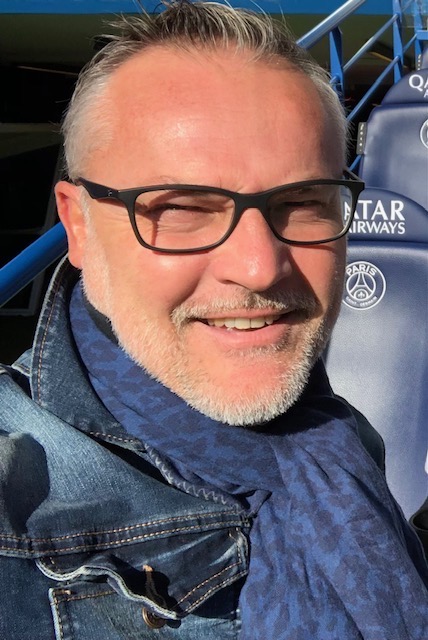
We are pleased to introduce in this article one of our users, Hervé Pelletier, University Professor and Co-responsible for the Work-Study Program in Plastics Processing at INSA Strasbourg.
INSA Strasbourg is a French engineering school whose specialties are oriented towards mechanical disciplines.
The curriculum offered by the Mechanical Department is itself divided into three specialties: Mechanical Engineering, Plastics Processing and Mechatronics, each of which may use 3D printing technologies.
It is within this Mechanical Department, among the INSA Strasbourg's materials platform, that Hervé has set up a unit dedicated to 3D printing.
He accepted to provide us with some information on the functioning of this unit, as well as on the various additive manufacturing projects he is currently working on.
With a background in metallurgy, and having started his work in 3D printing more than 15 years ago on SLM or EBM technologies, it is quite naturally that Hervé understood the potential of pellet-based additive manufacturing technologies (FGF). Following a public tender, his pick turned to PAM technology with the acquisition of a Pam Series MC system.
He explains: "The idea was not to create a Fablab, but above all to position ourselves on our expertise, which is the relationship between materials and processes. In other words, the link between the material property and the implementation process, in this case implementation processes by 3D printing. To date, we have three main families of technologies: a resin technology (with some SLA, DLP or MSLA systems); FDM printers using filament; and of course the technology that makes our originality, the PAM technology using pellets. We have a Pam Series MC 3D printer, i.e. a high-temperature version offering the possibility of using metallic materials, which is the main reason why we chose this model.“
