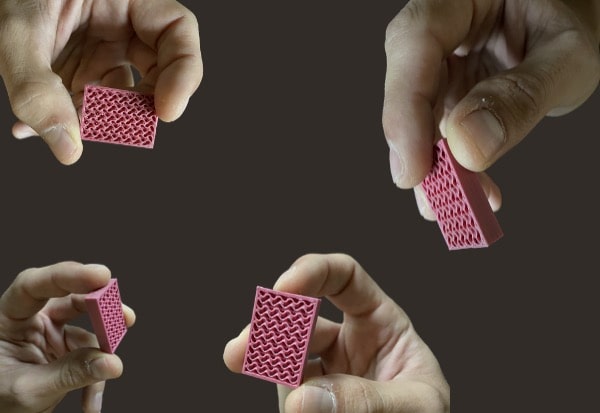
It's about 3D printing,
but with the right material.
- Material research
- Multi-extrusion research
- Prototypes & concept validation
- Material validation
- Functional testing
- On demand & local production
- Support to industrialization
- Tools, jigs & fixtures
- and so many more ...
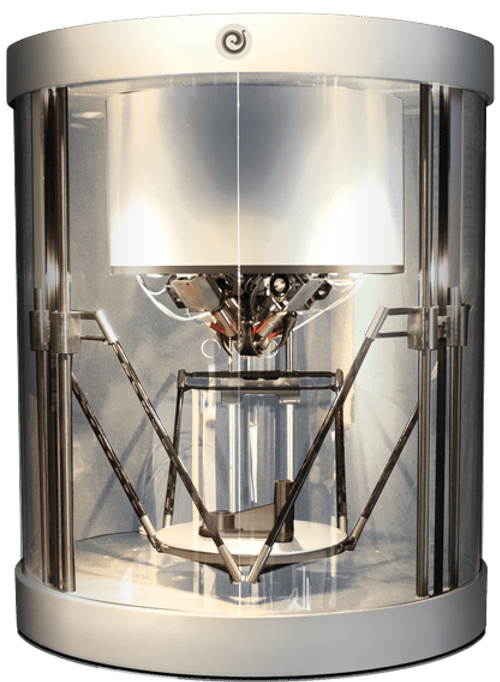
3D printer specifications
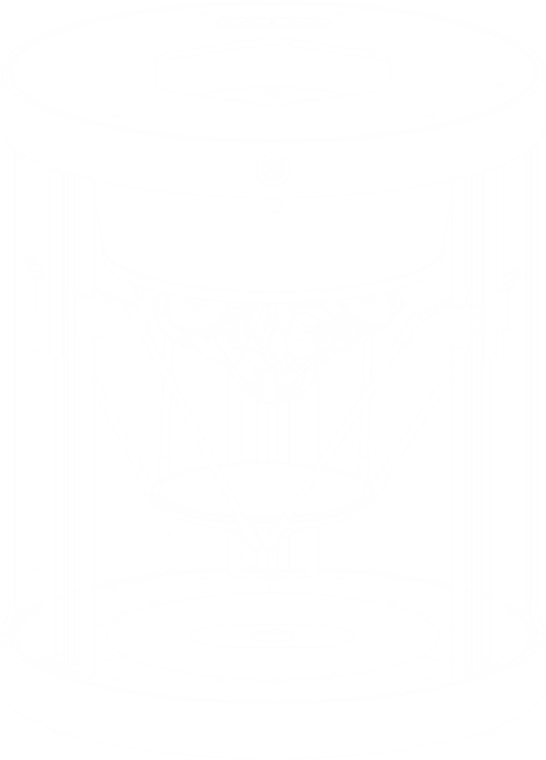
Physical Dimensions
Diameter | 834 mm |
Height | 925 mm |
Weight | 95 Kg |
Main specifications
3D printing process | PAM |
Number of extruder | 2 |
Compatible materials | Thermoplastic materials (Injection moulding grades) |
Maximum print volume | Ø 300 x H 300 mm |
Nozzles sizes | Ø 0.25 - 0.40 - 0.60 - 0.80 - 1.00 - 1.20 |
Stepper motor resolution | 40µm (Z) and 5µm (X,Y) |
Maximum extrusion temperature | 450°C |
Maximum print bed temperature | 150°C and 250°C in options |
Heating room | up to 70°C |
Radiant disc | up to 300°C |
Supplied Software | Honeyprint & Cura by Pollen AM |
New print head
Our print head is redesigned for better visual control precision and durability.
