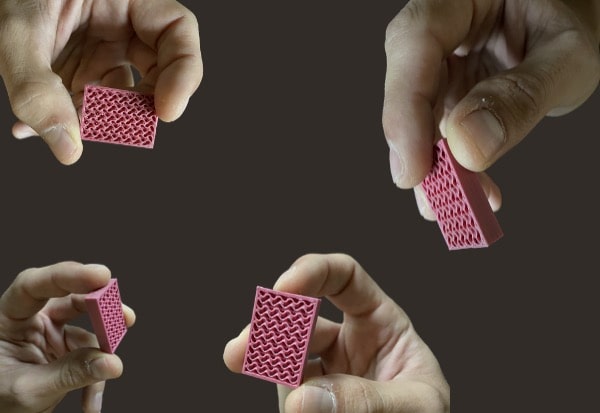
Processus de mise en forme
Les plus courants sont les carbures tels que SiC, les carbures de métaux de transition TiC, ZrC, HfC ainsi que VxC, NbxC, TaxC, MoxC, WxC et les nitrures tels que Si3N4, AlN, TiN, etc.
En raison de leurs propriétés (température de fusion élevée, grande dureté, manque de ductilité à basse température, fragilité, faible ténacité), les objets en céramique sont généralement obtenus par consolidation à haute température (frittage) d'une structure granulaire (pièce brute ou pièce verte) élaborée par la mise en œuvre d'un processus de mise en forme.
Les procédés de mise en forme les plus utilisés sont le moulage, le pressage, l'injection, l'extrusion. Il convient d'y ajouter les méthodes de dépôt (phase vapeur, pulvérisation plasma, etc.). Les liquides organiques et les auxiliaires utilisés lors de ces étapes sont éliminés (séchage, déliantage) avant le frittage.
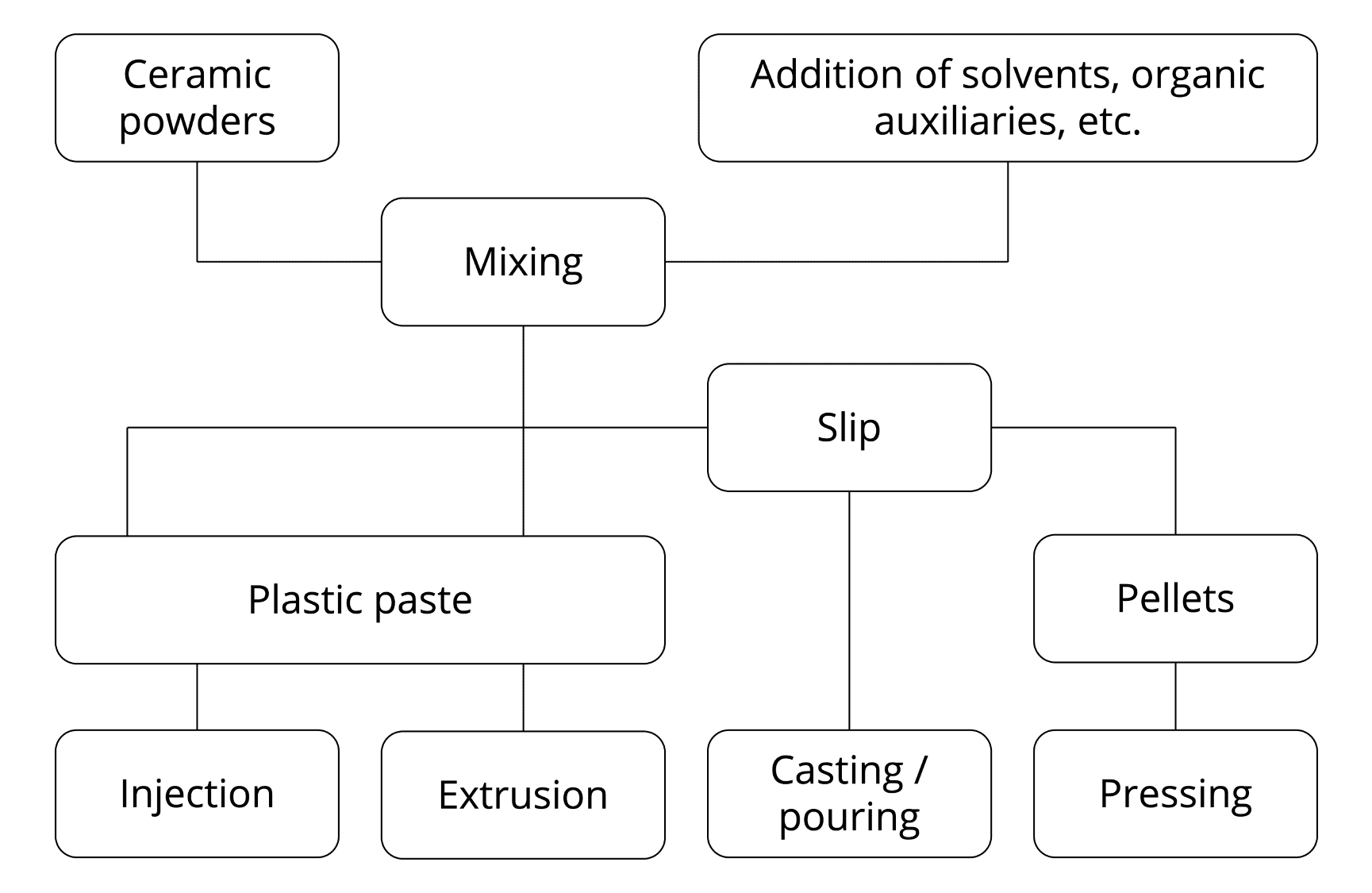
La mise en forme des céramiques traditionnelles peut se faire à l'aide d'une suspension (procédé humide), d'une pâte plastique (procédé semi-humide) ou de granulés (procédé sec). Ce sont essentiellement des critères de taille et de forme des pièces et de coût de production qui déterminent le choix entre ces trois voies.