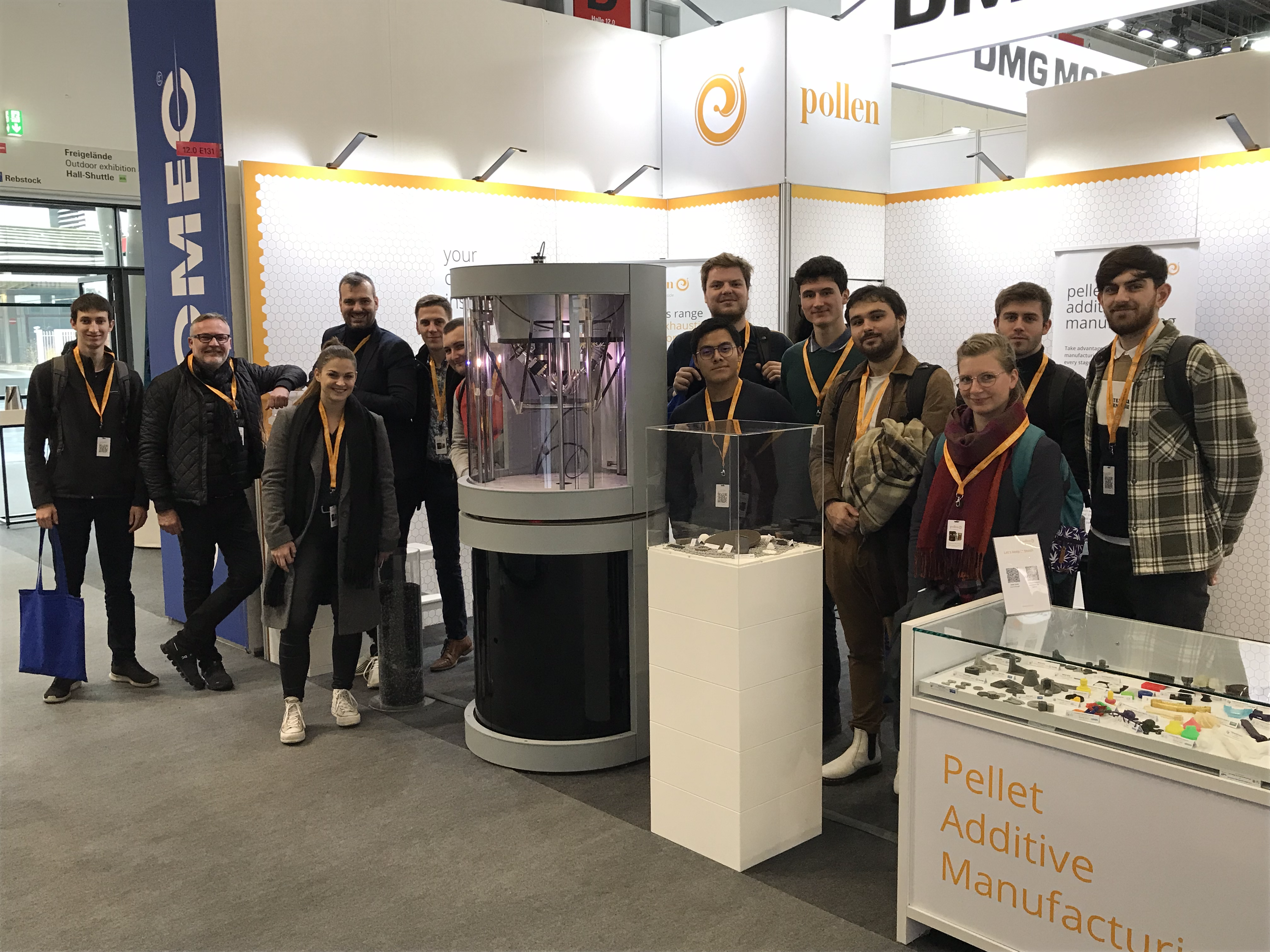
Pellet 3D printing combined with a powerful training tool to serve as teaching support.
Hervé explains how he is able to use Pam 3D printers to pass on his knowledge of additive manufacturing, awakening and nurturing an interest in 3D printing technologies among his students.
He explains: "I mainly use this type of industrial printer for demonstration purposes during my courses. Indeed, on small 3D printers such as FDM or SLA, a simple tutorial is necessary; but on a complete and advanced system such as the Pam, it is necessary to already have a reflex of plastics processing. During my lessons, I launch a print at the beginning of the session (I choose a part that will be printed during the course), I show beforehand how to fill the pellets in the material cartridges, how to extrude the wire in preparation for printing, and then the course continues as usual.”
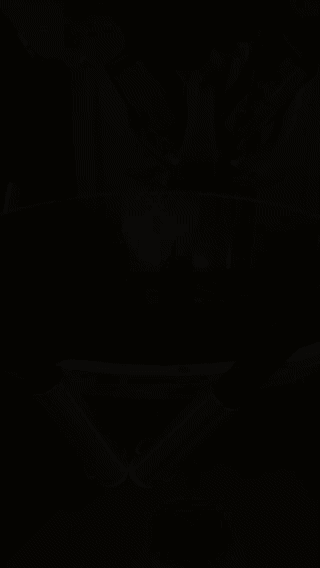
Therefore, while relying on the Pam printer as a demonstration medium for his teaching, Hervé regularly distributes 3D printed technical parts among the ranks of his students.
He continues: "Nevertheless, this year I am also involving some students in a more in-depth way on specific long-term projects. This allows me to really take the time to train them on the Pam 3D printer. They have plenty of time to browse the support and training platform provided by Pollen AM to expand their knowledge of additive manufacturing and to improve their skills in parallel of my teachings. These projects allow us to take the time and move forward step by step."
