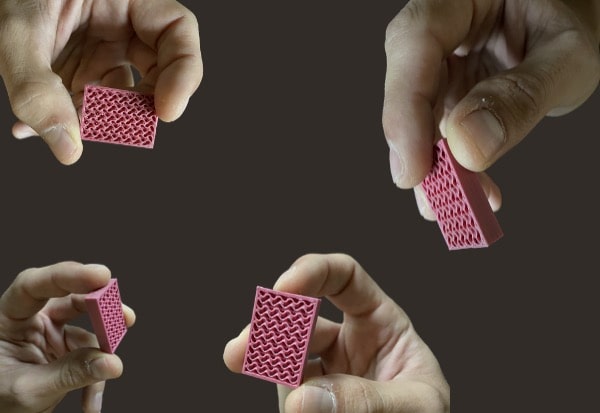
PiM & PiM-like
Régles de conception
Chaque procédé de fabrication a ses propres principes et directives de conception. L'utilisation des technologies PIM-Like pour les granulés en complément du procédé PiM nécessite de prendre en compte certaines règles de conception afin d'optimiser les pièces à produire pour les deux procédés. L'objectif de cette note est de présenter les grands principes à suivre.
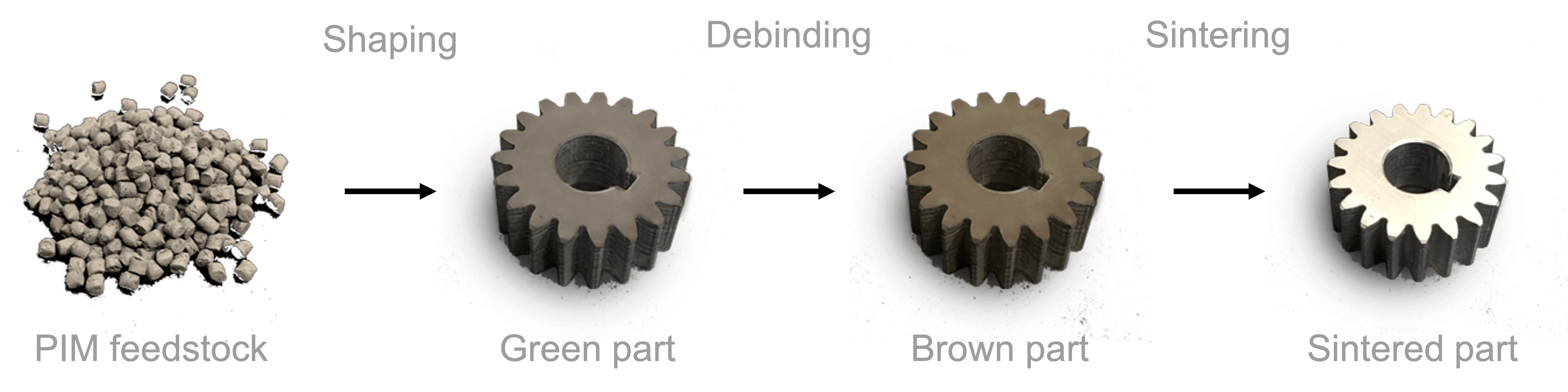
Dimensions maximales et minimales des pièces - Formes - Épaisseur des parois - Angles et rayons - Contre-dépouilles - Filets - Renforts - Supports de frittage - Régles pour l'impression 3D.
Découvrez les pièces imprimées en Métal et en Céramique
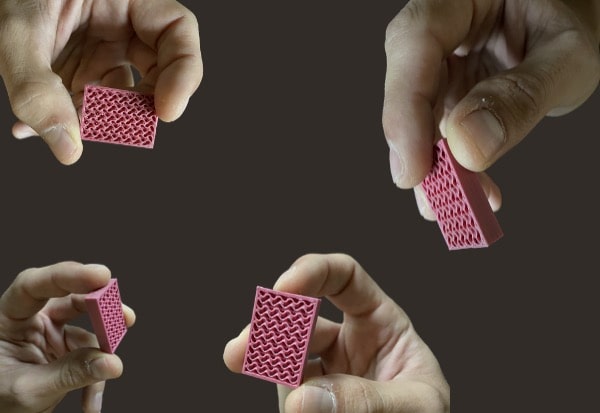
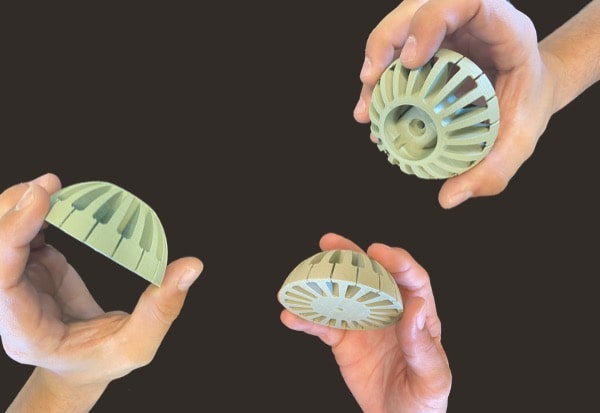
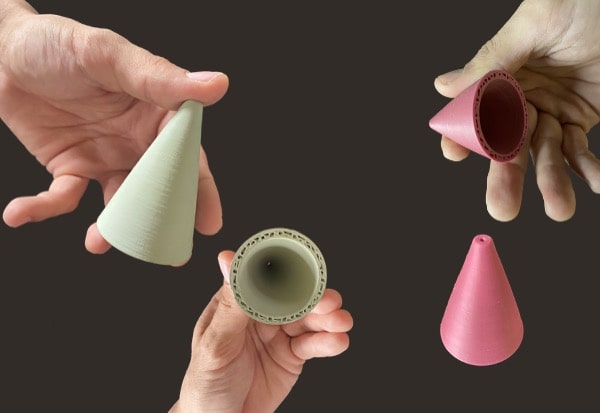