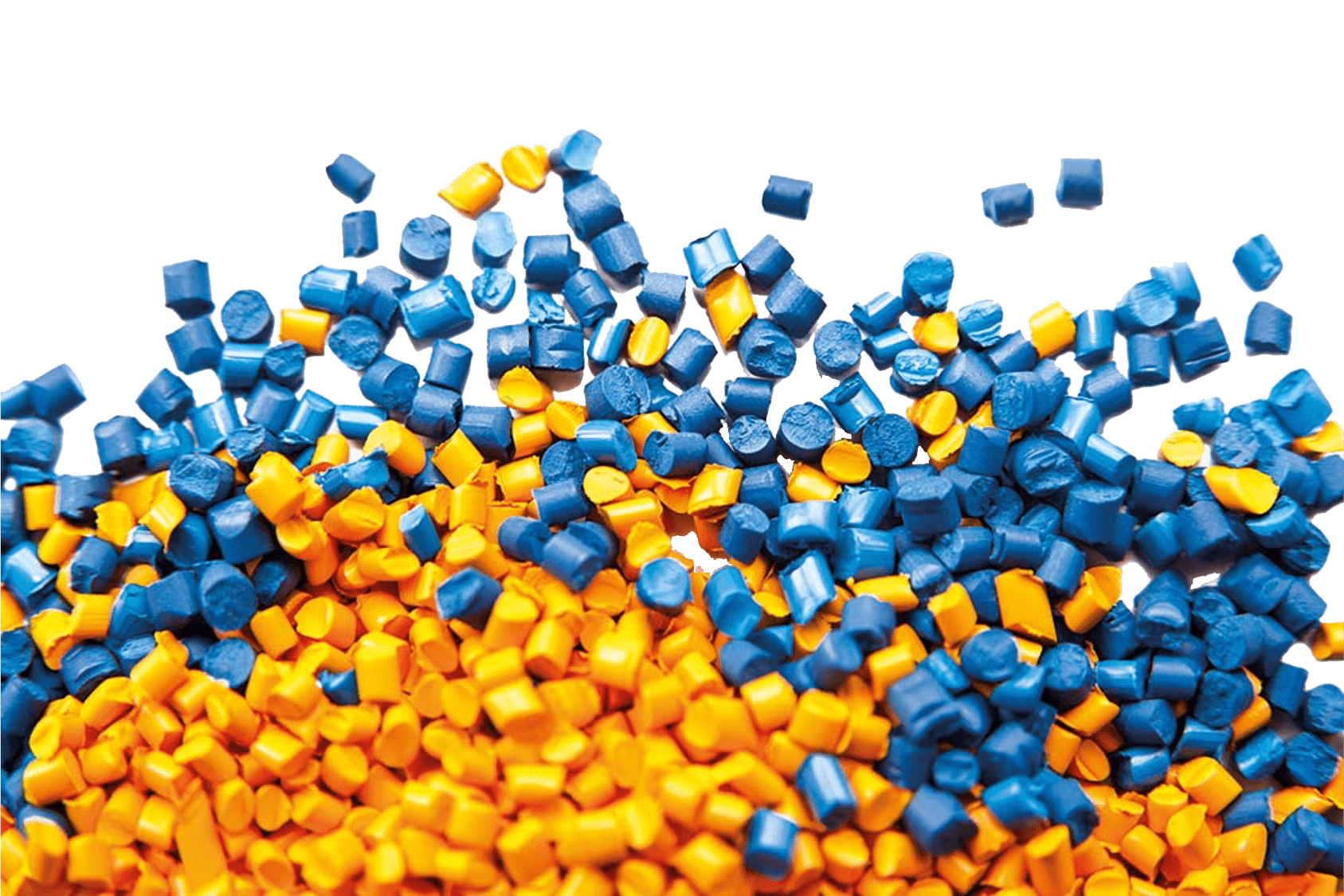
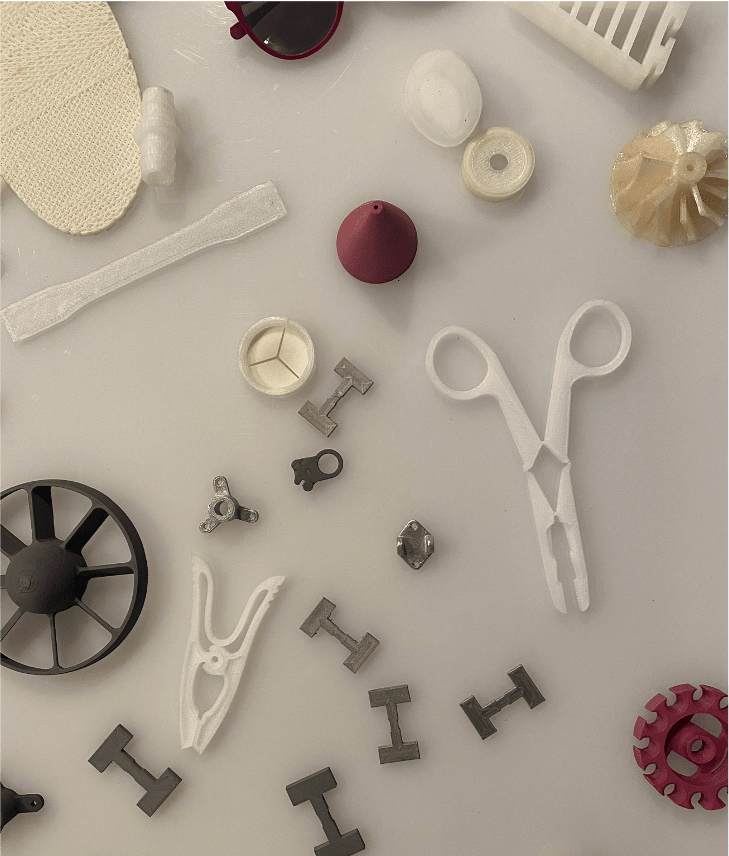
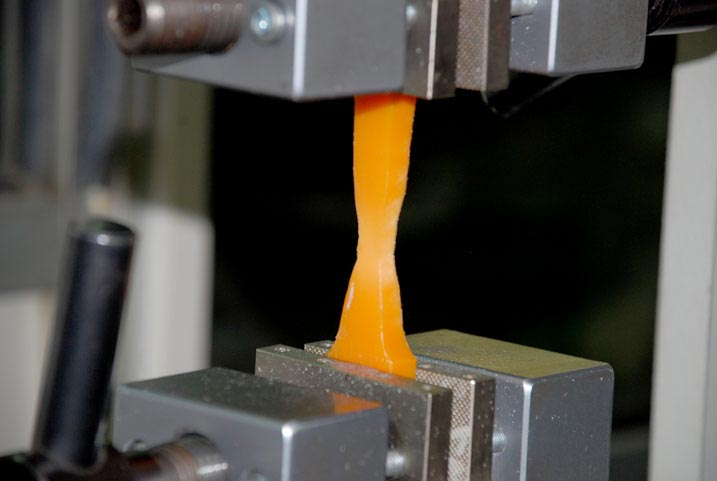
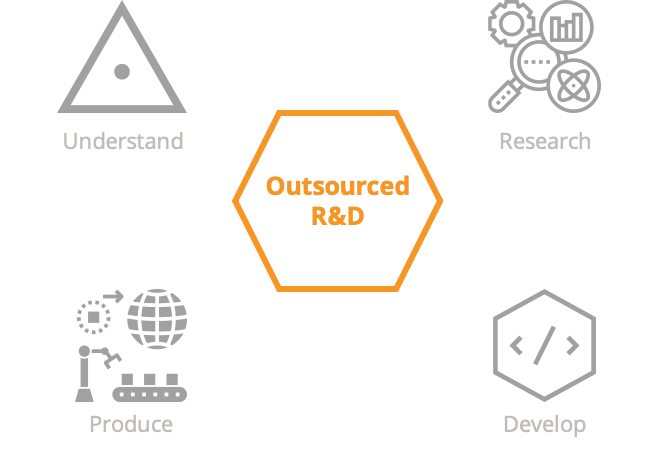
Let’s dive into the possibilities offered by PAM
From pellets to object, PAM technology offers the most direct process to high performances end-parts.
Metals Ceramics Commodity Elastomers Performance High Performance.