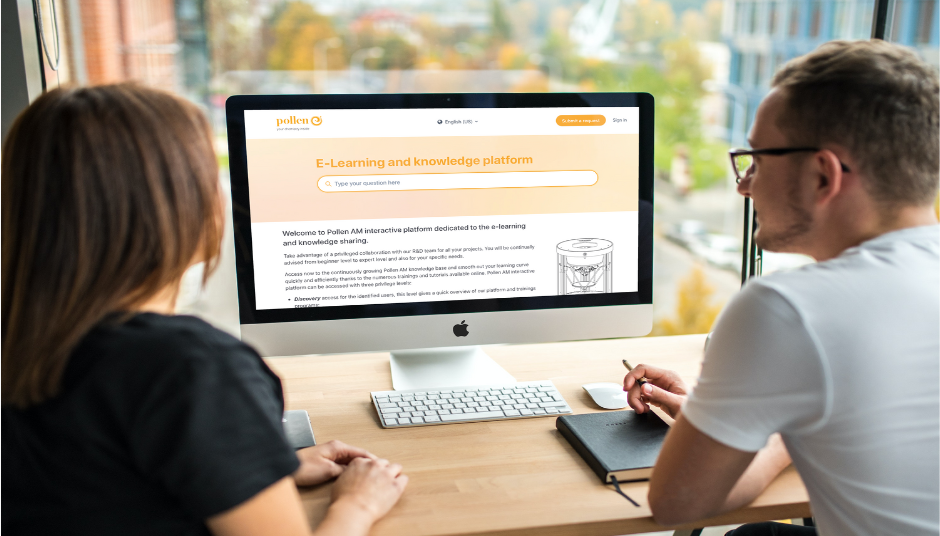
Indeed, to facilitate the use of its Pam 3D printer, INSA Strasbourg has been given access to Pollen AM's E-learning and knowledge sharing platform: "I use the training platform a lot, whether for myself or when I involve students in projects concerning the Pam. I don't tamper with language, when something goes wrong, I say so; and honestly, I find this training platform very useful and well done!"
Pam Series MC, a 3D printer adapted to academic research...
INSA Strasbourg's main challenge was to find a 3D printing technology that could be used to shape metal parts without resorting to free powder or energy sources such as laser and electron beam, for the sake of student safety and comfort.
Indeed, instead of using volatile powder as raw material, PAM technology inspired by injection molding uses pellets, encapsulating these metallic or ceramic powders in a binder coating. This allows for easier storage of the materials, as well as a reduced risk of inhalation or irritation for the operators.
Hervé explains: "I oversaw a student who worked on the subject of metal parts 3D printed with pellets and filaments. We mainly dealt with 316L Stainless Steel material, and the next step would be Copper, especially by observing the alternatives offered by MiM pellets, materials provided by PolyMiM."
He then explains the work he is carrying out: "I currently have one potential application in mind concerning micro-heat exchangers. The idea of the latter would be to create a new generation of heat exchangers by miniaturizing the structure as much as possible while keeping the exchange surfaces as large as possible."
