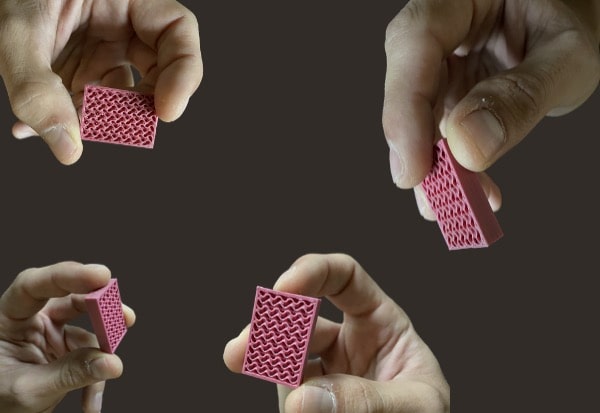
MiM & MiM-Like
Why and when using it?
Surface treatments are very common for MiM & MiM-Like parts, its aim is to improve functions and aesthetics.
It exists a wide range of metalworking technologies, all are not adapted to each part complexity and volume requirements. MiM & MiM-Like are generally used to produce complex shaped, high density, high-performance metal parts.
MiM is mainly used in the automotive, medical and dental instruments, Computer and electrical applications, aerospace and defence markets, etc.
MiM-Like answers a large range of market applications from unique parts to medium series, where traditional MiM part are not competing due to mould cost.
MiM process is best applied to small and medium size parts that are often complex in nature with high annual part volumes. Thanks to pellet MiM-like additive technology such as Pam Series MC, MiM is now economically viable from 1-unit part and with no tooling investment.
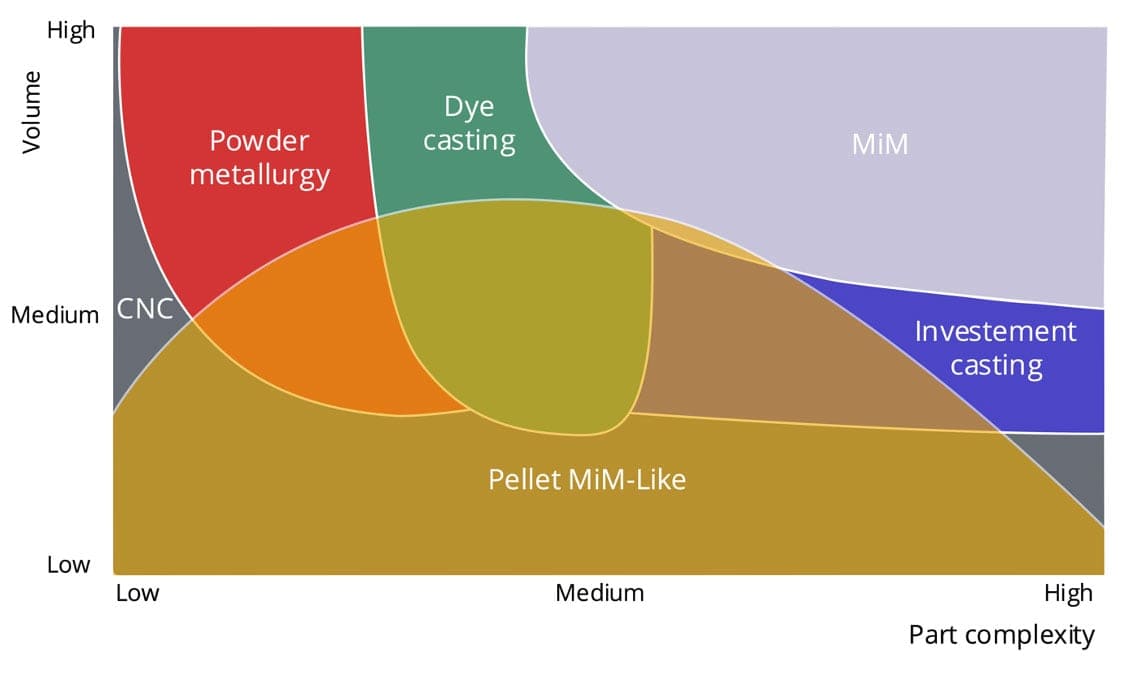
MiM & pellet MiM-like processes are compatible with almost all type alloys such as ferrous and non-ferrous alloys, titanium, copper, nickel, etc.
Benefit from enhanced properties: MiM & MiM-Like parts are typically 96% to 99% dense, approaching wrought material properties and can achieve higher mechanical strength, corrosion resistance, magnetic properties than conventional powder metallurgy processes and traditional casting.
Reduce design constraints: MiM & MiM-Like offer design flexibility as traditional plastic injection moulding process. For example, some complex parts produced with conventional powder metal processes will require secondary operations, using MiM processes allow producing net shape parts.
Avoid subassemblies: MiM & MiM-Like processes can be used to combine different shapes into one, to avoid assemblies and reduce labour and additional operation costs.
Nevertheless, since every process comes with its own constraints, it is necessary to take into account some MiM conception guidelines during the design phases.
Discover Metal and Ceramic 3D printed parts
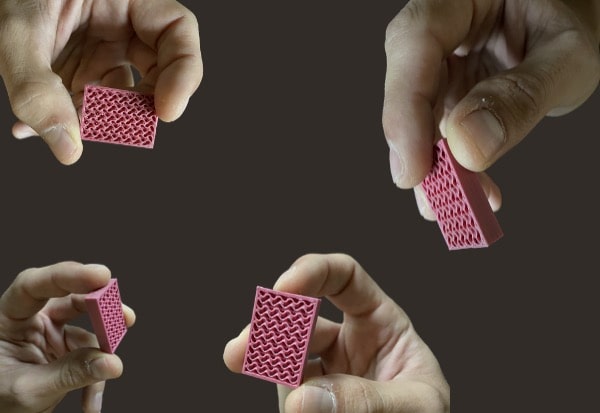
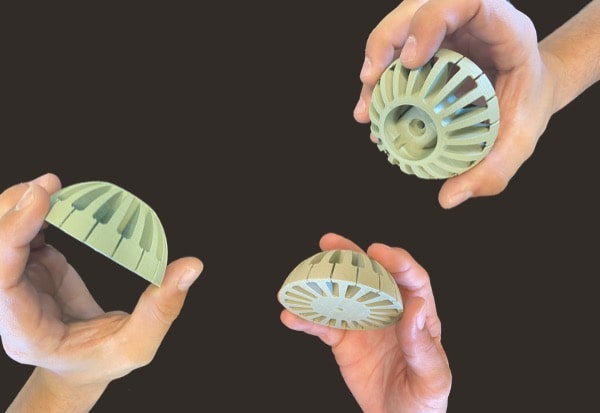
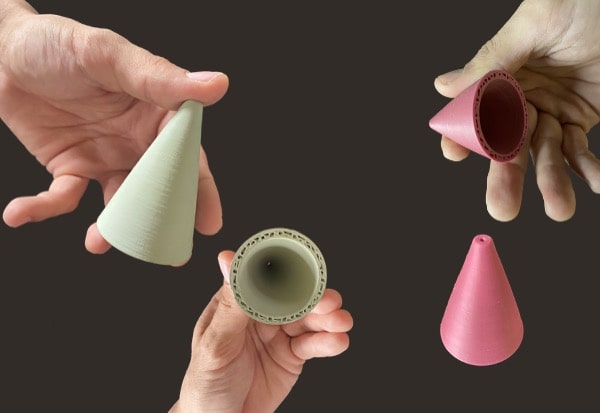