We also improved the cooling architecture.
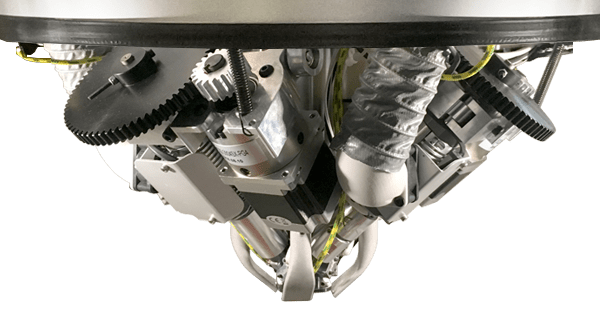
New holding mechanism
One screw opening mechanism for easy extruder removal.
Reinforced machined aluminium parts with ball bearings integration for more precision and durability.
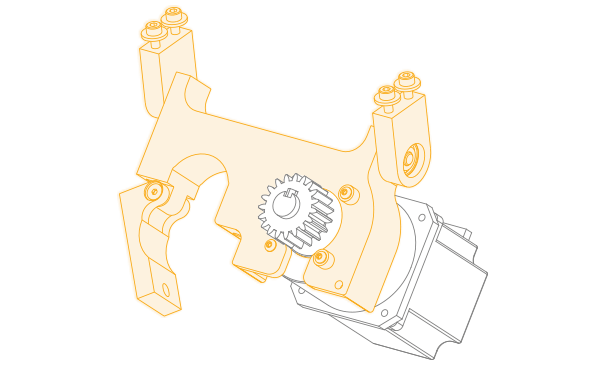
New lifting mechanism
All in-one stainless steel wire rope with eyelets and easy one screw removal for maintenance.
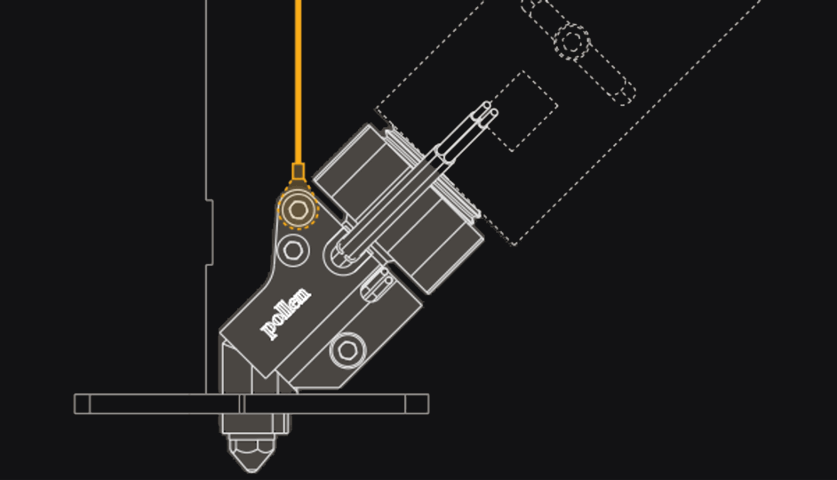
New material cartridge
Integrated cartridge opening mechanism for pellets refill on the fly. The hopper has an optimized base geometry for increased cooling performances and better pellets flow.

New build plate
Our build plate is redesigned for better maintenance durability
and dimensional accuracy.
