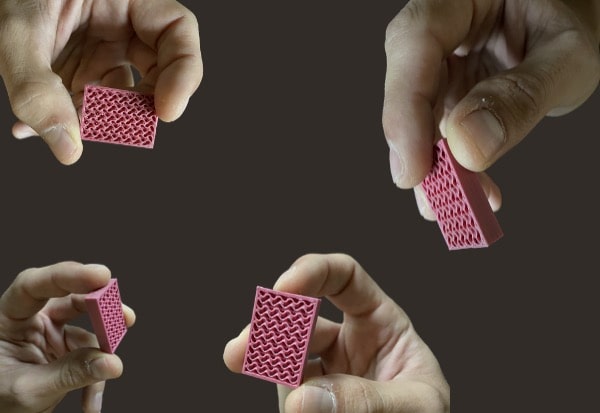
Bio-Based Polymers
Opportunity
The use of bio-feedstock in the polymer sector is of great interest. Starch, cellulose, but also alkyd resins and some polyamides have been obtained from natural resources on an industrial scale.
The industry demonstrated a great ability to process large amounts of biomass. Nevertheless, it is difficult to estimate the amount of such biomass that is necessary to replace petrochemical polymers by bio-based ones and whether this substitution would lower the environmental footprint.
From a technological point of view, the progress in the plants processes have been spectacular. Some plants still have a rather small capacity, but others are comparable to typical petrochemical plants.
With the continuous growing demand for bio-based plastics, plants with a bigger capacity production will be even more commercially available.
From a geographic point of view, the United States and Europe are the most important areas for bio-based plastic production, followed by the Asia Pacific region and South America.
Those polymers are produced from a bio-based diol, while diacid or diester could be either bio-based (like succinic or adipic acid) or petrochemical-based (like PTA and/or di-methyl terephthalate, DMT).
Among them, PET is the largest used polyester, with physical and mechanical properties that make it suitable to be used for fibers (65%) and packaging (35%) applications.
This last application regards bottles (76%), containers (11%) and films (13%). It plays an important role in the plastic market, but due to its poor sustainability due to a much slower degradability, it poses serious environmental issues, especially for waste treatment, when it is used for short time applications, as for example when it is employed as food packaging.
In order to realize a sustainable plastic, both starting chemicals such as ethylene glycol (EG) and PTA and/or DMT monomers have to be obtained from biological sources.
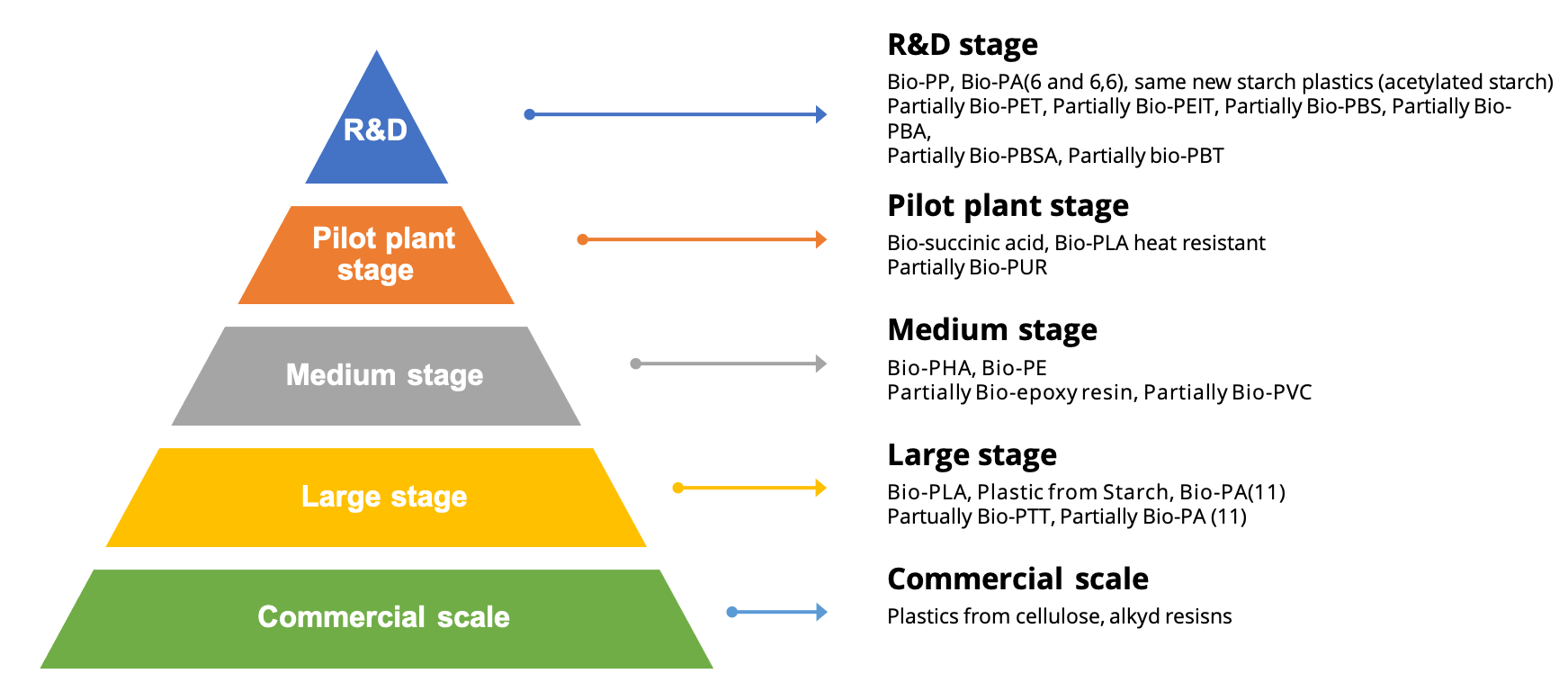
Bio-based polymers development stages
The largest number of bio-based plastics are in the R&D and pilot plant stage, while only few materials are in large and commercial stages.
In the first case, different kinds of technological challenges are only possible.
For the production of partial Bio-PBS, no technological barriers are present, because the production of succinic acid is technically ready. The esterification of succinic acid with butanol to obtain PBS is performed at a large scale but via petrochemical precursors. With respect to PBS, the production of partial Bio-PET is even more easy.
