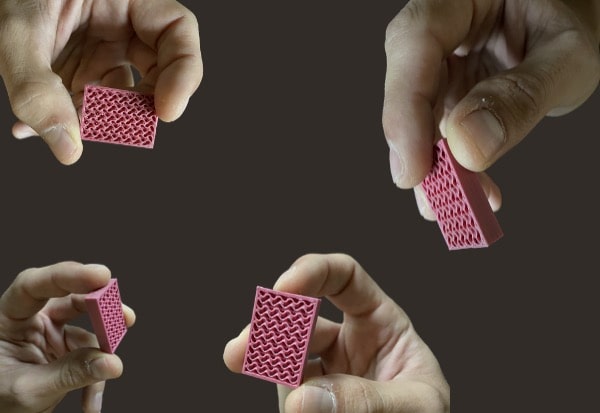
Medium batch - Focus on KPIs - TPE Ultra Soft
Industrial level of capability and centring.
The Pam technology is the first 3D printing technology able to transform very low hardness materials. An octopus production was made internally on a New Pam Series P to demonstrate its capacities.
This study is based on the comparative analysis of a reproduction of a part for a spare parts application.
The objective was to compare the different cost structures of two production methods: 3D printing with a Pam system vs. injection molding (requiring mold rework).
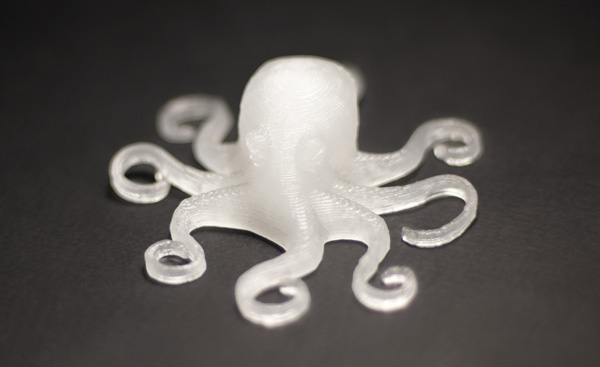
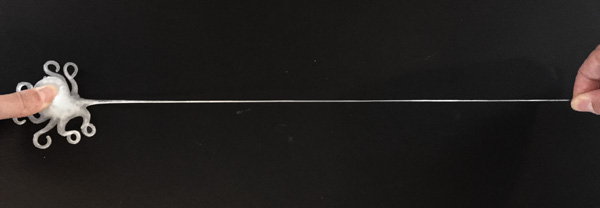
Material
- TPE familly: TPE-S;
- Material supplier: Kraiburg TPE;
- Material reference: TFOSTL;
- Material hardness: 51VLRH (30 shore00)
Printing parameters
- Number of extruder: 1;
- 0.8 mm nozzle;
- 0.4 mm layer height;
- 25 minutes for 1 part.
Production parameters
- Number of parts per 3D printing cycle: 5 parts;
- Transition between two productions: 1 minute (part removal and new printing cycle launch).
Production KPI
New Pam Series P is working 12 hours a day including 4 cycles per day and 1 cycle per night with no printing failure.
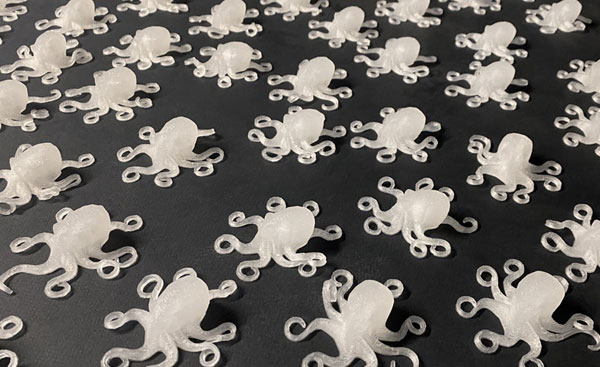
- Availability rate = 94%;
- Performance rate = 99%;
- Quality = 100%.
We observe an OEE (Overall Equipment Effectiveness) of 93% which demonstrates the reliability and robustness of Pam technology with a good machine setup.