A partir de suspension
Les suspensions aqueuses de matières premières minérales utilisées pour la préparation des céramiques sont appelées boues. Elles contiennent généralement une fraction importante de gros grains (> 40 μm). Elles sont utilisées notamment dans les procédés de moulage en moule poreux et de moulage sous pression, pour la mise en forme d'objets de forme complexe (pièces décoratives ou vaisselle) et/ou de grande taille (sanitaire).Dans tous les cas, la consolidation, appelée prise, doit intervenir avant le démoulage et la manipulation de la pièce. Elle se produit le plus souvent après extraction d'une partie de l'eau de la barbotine et formation contre les parois du moule d'une couche de matière humide, appelée cake. La mise en forme est toujours suivie d'une étape de séchage.
Dans le cas du moulage, l'eau est transférée dans la porosité du moule. Si les pores du moule sont nettement plus petits que ceux du cake, le transfert se fait sans contrainte extérieure sous l'effet de la succion capillaire. L'utilisation d'un dégraissant composé de gros grains (> 40 μm), qui stabilisent les gros pores au sein du cake, peut donc être très favorable. En pratique, la taille des pores est centrée sur 1 μm pour les moules en plâtre et sur 15 μm pour les moules en résine (nécessité d'appliquer une pression dans ce dernier cas).
A partir de pâte plastique
