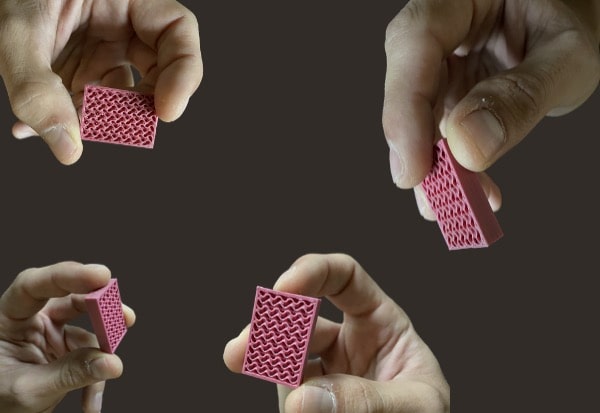
Utilisation de structures de support
avec les imprimantes 3D Pam
On appelle "supports" les structures générées pendant l'impression pour soutenir la pièce et qui seront retirées à la fin de l'impression.
Le support est utilisé pour permettre l'impression des surfaces en porte-à-faux de la pièce. S'il permet la réalisation de la pièce, le support engendre cependant quelques inconvénients :
- sa mise en œuvre accroît le temps d'impression, avec un matériau qui ne sera pas conservé dans la pièce à l'état final ;
- cela conduit à des opérations de post-traitement pour retirer les parties qui ont servi de support pendant l'impression.
Pour ces raisons, il est préférable de pouvoir imprimer une pièce sans avoir recours à un support.