Meanwhile, the production of Bio-PP requires several steps that present limited knowledge, making the scale-up even more diffcult and more demanding. Thus, depending on the type of plastics, between 20% and 100% of the actual volume could be replaced by bio-based alternatives, but not in the short/medium term due to economic problems related to cost production and capital availability, technical scale-up, the great amounts of bio-based feedstocks and the industrial conversion to the new plastics.
Another important factor to take into consideration in the production of bio-based materials is the competition with food, feed and bio-fuels for the supply of raw materials.
Today, starch and sugar crops are the sole feedstocks supply, but a second generation of bio-ethanol, based on lignocellulosic feedstocks, can be used as future starting chemicals in the production of bio-PE, as well as for other biopolymers.
Lignocellulose is cheap, abundant and not competitive with food with respect to starh and sugar crops, but the biotechnology to transform cellulose into sugar monomers, via microorganisms, requires processing steps that are more complicated. For the next two decades, the biomass dend for bio-based plastics production will remain smaller than that demanded for human food and animal feed.
The major influencing factors for the development of bio-based plastics are the technological barriers that must be overcome in order to reach a large-scale production, the suitability of these materials to be used as bulk materials, their competitiveness in terms of cost with respect to petroleum-derived ones and the availability of raw materials for their synthesis.
The production using sugar beet and maize grain was closest to the current fossil technology, the production with sweet corn was found to be the most impactful, while the production using orange peels was the greenest one.
The potentiality of these bio-based polymers to be used in bulk applications is not a problem, thanks to the fact that they are chemically identical with their petrochemical counterparts.
Within the bio-based plastics sector, PLA, bio-PE, starch plastics and bio-based epoxy resins are the four key materials.
PLA and starch plastics are candidates for fast growth thanks to their production cost reduction and bulk application.
The key factor for the growth of Bio-PE is related to its production costs.
Bio-PP is still in its lab/pilot-plant stage due to technological barriers that include conversion technologies and downstream processing technology. When considering an optimistic future scenario.
Let’s dive into the possibilities offered by PAM
From pellets to object, PAM technology offers the most direct process to high performances end-parts.