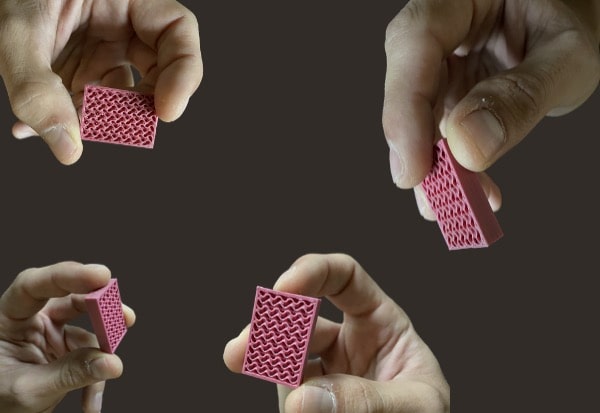
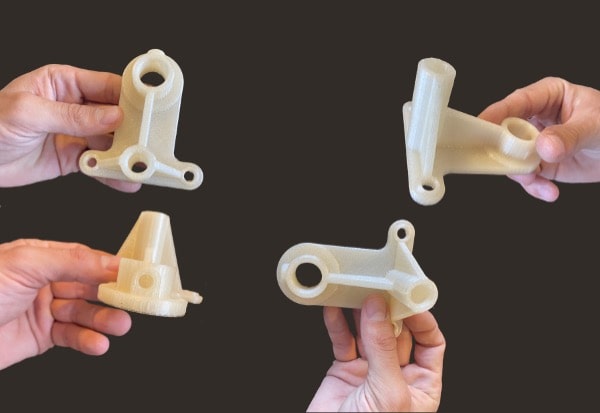
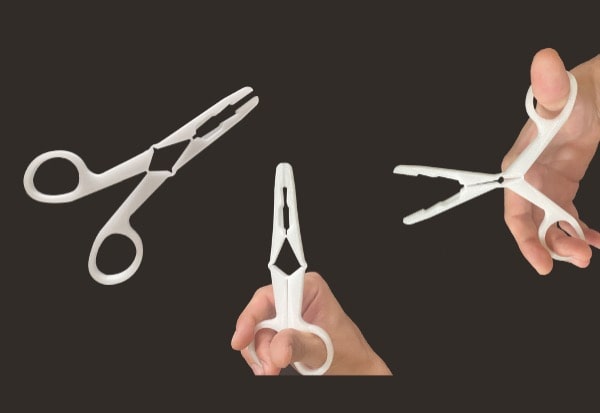
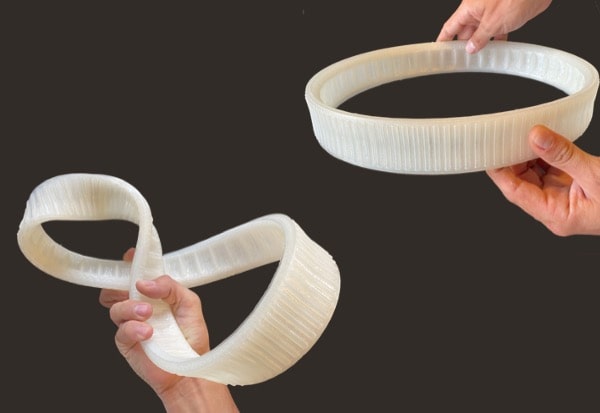
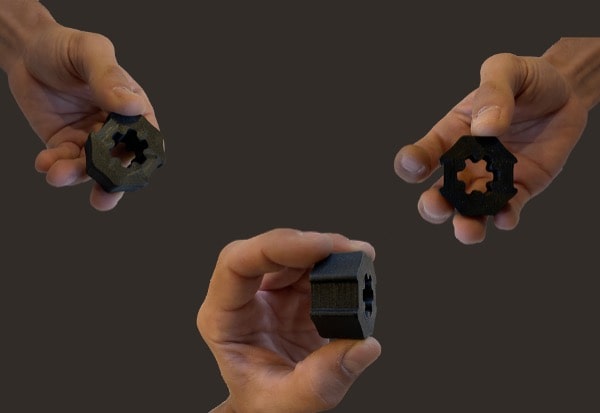
From pellets to object, PAM technology offers the most direct process to high performances end-parts.
Metals Ceramics Commodity Elastomers Performance High Performance.
We’ll never share your email address with anyone.
And you can opt out at any time. We promise.
© 2025 Pollen AM inc. All rights Reserved.