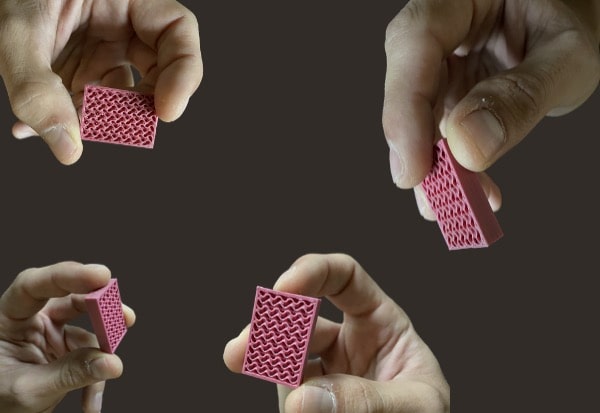
Using the support structure
with Pam 3D printers
We name by support the structures generated during printing to support the part and which will be removed at the end of printing.
The support is used to allow the printing of the overhanging surfaces of the part. If it allows the realization of the part, the support generates some disadvantages:
- its realization increases the printing time for material which will not be preserved in its final state;
- this leads to post-processing operations to remove the parts that served as support during printing.
For these reasons, it is more comfortable to be able to print a part without having to use a support.
The first solution is to design a part whose geometry does not involve the use of media. The main design rules are as follows:
- Overhang angle greater than 45° with respect to the printing buildplate;
- overhang length less than 10 mm.
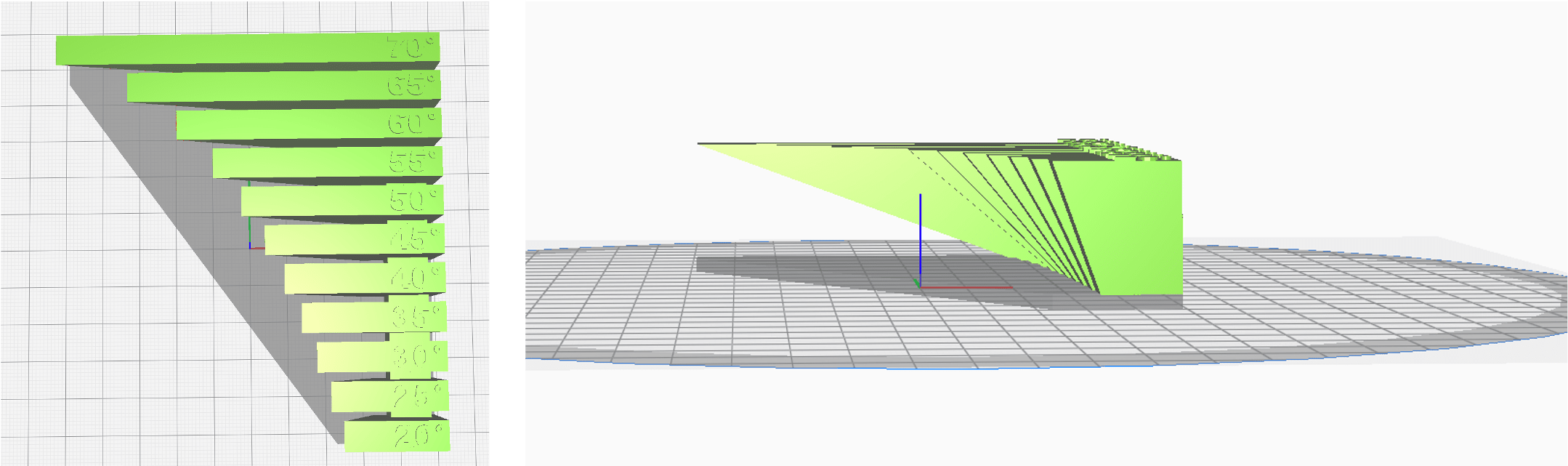
Part sample to test the overhang
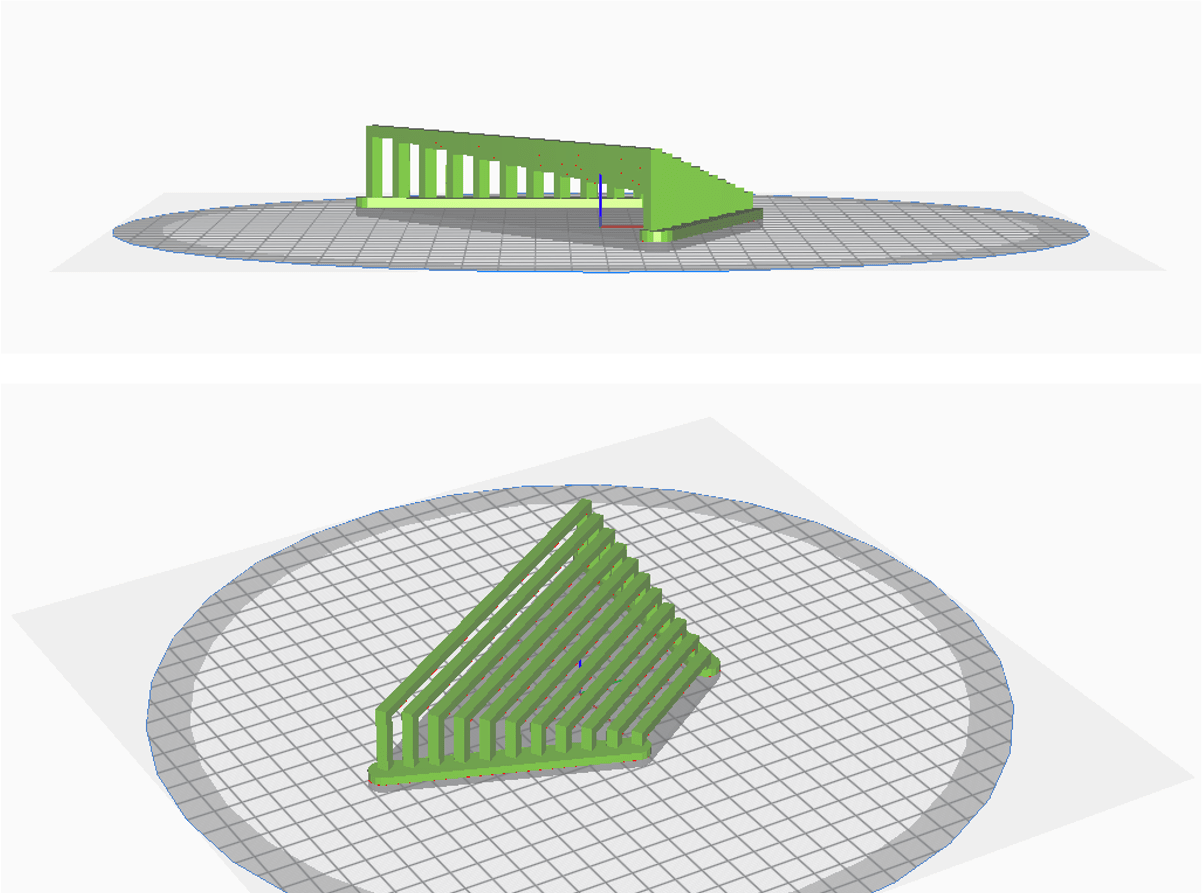
Part sample to test the bridging
If it is not possible to apply these rules then a first solution is to make the part in several parts which will then be assembled by a conventional technique.