Metals Ceramics Commodity Elastomers Performance High Performance.
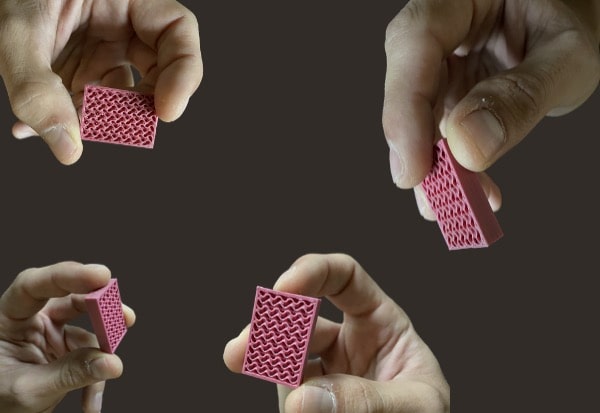
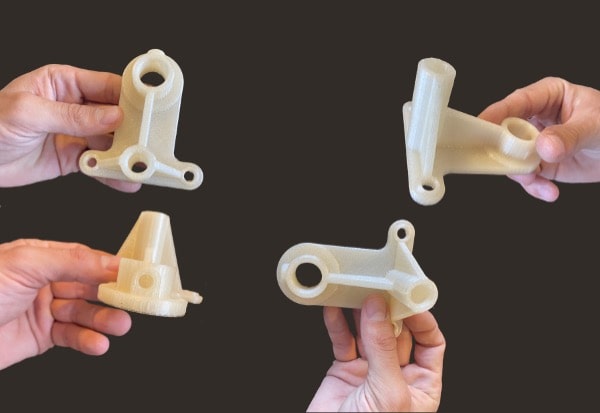
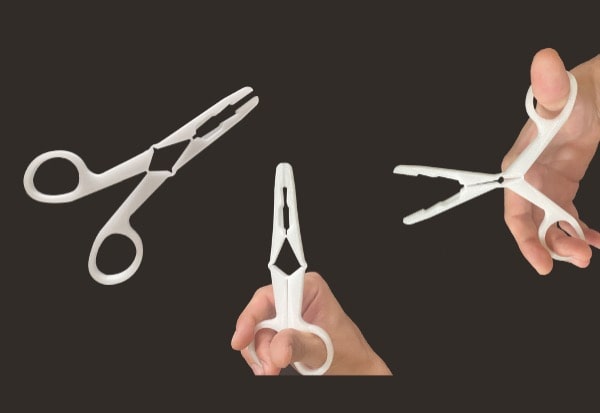
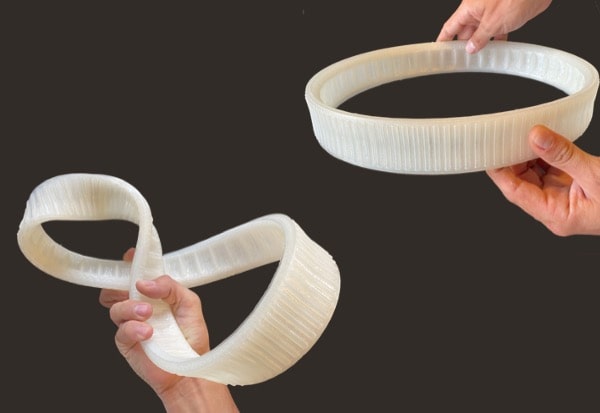
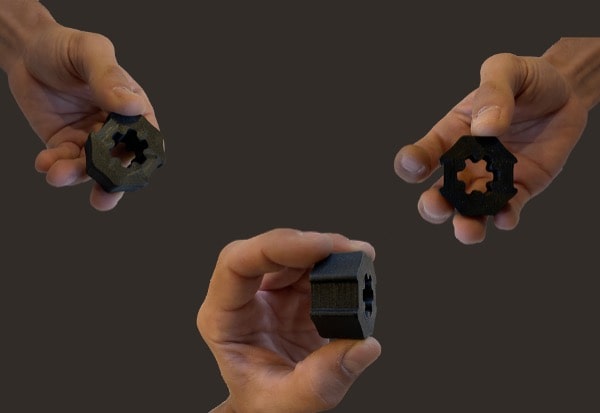