"We are currently working on CAD models to make them compatible with 3D printing and the necessary debinding and sintering steps. For these post-processing steps, we will initially use a service provider."
"Moreover, we are working in parallel with the same student on chiral structures, initially printed in SLM due to the very small dimensions of the parts, but soon on Pam printers."
"We are talking about chiral structures here, but there are many different structures that can be 3D printed today, including lattice or Voronoi structures for example!"
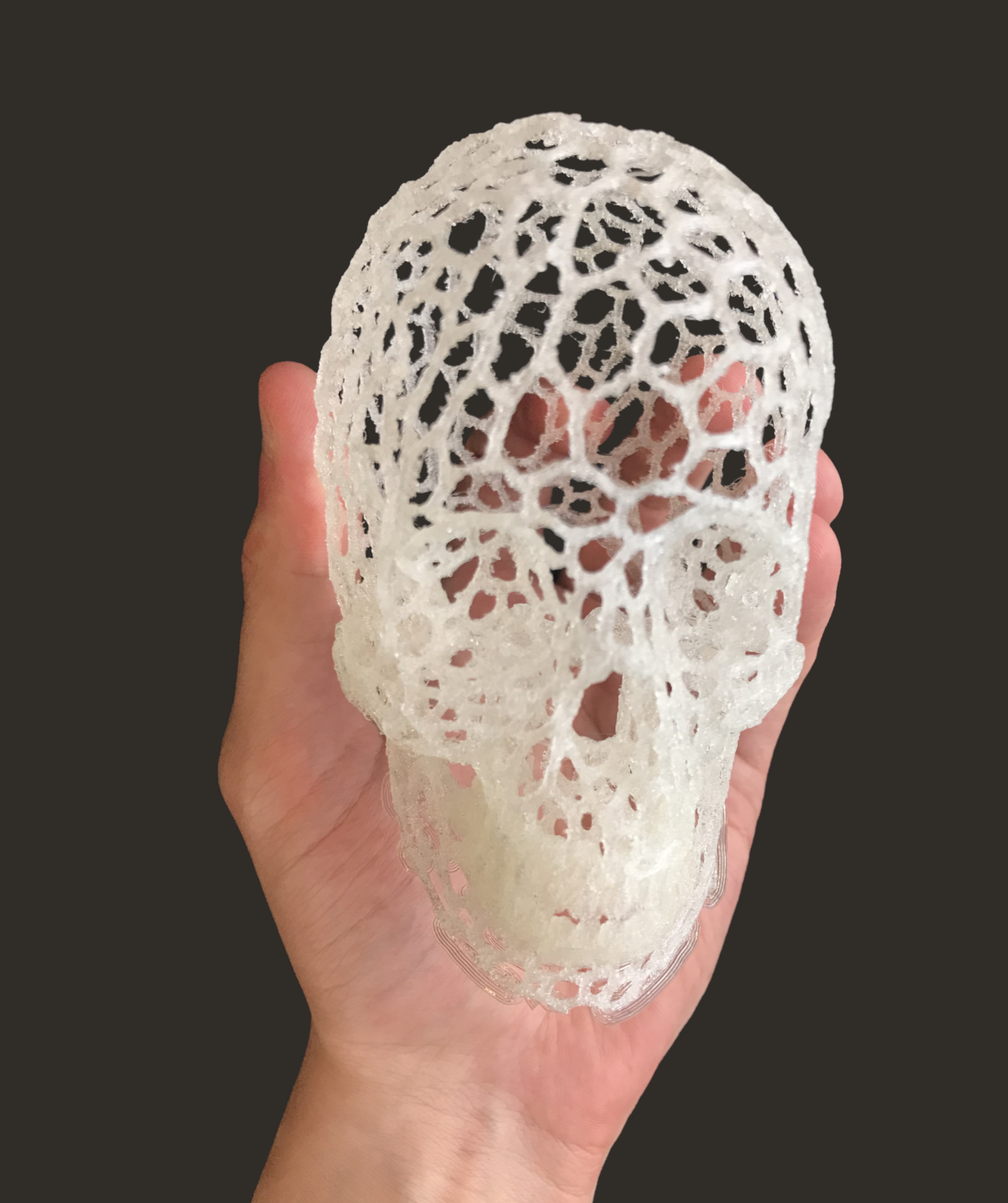

...while responding to various industrial applications with the printing of flexible, high-performance or filled thermoplastics!
Hervé then gives us an overview of his current projects: "At the moment I am working on a production project for an industrial company [Confidential] which involves a student who has done an internship at Pollen AM, and who is therefore already trained on Pam printers."
"We will be performing pre-tests on two different types of soft parts printed on Pam, in a TPE Shore 00 material supplied by Kraiburg TPE as well as in a TPE 35 Shore D material supplied by BASF. With the goal of producing two final parts that will fill the role of protective bars on a bicycle-drawn cart, TPEs are here being used with shock absorption in mind."
Pollen AM was the first company to showcase its ability to produce 3D printed parts from TPE Shore 00 material, enabling the full Shore hardness scale of TPEs to be shaped!