Pour y parvenir, la première solution consiste à concevoir une pièce dont la géométrie n'implique pas l'utilisation de supports. Les principales règles de conception sont les suivantes :
- Conserver un angle de porte-à-faux supérieur à 45° par rapport à la plaque d'impression ;
- Conserver une longueur du porte-à-faux inférieure à 10 mm.
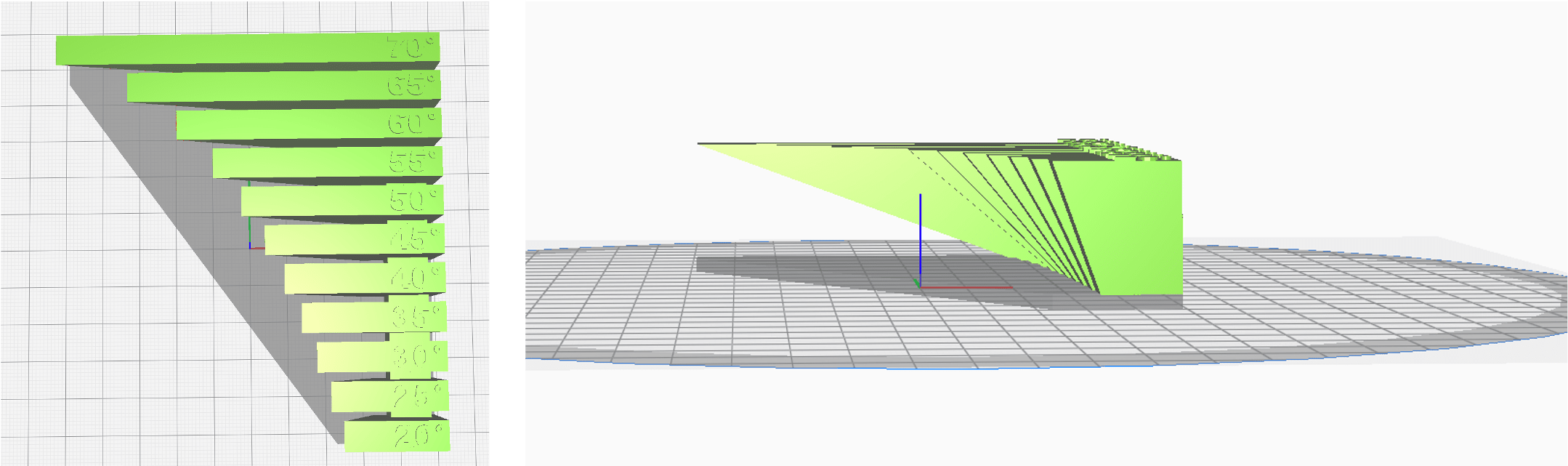
Echantillon de pièces pour tester le porte-à-faux
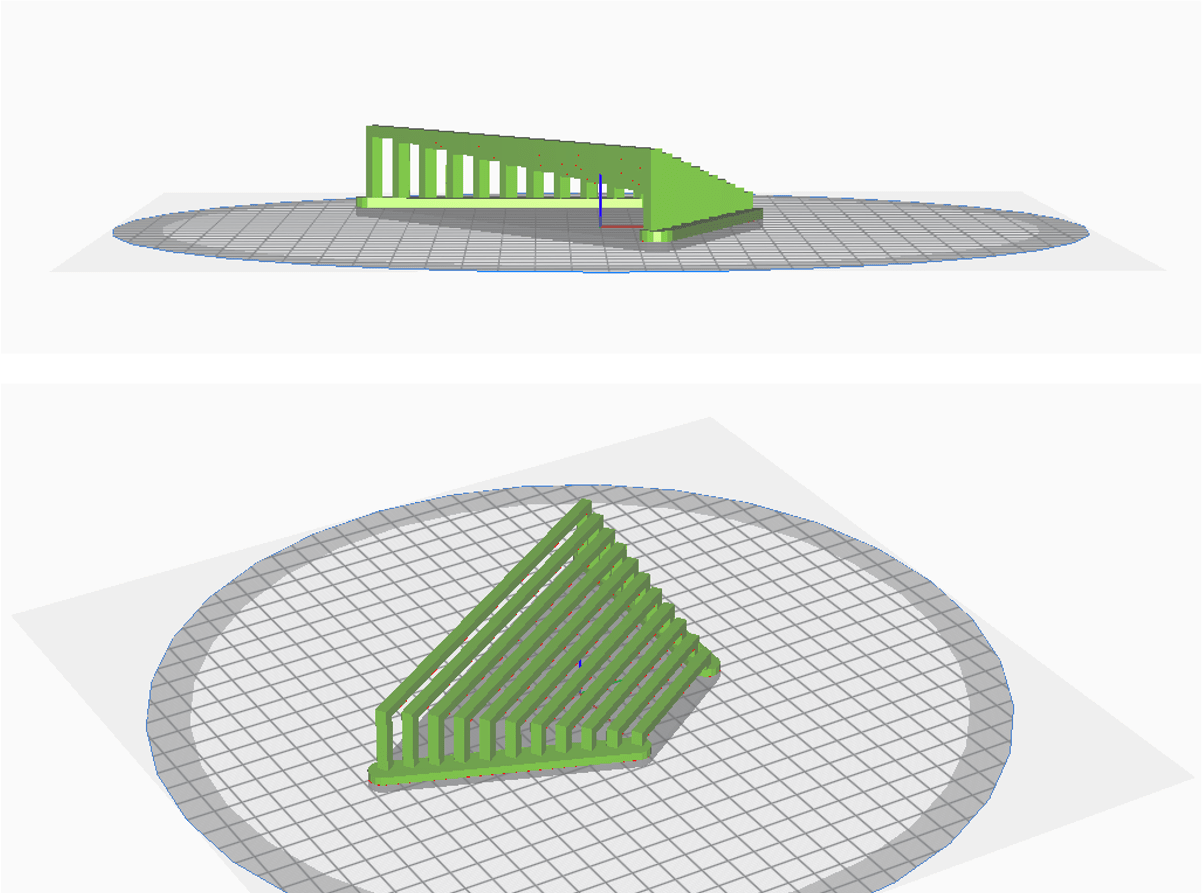
Echantillon de pièces pour tester le pontage
S'il n'est pas possible d'appliquer ces règles, une solution consiste à fabriquer la pièce en plusieurs parties qui seront ensuite assemblées par une technique conventionnelle.