Les pâtes plastiques se comportent comme des fluides non newtoniens avec une contrainte de seuil élevée. Elles sont utilisées pour la mise en forme par injection, pressage ou extrusion (pièces de géométrie simple et/ou à symétrie axiale). Leur teneur en eau dépend de la nature de l'argile contenue dans le mélange minéral et des conditions de mise en forme. Elle varie entre 18% (pâte dure pour l'extrusion) et 30% (pâte molle pour l'injection) de la masse de matière sèche. Dans tous les cas, les produits doivent être séchés avant cuisson.À partir de granulés
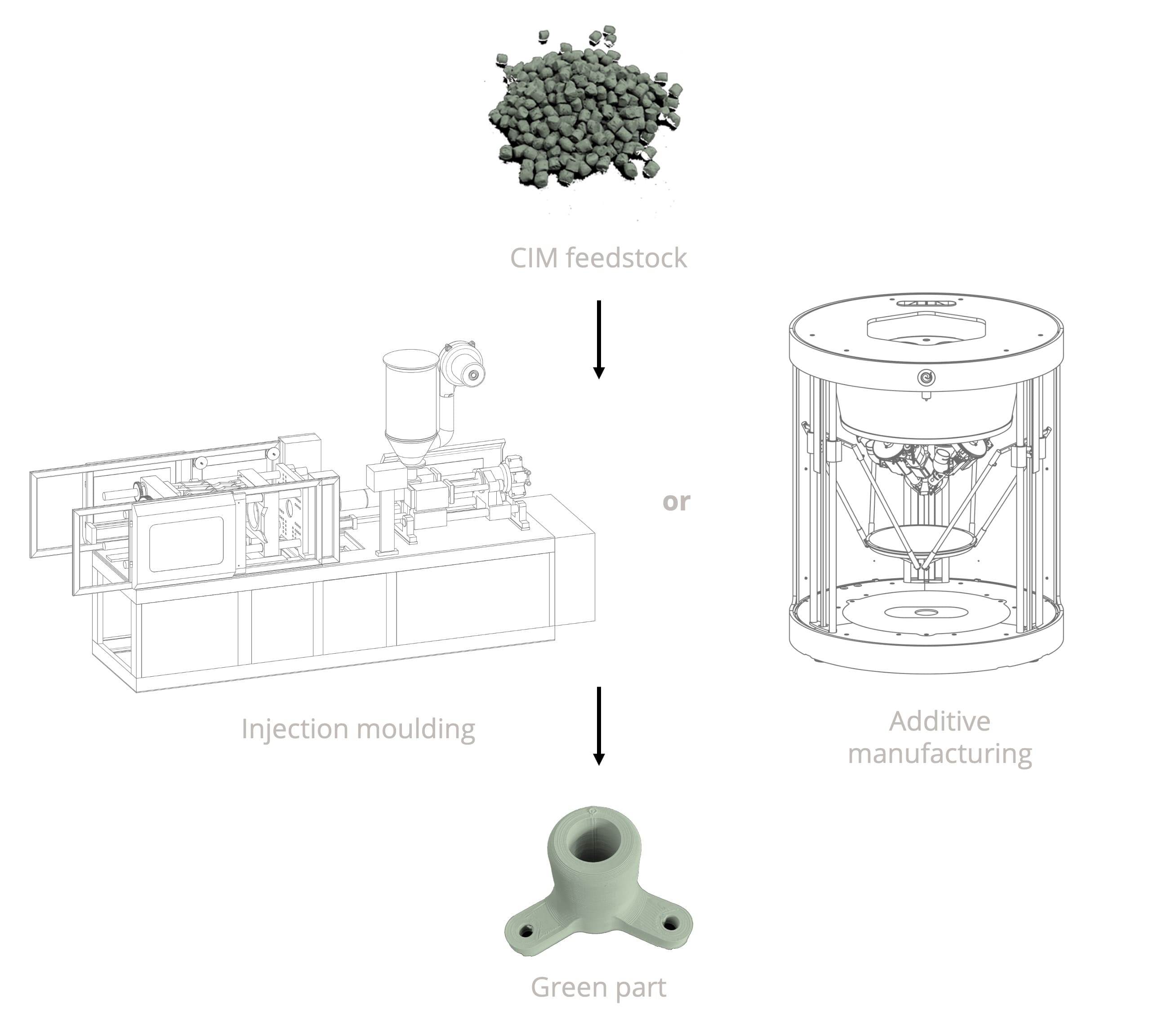
La mise en forme de pièces de géométrie simple peut être réalisée par pressage. Pour obtenir un remplissage homogène de la matrice de pressage, il est d'usage d'utiliser les matières premières sous forme de granulés sphéroïdisés (généralement entre 300 et 600 μm de diamètre) ayant une grande fluidité. Obtenus par granulations mécaniques ou par pulvérisation / séchage, ces granulés ne contiennent que l'eau (ou le liant) nécessaire à leur cohésion (quelques % en masse). Le séchage de la pièce est donc facilité. Cette voie est largement utilisée pour le façonnage des carreaux de sol ou de mur.
Découvrez les pièces imprimées en Métal et en Céramique
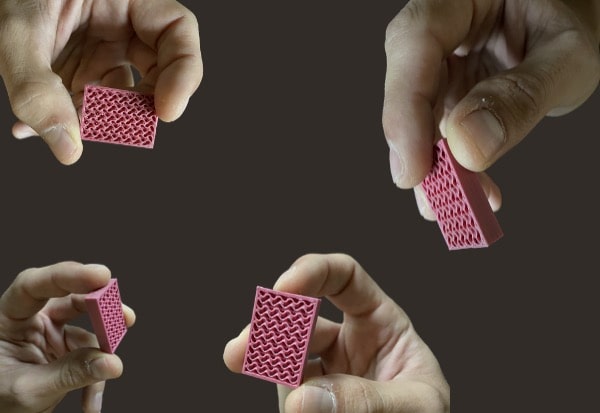
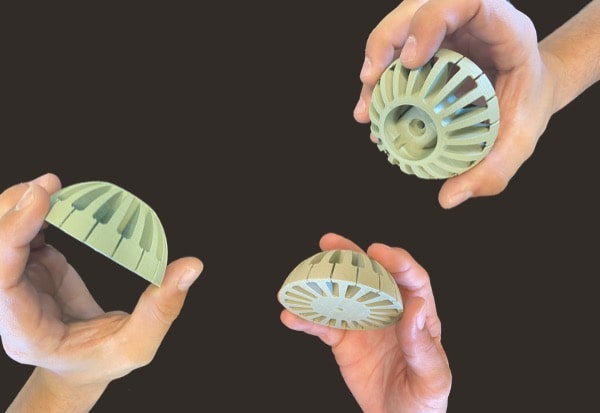
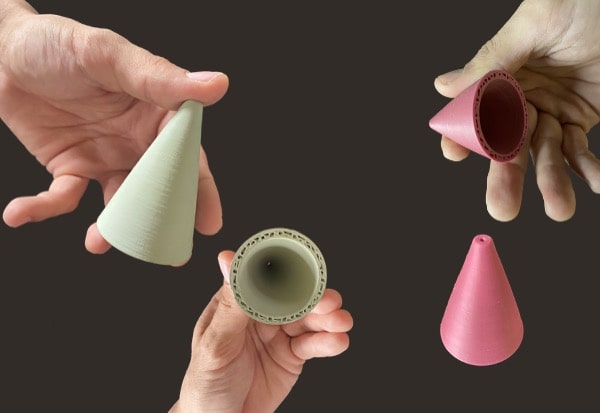