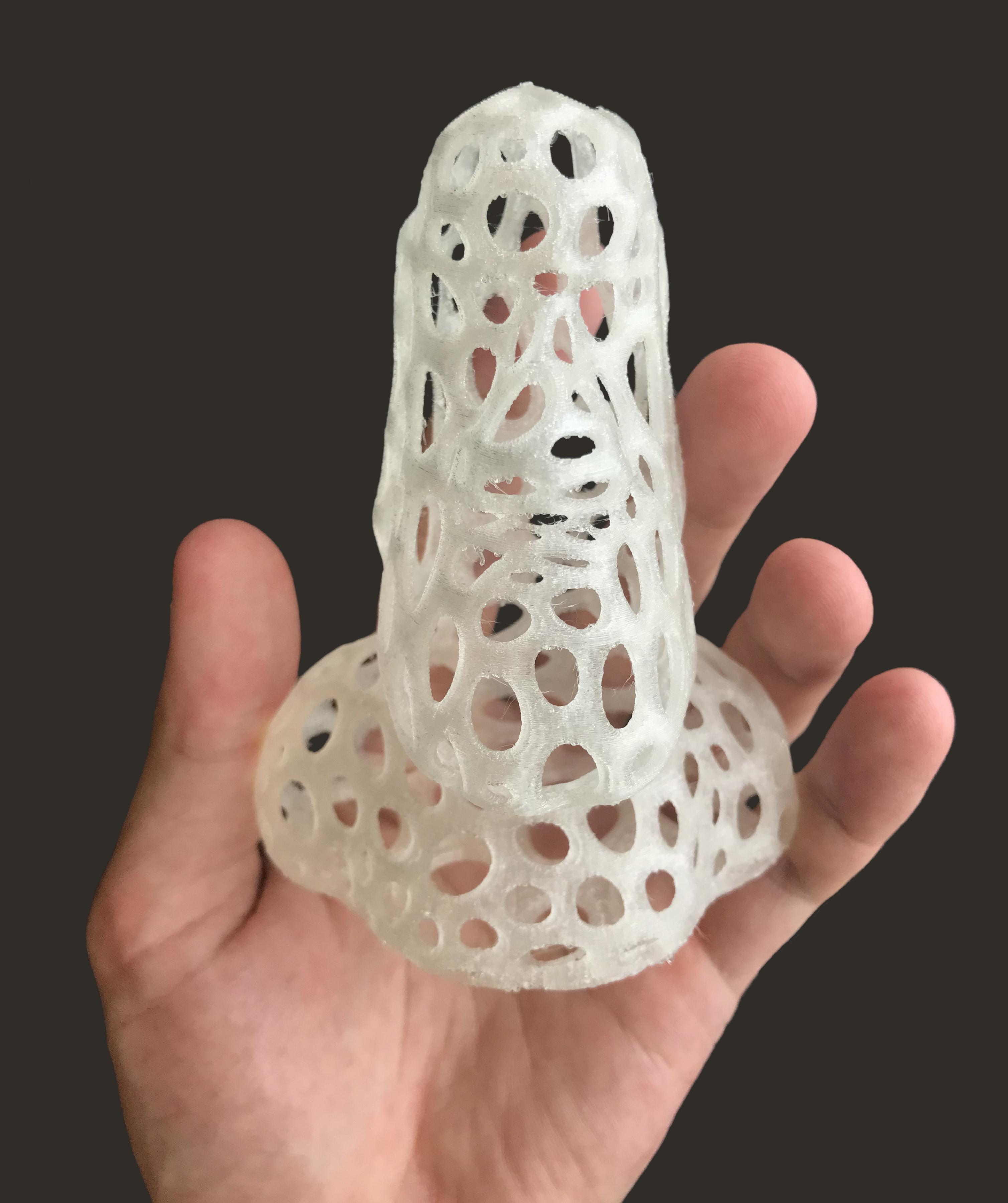
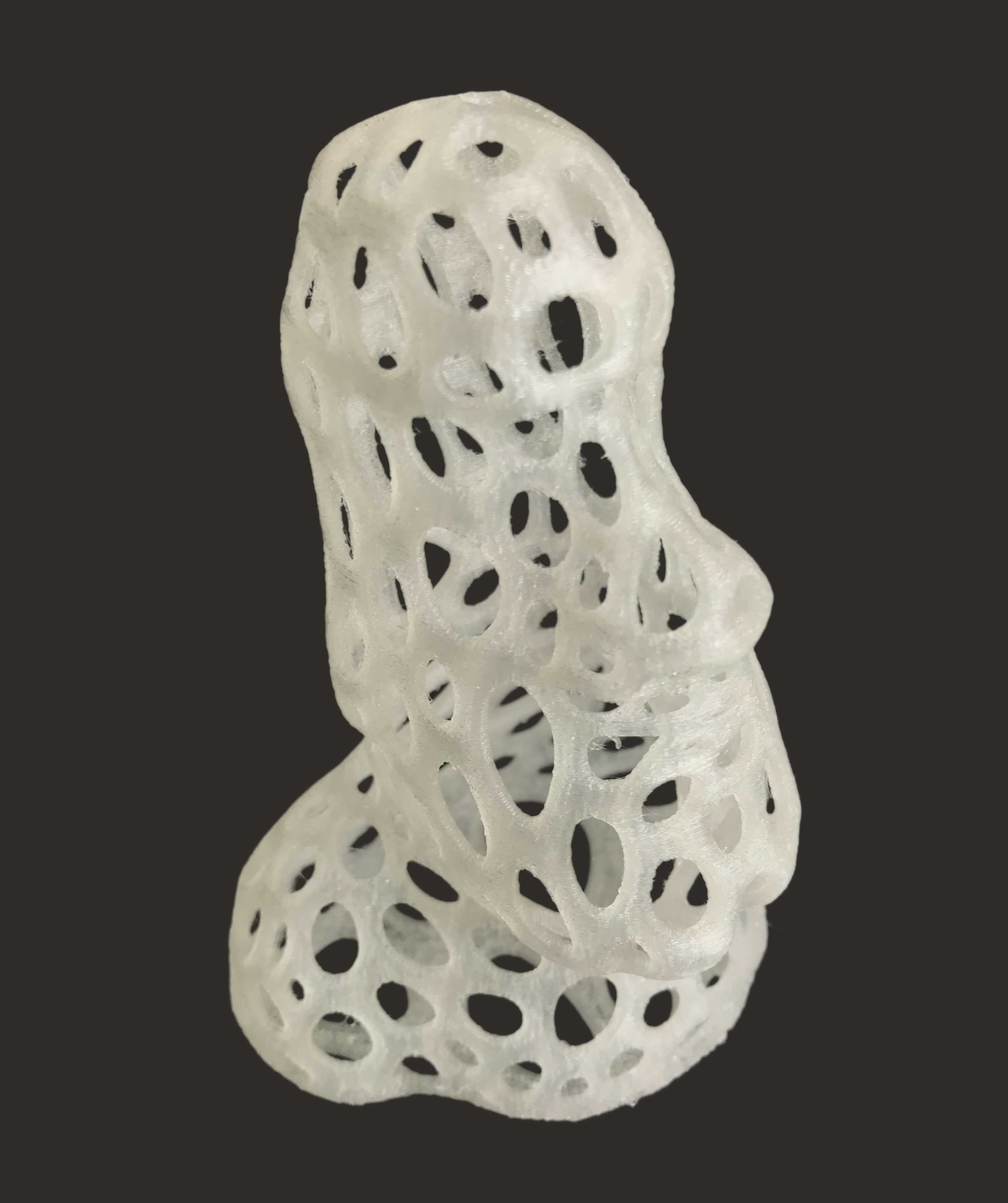
Hervé continues: "We will also have structural parts to produce for the same company, 3D printed in a rigid PA HT material filled with carbon fibers, and supplied by Lehmann&Voss&Co."
Indeed, Pam Series MC, because of its great versatility, also allows the shaping of fiber-filled performance and high-performance materials, such as Polyamide 6.6 Haute Température, chargé à 15% de fibres de carboneHigh Temperature Polyamide 6.6, filled with 15% carbon fibers. This material has a very good mechanical strength due to the presence of carbon fibers in its composition, as well as an excellent thermal resistance at high temperatures. These properties make it the material of choice for mechanical end parts subject to significant stress.
3D printing for complex research projects in mechanical applications
One of the advantages of the Pam 3D printers is the ability to mount up to four extruders on a single 3D printer, allowing for the printing of multi-material parts in a single run. The user can, for example, combine the properties of different elastomers, thus meeting a wide range of needs and industrial applications.
Hervé explains: "We started working quite recently on multi-material printing with Pam, regarding mechanical coupling systems. We are working on a bi-material structure, including a coupling zone with axes and shafts, designed in rigid material, and an intermediate zone printed in TPU, to bring flexibility to the system. The idea would be to create modernized gimbals on Pam. To do this, I use the tutorials on Pollen AM's e-learning and training platform to gain expertise in bi-materials."