Production capabilities
To evaluate our capability we focus on part weight. Indeed with such soft material contact measurements are not efficient.
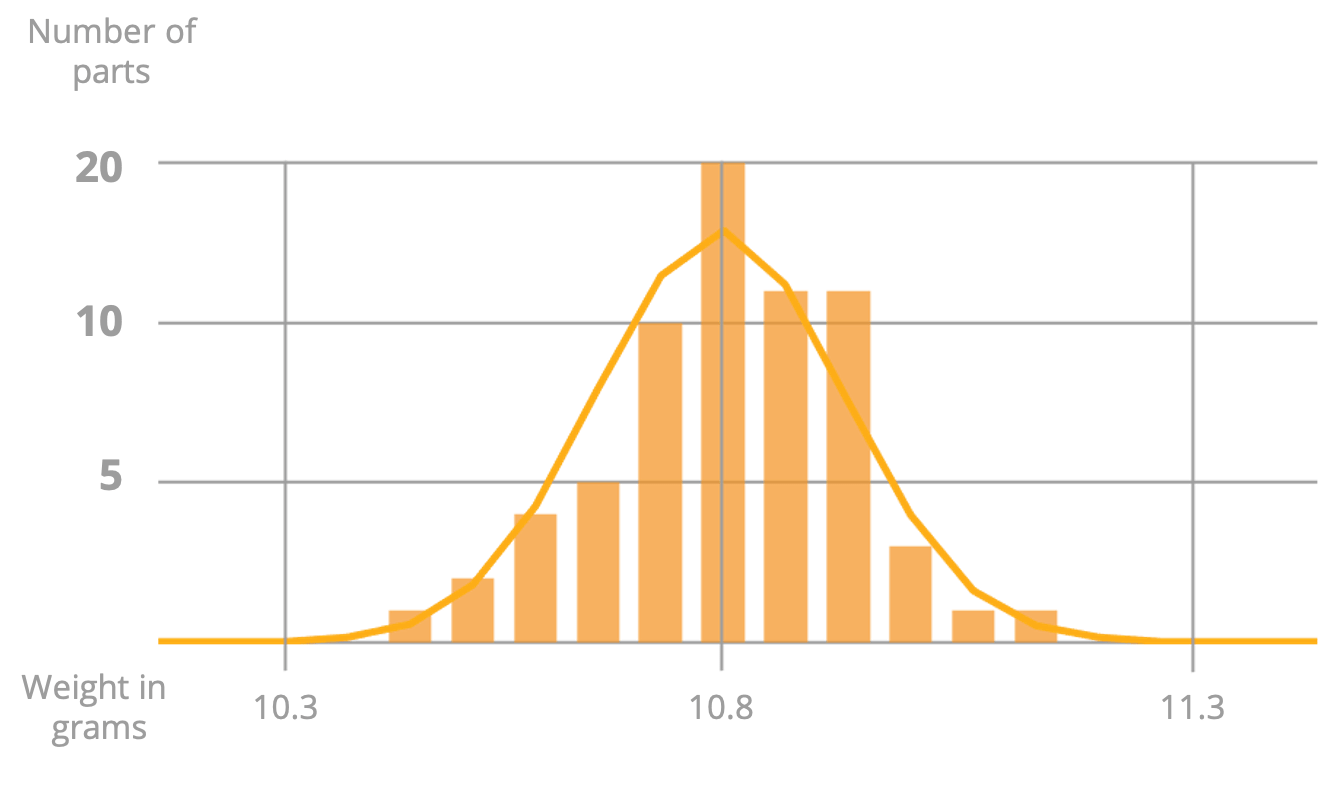
The input model used gives a weight of 10,8g per part. We are considering a tolerance of ± 5% so a part is acceptable between 10,3 to 11,3.
- Cp = 1,42;
- Cpk = 1,34.
Pam 3D printers demonstrate industrial level of capability and centring.
Let’s dive into the possibilities offered by PAM
From pellets to object, PAM technology offers the most direct process to high performances end-parts.
Metals Ceramics Commodity Elastomers Performance High Performance.