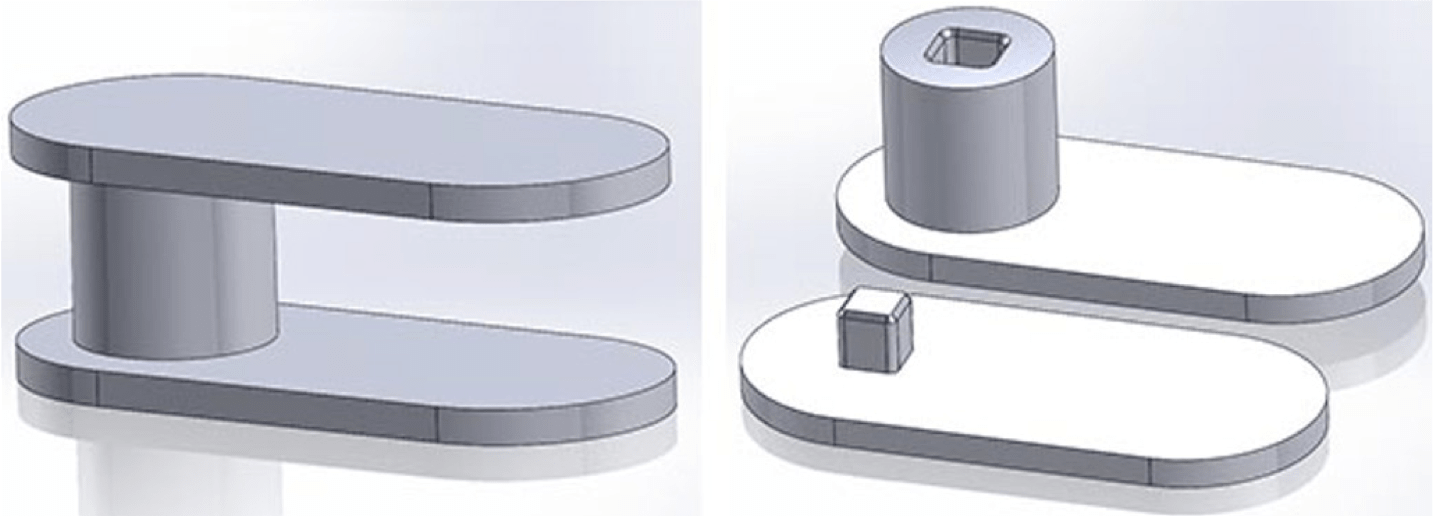
Si aucune de ces solutions n'est possible, vous allez devoir utiliser des supports pour imprimer la pièce.
Il existe deux stratégies de génération de supports :
- Le support est constitué du même matériau que la pièce imprimée : Les paramètres d'impression du support sont ensuite déterminés pour faciliter le retrait mécanique, par exemple en incorporant un espace entre la pièce et le support.
Malheureusement, cette solution nécessite beaucoup de temps et dégrade la surface aux interfaces pièce/substrat.
- Le substrat se présente sous la forme d'un matériau soluble dans un solvant :
Cette solution est de loin la plus confortable. Elle permet de générer des supports qui seront dissouts ultérieurement en plongeant la pièce dans un solvant.
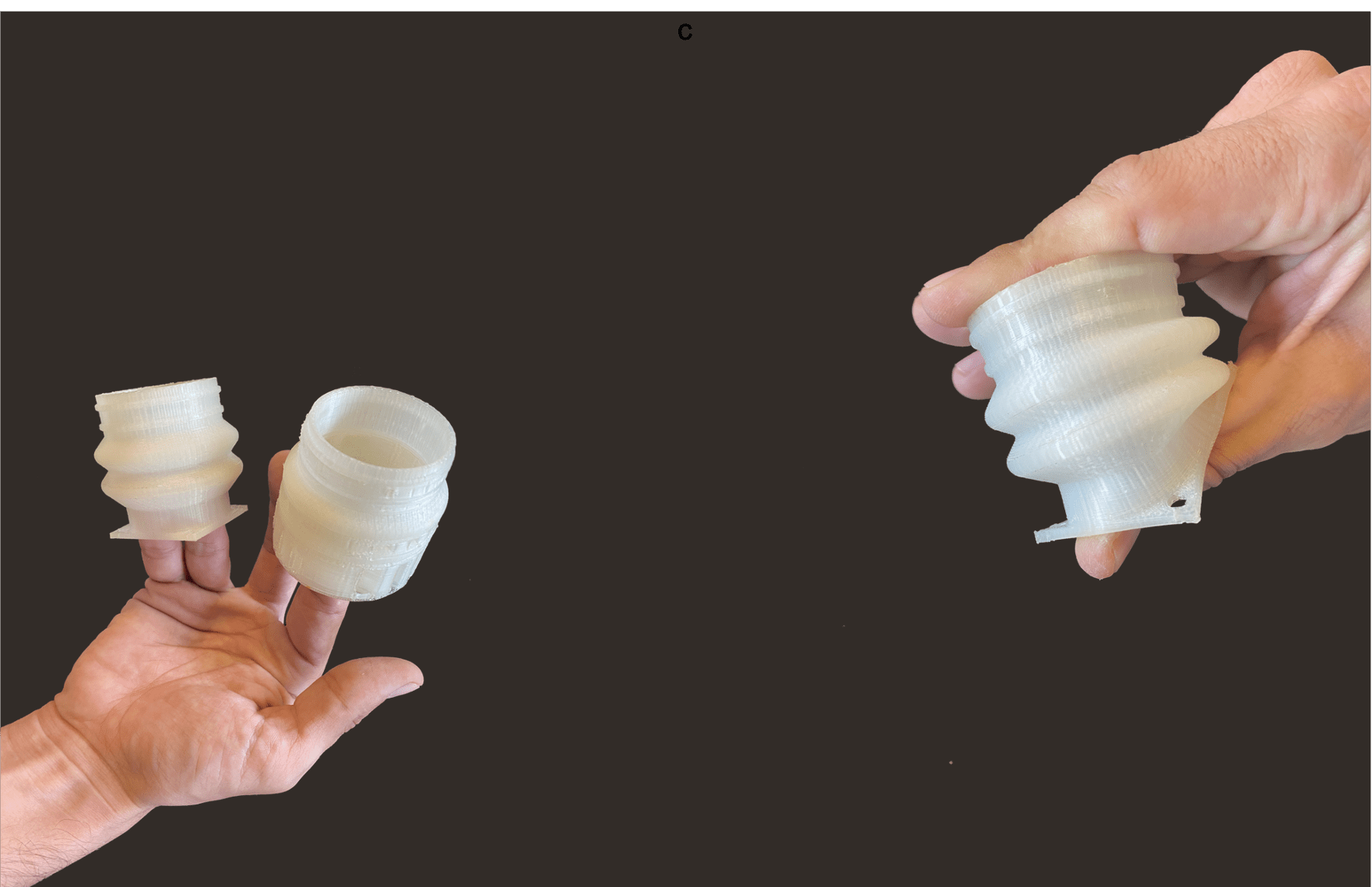
Pour mettre en œuvre cette solution, il est nécessaire d'identifier un matériau compatible qui adhère au matériau imprimé et qui est soluble dans un solvant sans impact sur le matériau imprimé.
Par exemple, le PLA peut être imprimé avec des substrats en PVA qui se dissolvent dans l'eau.
Il apparaît donc que l'utilisation d'un système ouvert utilisant le matériau sous sa forme la plus courante présente de nombreux avantages quant à la gestion du matériau de support. Il devient possible d'identifier les matériaux (ou les combinaisons de matériaux sous forme de mélange) qui présentent un intérêt en tant que matériau de support par rapport au matériau à traiter, puis de développer un profil d'impression adapté.
Synthèse de la gestion de la structure de support
Contraintes et éléments | Solutions proposées |
Étape de la chaîne d'impression 3D | Bonnes pratiques |
---|---|---|---|
Aucune structure de support nécessaire - Recommandation |
Éviter les surfaces en porte-à-faux formant un angle inférieur à 45° avec le plateau d'impression. | Modeling | |
Évitez les porte-à-faux de plus de 10 mm de longueur | Modélisation | Supporter les porte-à-faux avec des chanfreins qui respectent l'angle d'impression sans support. | |
Séparer la pièce en plusieurs parties à assembler | Modélisation | Intégrer dans les différentes pièces des formes facilitant l'assemblage (géométrie mâle-femelle) | |
Structure de support nécessaire | utiliser le même matériau que celui imprimé en 3D avec un profil d'impression adapté | Tranchage | |
Utiliser un matériau de support compatible avec le matériau imprimé en 3D et soluble dans un solvant. | Tranchage | Impression 3D avec un système ouvert pour sélectionner ou formuler un matériau compatible |
Plongeons dans les possibilités offertes par PAM
Des granulés à l'objet, la technologie PAM offre le processus le plus direct vers des pièces finales de haute performance.