We can imagine applications for the automotive or even railway industry, which rely heavily on this kind of mechanical parts combining flexibility and rigidity to better transmit the energy and power of the engine to the driving wheels.
He then proceeds to say: “The next step would be to progressively shape high performance polymers, offering high mechanical resistance at high temperatures, and then technical ceramics in the longer term.”
Stay tuned for future releases!
It was a real pleasure for us to hear Hervé Pelletier's fascinating testimony, and we thank him for all the details about his applications and projects on Pam.
Hervé also provides scientific and technical consulting services in 3D printing, whether it be for the production of functional parts, the installation of 3D printing systems, related training, etc. So if you experience this kind of needs, do not hesitate to contact Hervé on Linkedin (Indip3D) or directly by email at indip3D@gmail.com!
If you liked this article, come and follow us on Linkedin to keep up to date with our news and discover future testimonials. Also, if you are a Pam user, and you want to share your experience and opinion about the machine, you can contact us at the email address contact@pollen.am or directly through the forms on our website.
Newsletter
sign up for updates
We’ll never share your email address with anyone.
And you can opt out at any time. We promise.
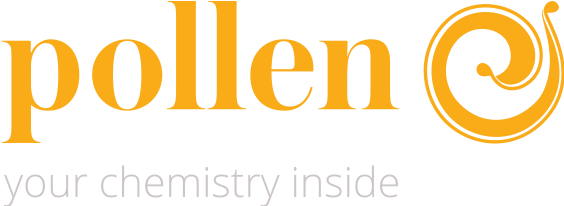
© 2025 Pollen AM inc. All rights Reserved.