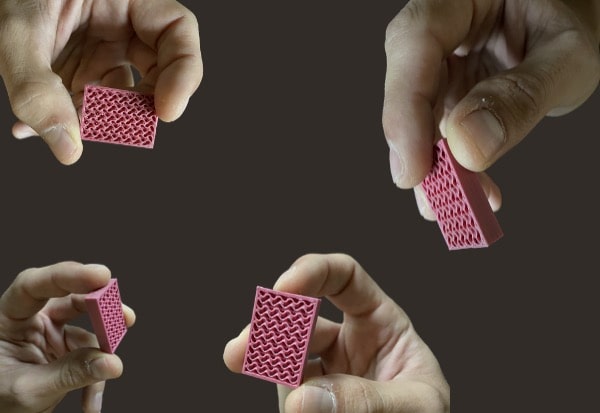
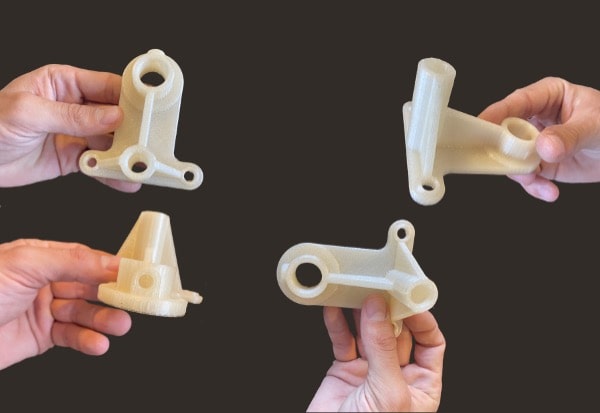
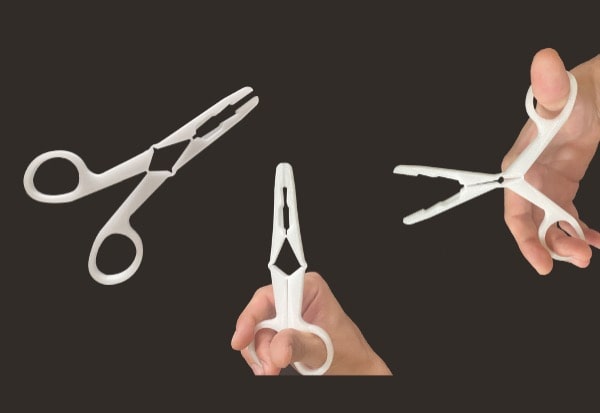
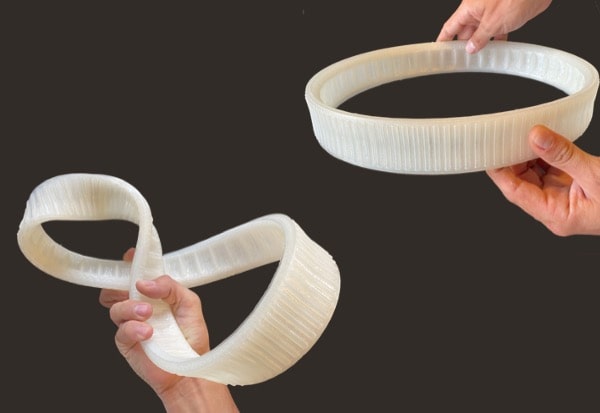
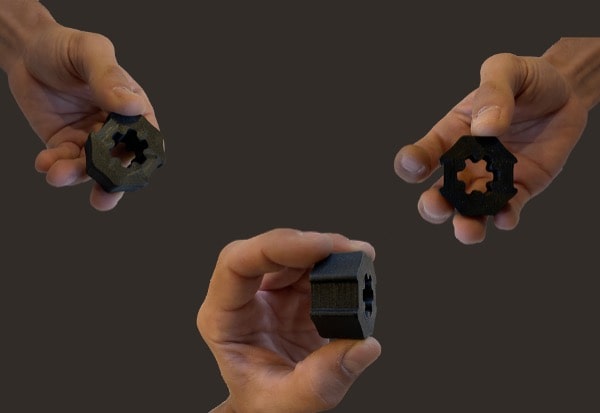