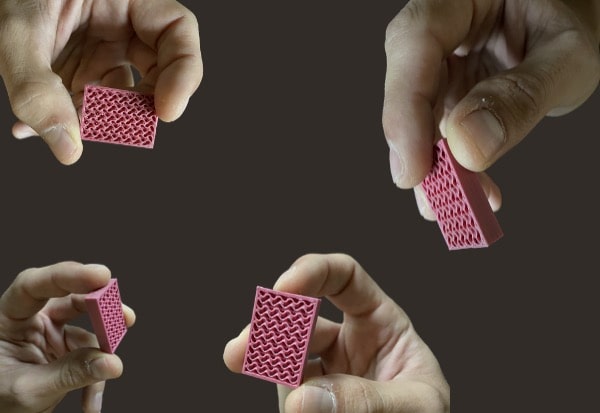
PiM & PiM-like
Processes design principles
Every manufacturing process has its how design principles and guidelines. Using pellet PiM-Like technologies as a complement of PiM process requires to take into account some design rules to optimize the parts to produce for both processes. The objective of this note is to present the main principles to follow.
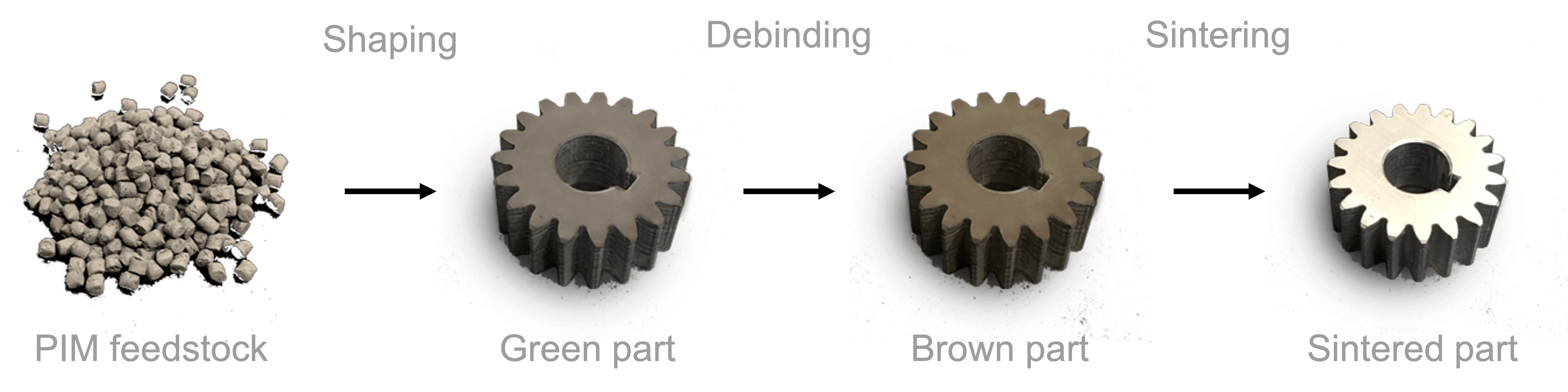
Maximum and minimum part sizes – Shapes - Wall thickness - Corners and radii – Undercuts – Threads – Reinforces - Sintering supports - 3D printing guidelines.
Discover Metal and Ceramic 3D printed parts
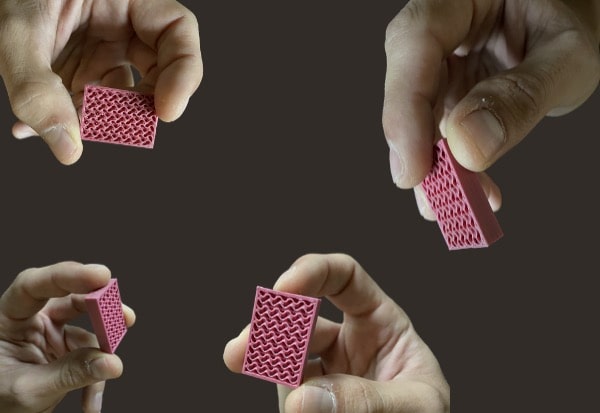
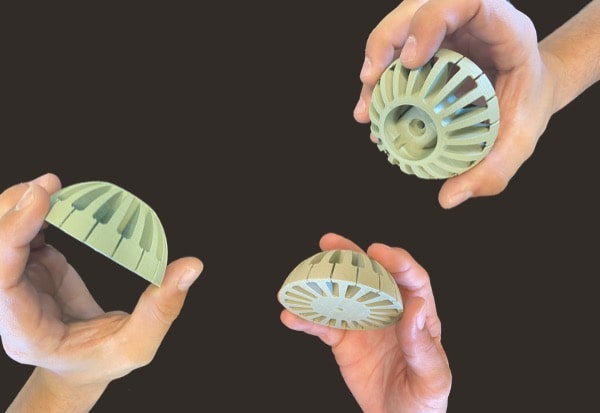
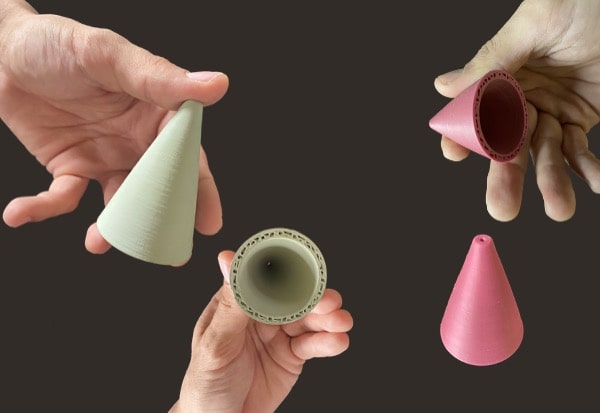