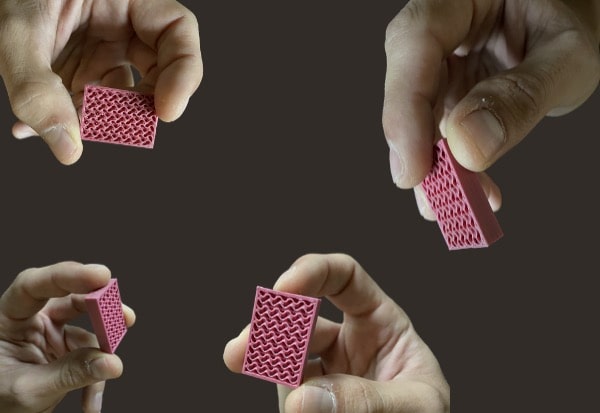
Shaping process
The most common are carbides such as SiC, the transition metal carbides TiC, ZrC, HfC as well as VxC, NbxC, TaxC, MoxC, WxC and nitrides such as Si3N4, AlN, TiN, etc.
Because of their properties (high melting temperature, high hardness, lack of ductility at low temperatures, brittleness, low toughness), ceramic objects are generally obtained by consolidation at high temperature (sintering) of a granular structure (part raw or green piece) developed by implementing a shaping process.
The most used shaping processes are casting, pressing, injection, extrusion. The deposition methods (vapor phase, plasma spraying, etc.) should be added to this. The organic liquids and auxiliaries used during these stages are removed (drying, debinding) before sintering.
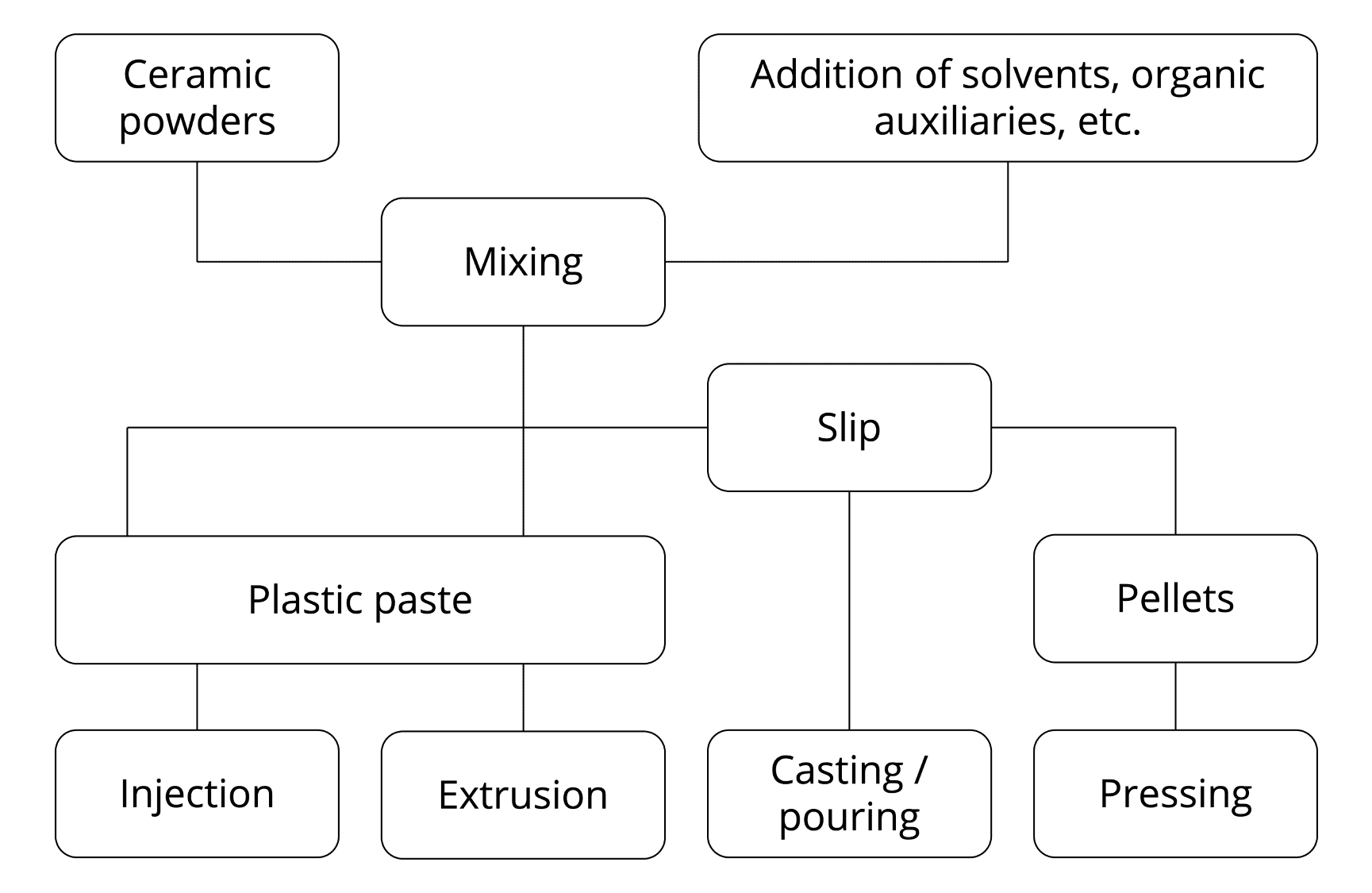
The shaping of traditional ceramics can be done using a suspension (wet process), plastic paste (semi-wet process) or granules (dry process). These are essentially criteria of size and shape of the parts and production cost that govern the choice between these three paths.