New assembly configuration
Easy build plate replacement and micro-perforated options dedicated to materials with strong warping effect.

New carbon rods
Assembly jigs are redesigned for improved carbon rods dimensional accuracy resistance and repeatability.
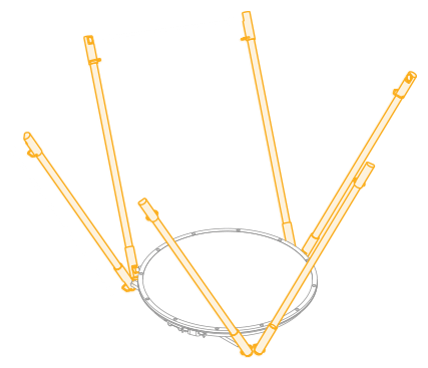
Enhance heating
Two additional equipments are present to perform good temperature homogeneity into the build chamber and to optimize inter layer adhesion.
Integrated heating radiant dics
Our interlayer heating device is designed to increase Z direction mechanical performances. It keeps a warm zone over the part and preserve good adhesion between each layer.
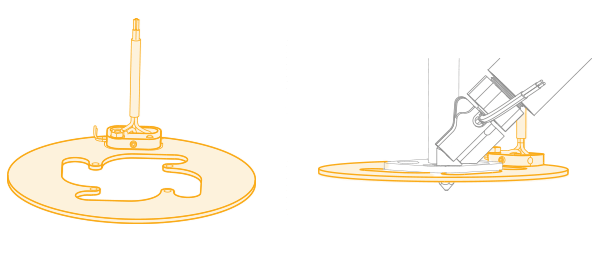
New heating room
Specially designed forced convection heating room devices: hot air is recycled from inside the build volume for increased thermal regularity.
Heating room temperature control is integrated in Honeyprint software for easy set-up. The maximum temperature is 70°C.
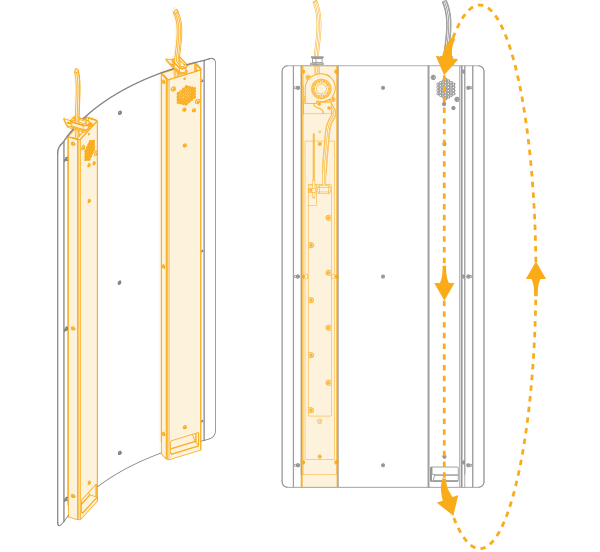
Optimized electronics and wiring
Each extruder is controlled by two electronic boards. One is dedicated to low-voltage heating elements and the second is dedicated to extra-low voltage such as motors, fans and temperature sensors.
Pam Series MC wiring is redesigned for increased robustness and 3D printing repeatability.
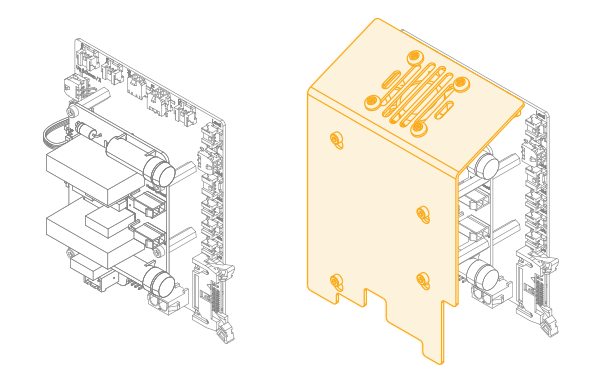
New metal skin
Pam Series MC has a brand new metallic and insulated casing. Our team has developed the original wooden casing with great insulation performances without additive heated build chamber.
