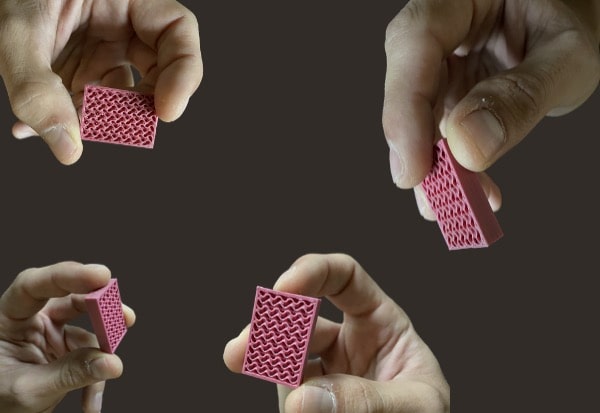
Right material prototyping with Decathlon
Quickly validate innovations, no matter their complexity.
“Right material” prototypes: functional prototypes close to the real material of the final product, allowing users to validate the characteristics and functionalities of the final product.
With pellet 3D printing processes, the material undergoes fewer transformations than a filament, for example, and therefore has characteristics more similar to those of injection molding. This is one of the reasons why Decathlon chose PAM technology: the goal was to print prototypes with the material used in large-scale production to obtain properties that were as close as possible to the final part.
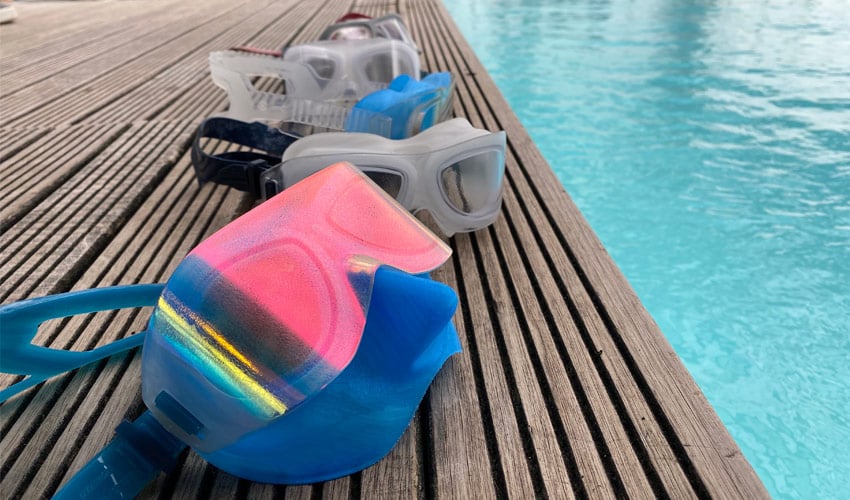
Jimmy Gantier is the Right Material Prototyping Manager of the AddLab at Decathlon. He is in charge of the prints made on Pam 3D printers.
His job is to manage the material and the way of printing. The design or engineering team provides him with a 3D file and the material that will be used in large-scale productions. He will then characterize the material to print it on Pam. This allows him to design prototypes that will be used for use tests or in the laboratory to directly study the behavior of the part with the right material.
For certain product categories, this approach allows to modify the product more quickly, without going through molding steps that are time-consuming, expensive and represent a certain energy cost.
Today, Decathlon uses PAM Series P machines to 3D print a lot of prototypes using TPE, TPU or SEBS, especially for water sports such as diving masks or different types of soles. The quantity of prototypes designed varies according to their size, but one thing is certain: the rate is controlled.
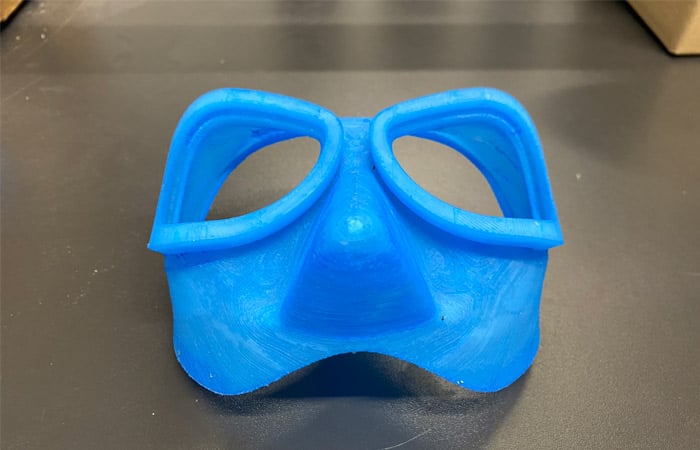
Thomas is a product engineer at SUBEA, Decathlon’s underwater sports brand. He has been using Pollen AM’s technology to produce parts for this kind of underwater applications.