From suspension
The aqueous suspensions of mineral raw materials used for the preparation of ceramics are called slurries. They generally contain a significant fraction of large grains (> 40 μm). They are used in particular in the porous mold casting and pressure casting processes, for the shaping of objects of complex shape (decorative pieces or dishes) and / or of large size (sanitary).In all cases, consolidation, called setting, must occur before the mold is removed and the part is handled. It occurs most often after extraction of part of the water from the slip and formation against the walls of the mold of a layer of wet material, called cake or cake. The shaping is always followed by a drying step.
In the case of mold casting, the water is transferred into the porosity of the mold. If the pores of the mold are significantly smaller than those of the cake, the transfer occurs without external stress under the effect of the capillary suction. The use of a degreaser made up of large grains (> 40 μm), which stabilize large pores within the cake, can therefore be very favorable. In practice, the pore size is centred on 1 μm for plaster molds and on 15 μm for resin molds (need to apply pressure in the latter case).
From plastic paste
Plastic pastes behave like non-Newtonian fluids with a high threshold stress. They are used for shaping by injection, pressing or extrusion (parts of simple geometry and / or axial symmetry). Their water content depends on the nature of the clay contained in the mineral mixture and the shaping conditions. It varies between 18% (hard paste for extrusion) and 30% (soft paste for injection) of the mass of dry matter. In all cases, the products must be dried before cooking.From pellets
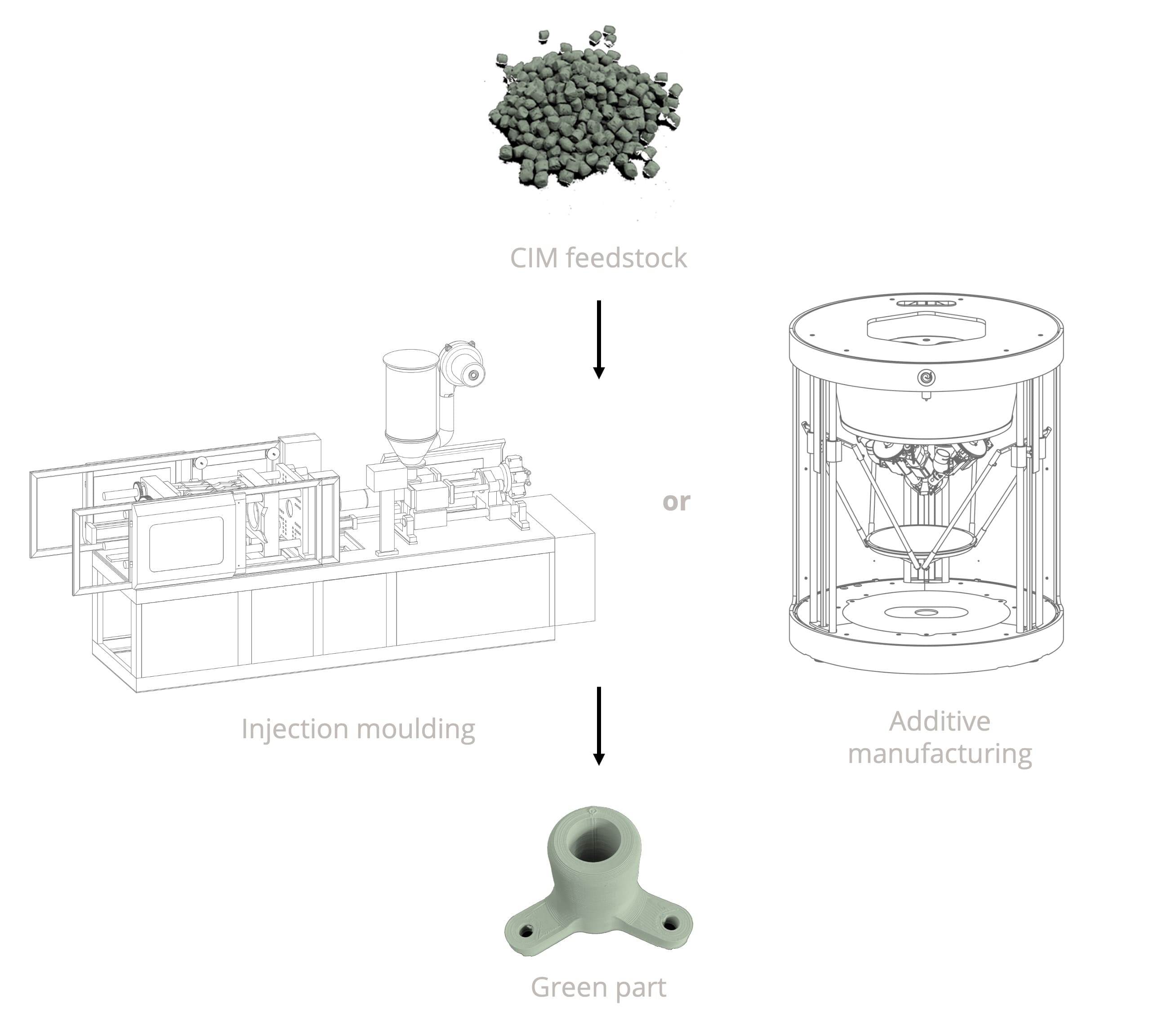
The shaping of parts of simple geometry can be carried out by pressing. To obtain a homogeneous filling of the pressing matrix, it is customary to use the raw materials in the form of spheroidized granules (generally between 300 and 600 μm in diameter) having a high flowability. Obtained by mechanical granulations or by spraying / drying, these granules contain only the water (or the binder) necessary for their cohesion (a few % by mass). It is therefore easier to dry the part. This route is widely used for shaping floor or wall tiles.
Discover Metal and Ceramic 3D printed parts
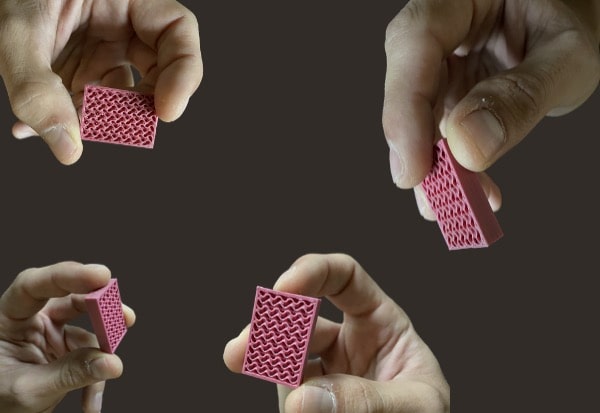
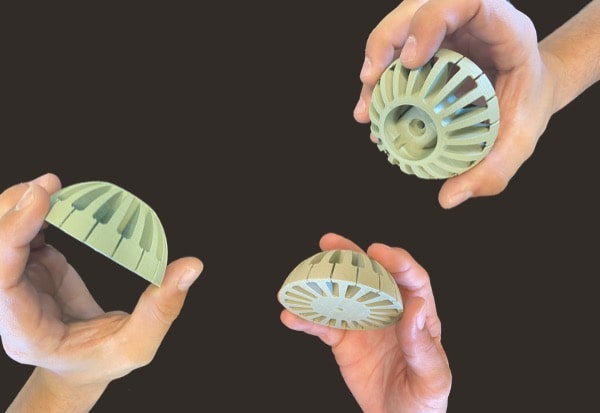
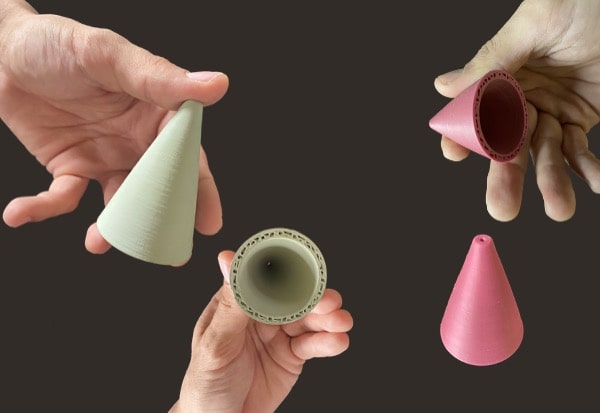