In regards of improving thermal regulation and increasing maximum room temperature, we completely rethought our position towards new casing materials. Insulation plates are made out of glass wool and overlapping casing is in aluminium. This enables the best heating performances for the build volume and rapid rise in temperature.
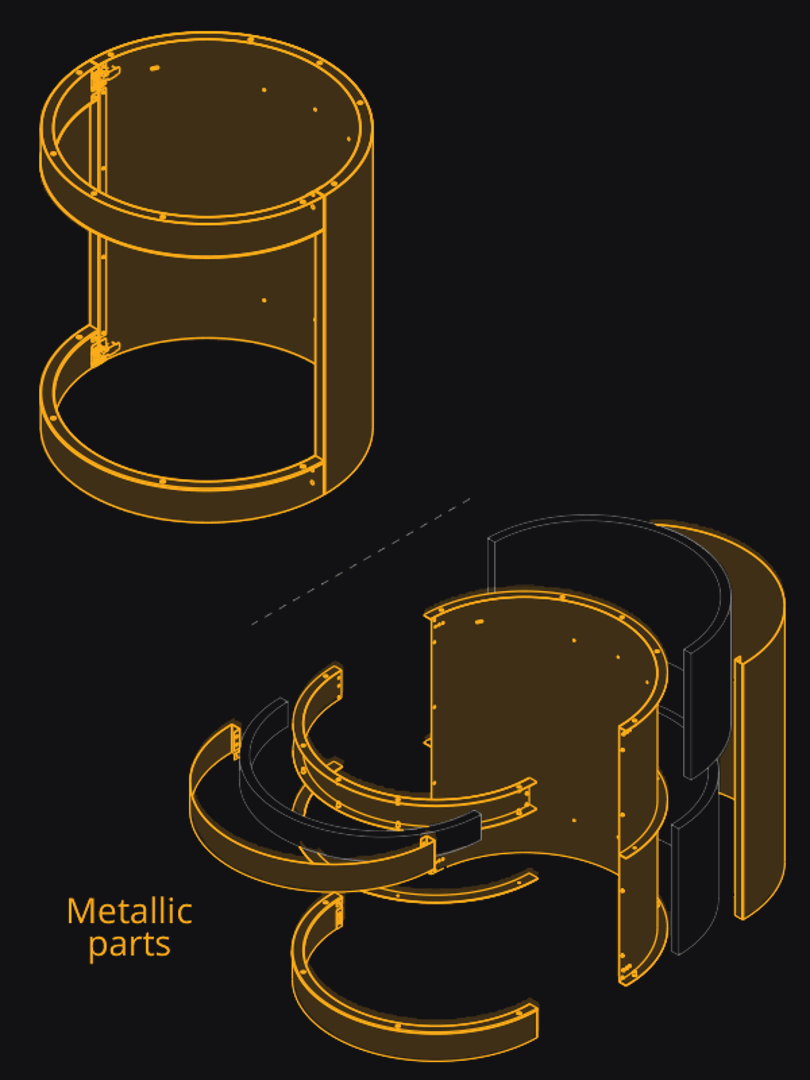
3D printing industrial thermoplastics,
is possible!
From standard to high performance materials.
Let’s dive into the possibilities offered by PAM
From pellets to object, PAM technology offers the most direct process to high performances end-parts.
Metals Ceramics Commodity Elastomers Performance High Performance.