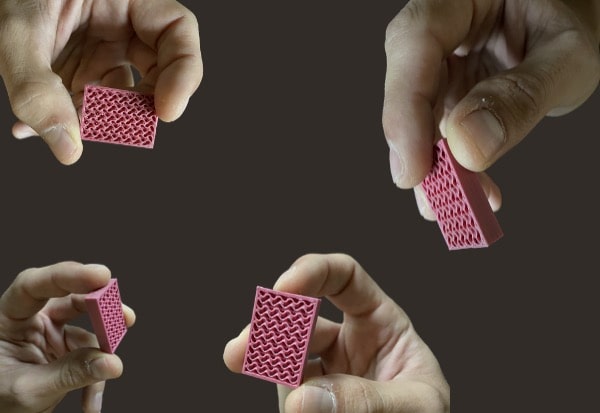
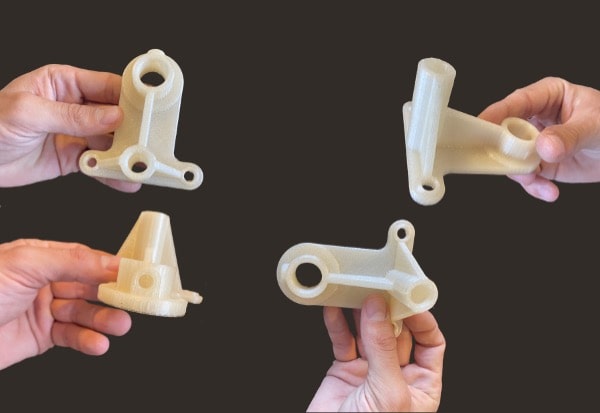
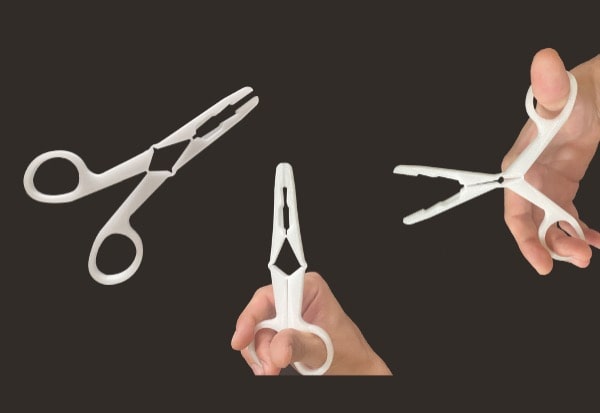
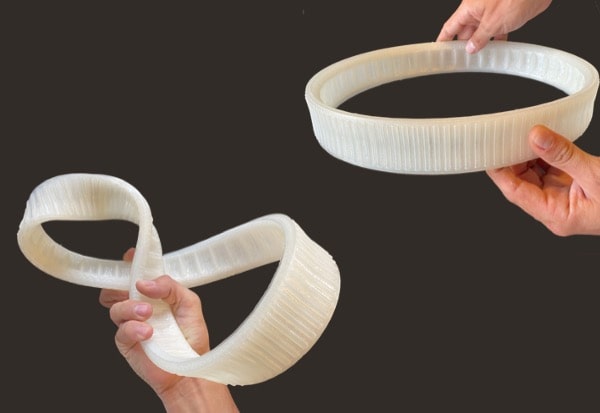
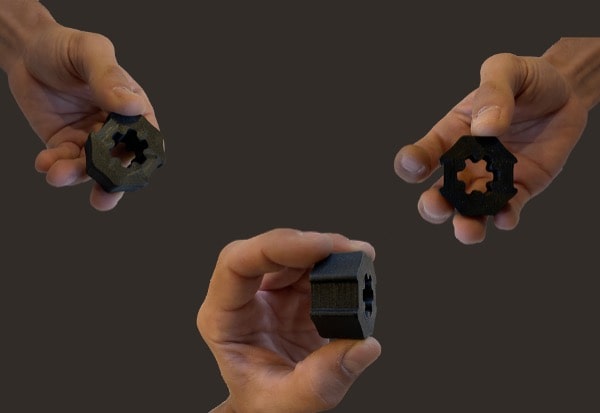