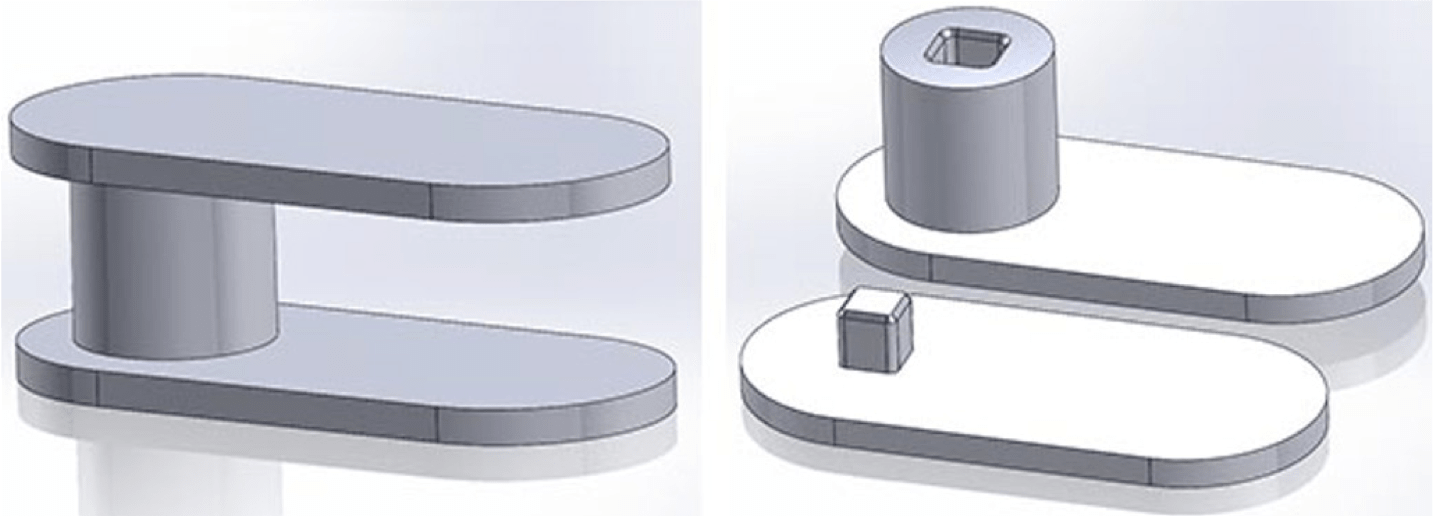
Since none of these solutions is possible, you will need to use media to print the part.
There are two media generation strategies:
- The media is of the same material as the printed part: The printing parameters of the media are then determined to facilitate mechanical removal, for example by incorporating a gap between the part and the media.
- Unfortunately, this solution is time-consuming and degrades the surface at the workpiece/substrate interfaces.
The substrate is in a solvent-soluble material:
This solution is by far the most comfortable. It allows to generate supports which will be dissolved later by dipping the part in a solvent.
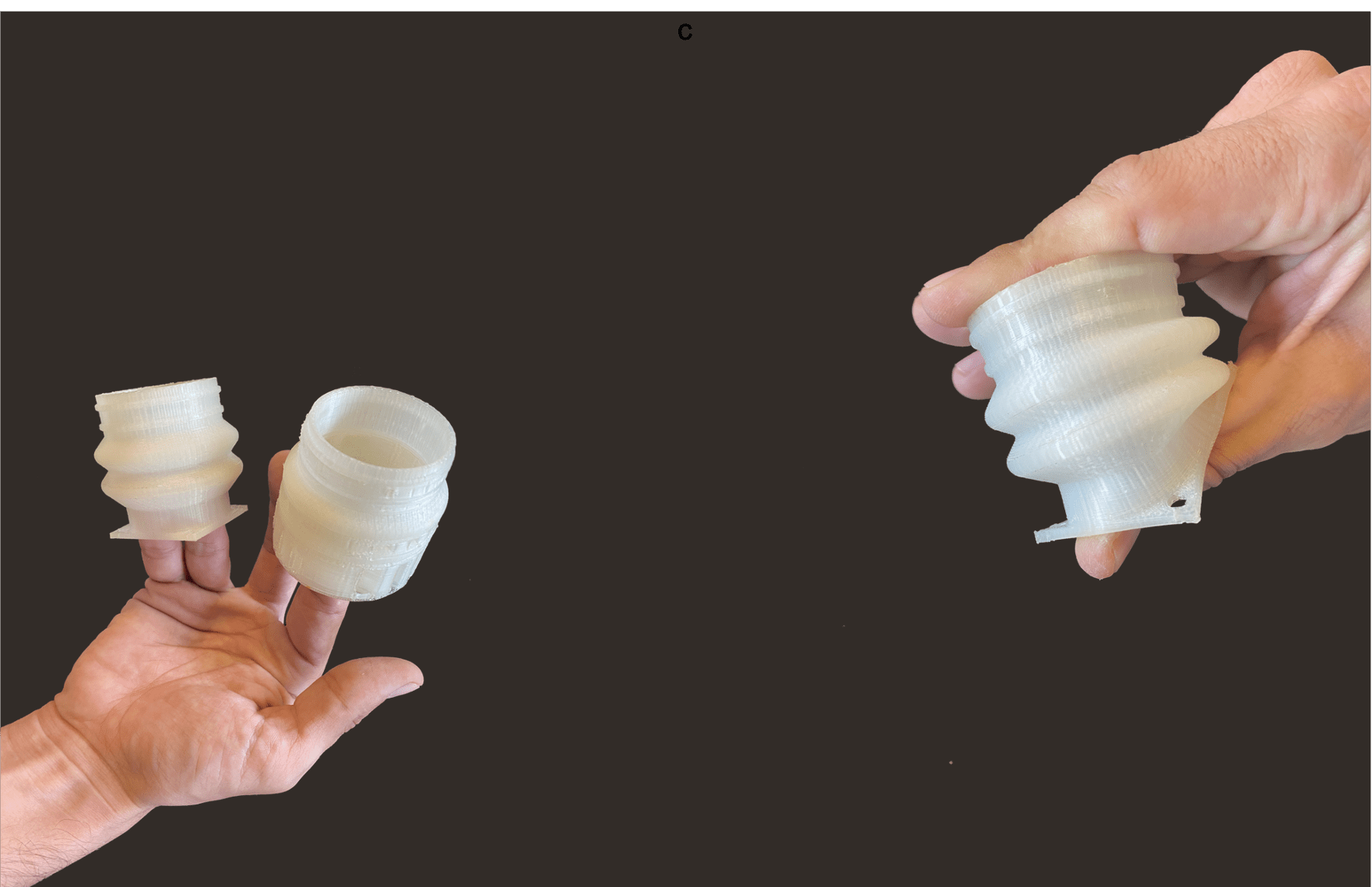
To implement this solution it is necessary to identify a compatible material that adheres to the printed material and is soluble in a solvent that does not impact the printed material.
As an example, PLA can be printed with PVA substrates that dissolve in water.
It therefore appears that the use of an open system using the material in its most common form has great advantages in the management of the substrate material. It becomes possible to identify the materials (or combinations of materials in the form of a mix) that are of interest as a carrier material in relation to the material to be processed, and then to develop a suitable printing profile.
Synthesis of the support structure management
Constraint and element | Proposed solutions |
Stage of the 3D printing chain | Good practices |
---|---|---|---|
No support structure needed - Recommanded |
Avoid cantilevered surfaces at an angle of less than 45° to the tabletop. | Modeling | |
Avoid overhangs exceeding 10 mm in length | Modeling | Support overhangs with chamfers that respect the printing angle without support | |
Separate the part into several parts to be assembled | Modeling | Integrate in the various parts of the forms facilitating the assembly (male female geometry) | |
Support structure needed | Use the same material as the one 3D printed with an adapted print profile | Slicing | |
Use a carrier material that is compatible with the 3D printed material and soluble in a solvent | Slicing | 3D print with an open system to select or formulate a compatible material |
Let’s dive into the possibilities offered by PAM
From pellets to object, PAM technology offers the most direct process to high performances end-parts.
Metals Ceramics Commodity Elastomers Performance High Performance.