One of the biggest difficulties in the design of a mask is to ensure the waterproofness of the product on the greatest number of different faces. To do so, a first 3D model is made, often inspired by existing face contacts, which will then have to be testes before opening the industrial mold (10 weeks / several tens of thousands of euros).
In recent years, Decathlon used a prototype mold (8 weeks / nearly 10K euros) for the first iterations, which were long and costly, and then opened an industrial mold that was systematically reworked. Digital simulation has enabled them to greatly reduce the number of iterations on prototype molds, but not yet to do without them.
Using right material prototyping with Pam, they intend to go from the digital model to the industrial mold without intermediate mold, thus saving up to 3 months and 20,000€, not to mention the CO2 impact of a mold made in Asia and dozens of parts sent by plane.
For now, Decathlon was able to validate the prototype’s waterproofness by using this process for a first concept. The next step will be to validate the correlation between this printed model and a very close model injected on prototype mold.
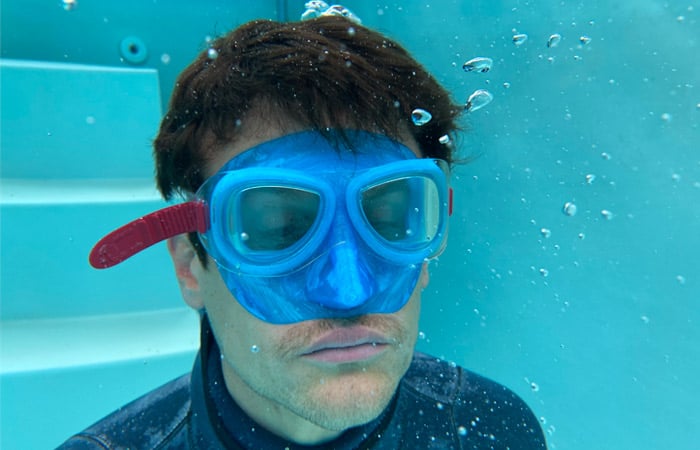
Pam 3D printers allow to use a wide variety of elastomers with a very low Shore hardness and therefore a better flexibility. This specificity allows Decathlon to design prototypes with different Shore 00, SHORE A and/or SHORE D hardnesses, thus expanding its range of soft materials to the maximum.
A lot of work has also been carried on the hooking plates and printing supports of each of the elastomers used. All materials have been characterized by Jimmy to associate them with the best possible soluble support, a good solution to imagine more and more complex designs but also to save time. The support dissolving in water, the post-processing does not require human labor and therefore no immobilization in human time.
Another consideration explaining the choise of Decathlon to use Pam systems is multi-extrusion. Indeed, Pam systems allow to associate up to 4 different materials in a same part. This ability is used for example during the manufacturing of ski poles. It is then possible to design a very hard shell and a rim with a rather flexible elastomer and soluble supports. In just a few hours, a prototype is born with multiple materials and very complex geometry.
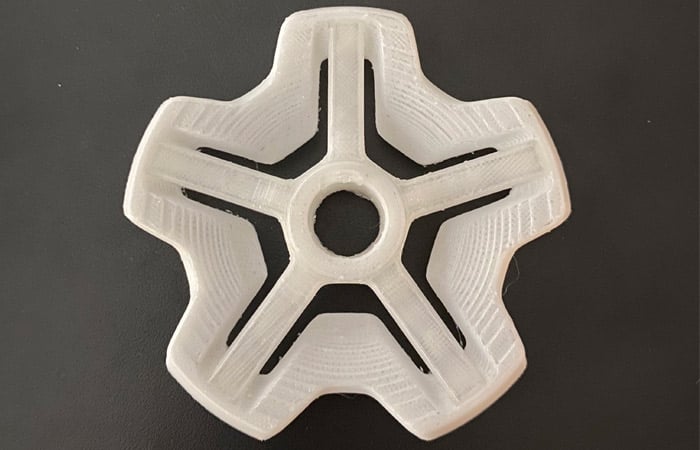
Thanks to additive manufacturing, and more particularly to materials compatible with PAM technology, because of the time and financial savings, Decathlon can easily imagine and test prototypes with virtuous materials to reduce the environmental impact of their product.
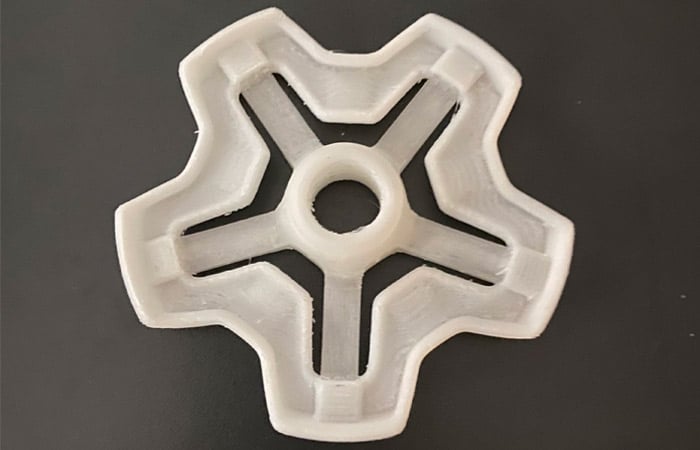
The future developments of the group around Pam concern mainly the materials. Decathlon will start a work on 100% biodegradable and bio-designed materials; testing granules based on vegetable waste will allow to understand if their behavior can be associated with a Decathlon product.