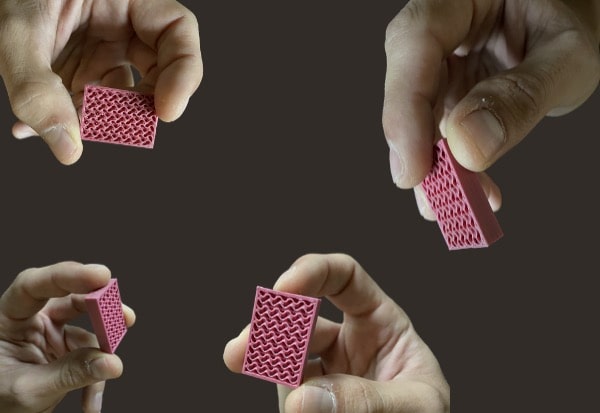
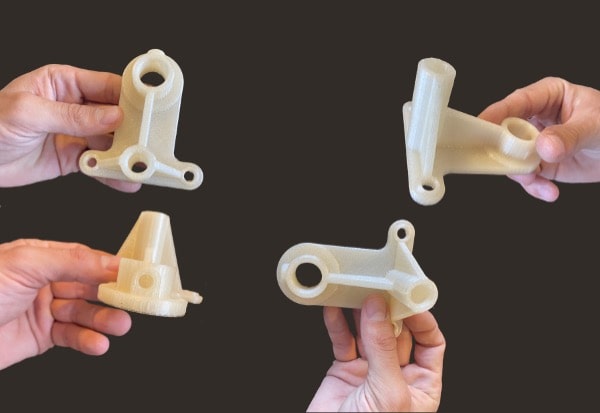
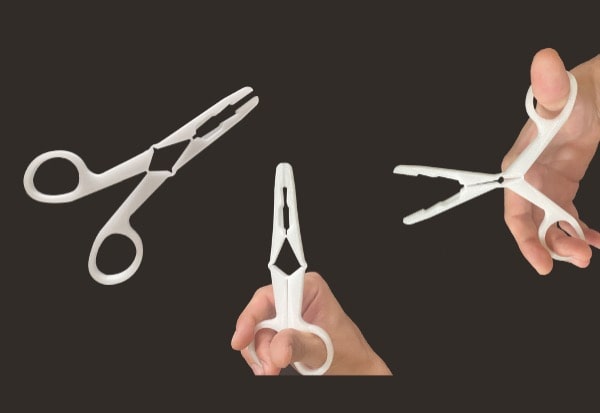
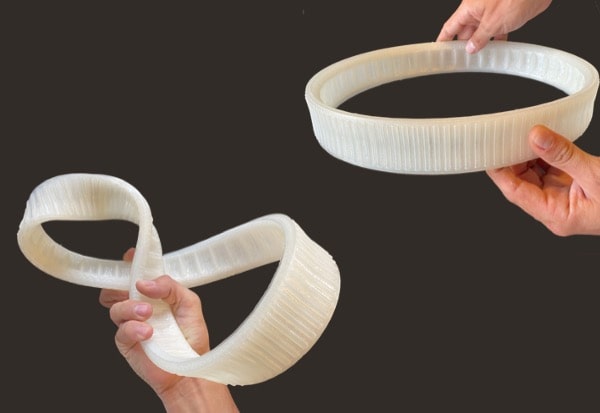
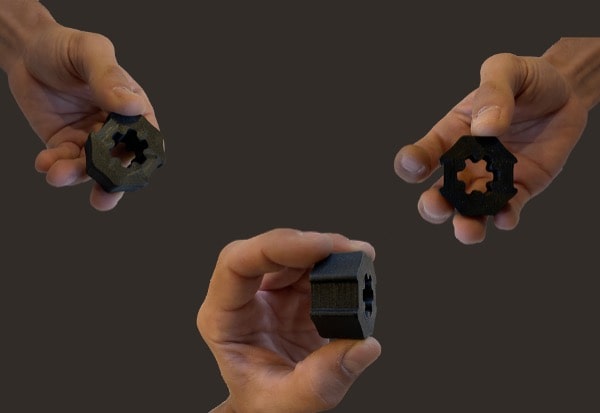