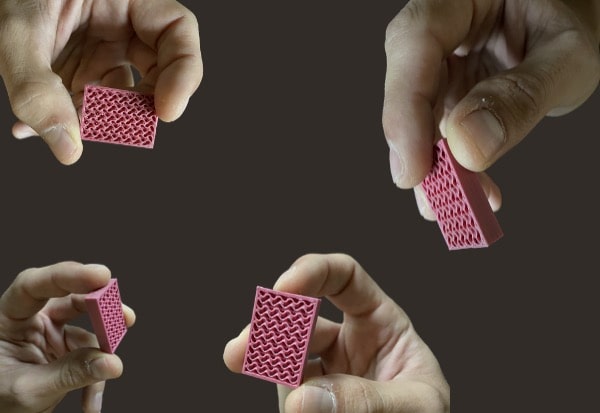
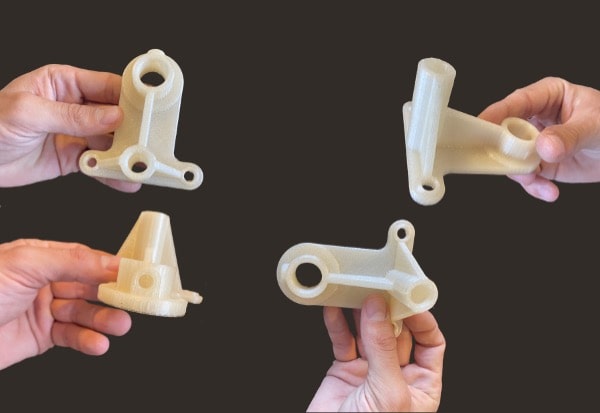
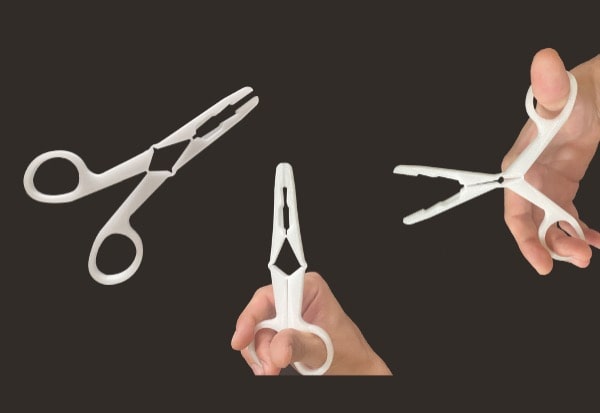
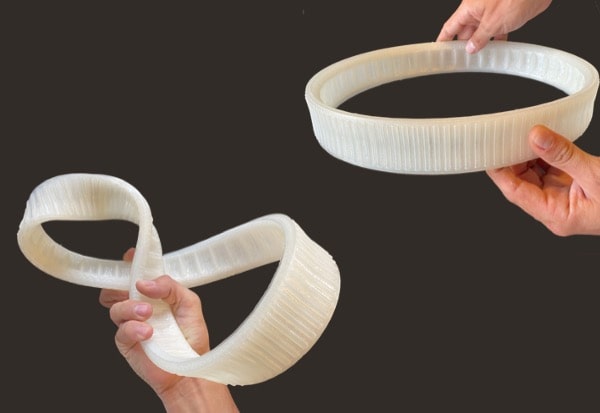
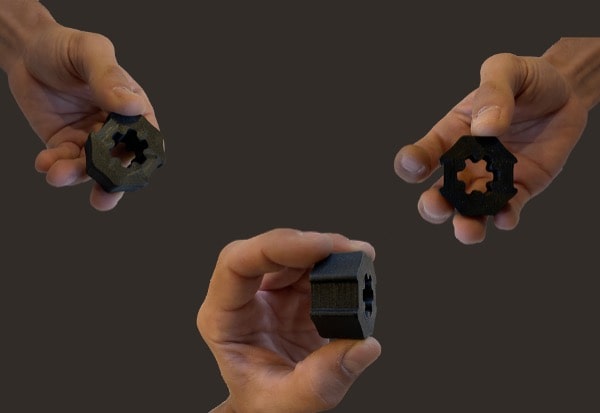