Let’s dive into the possibilities offered by PAM
From pellets to object, PAM technology offers the most direct process to high performances end-parts.
Metals Ceramics Commodity Elastomers Performance High Performance.
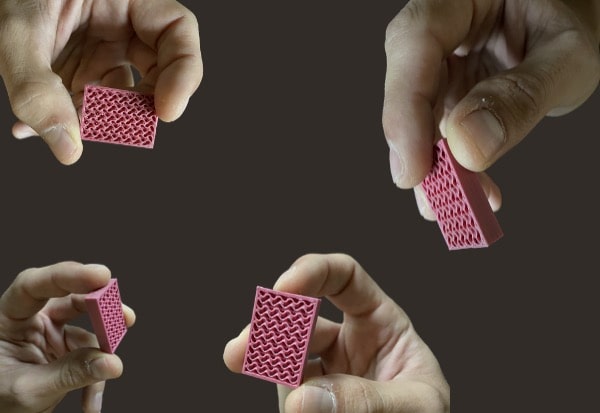
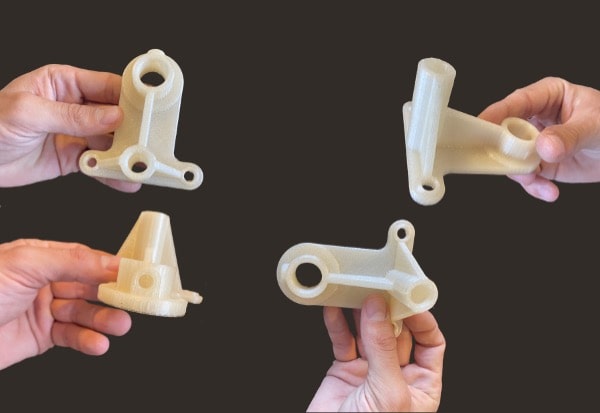
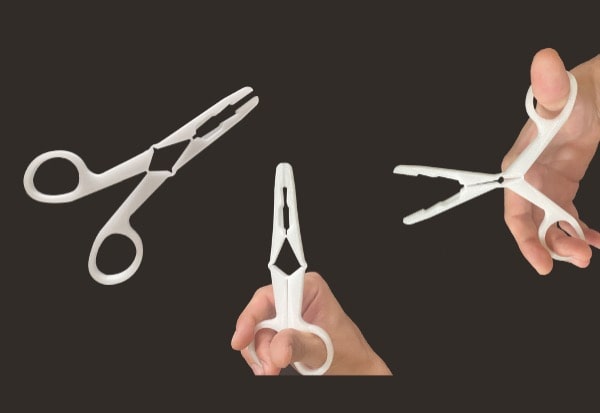
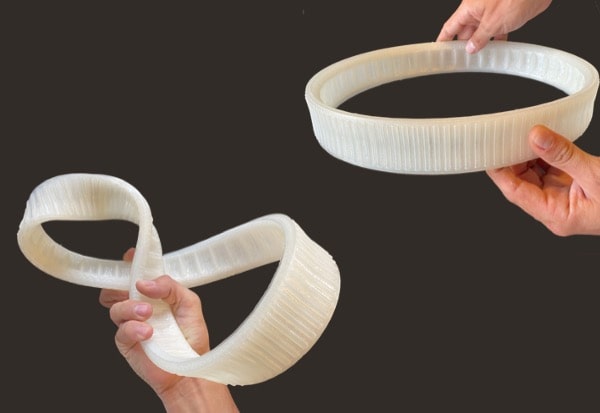
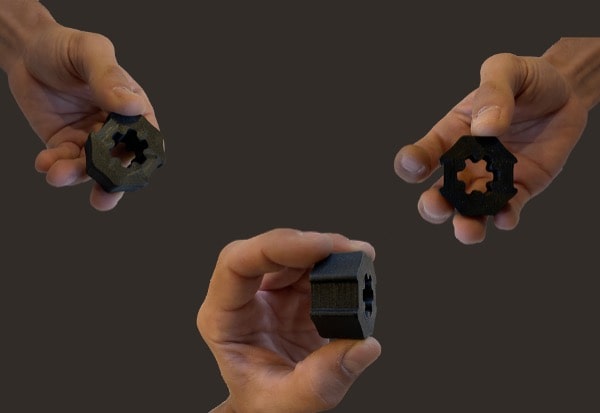